MONTH 2023
Robotics
Labor shortages are driving new demand for automation.
Options for Screwfeeding
The CubeStocker is a fully automated storage system for the carriers in which silicon wafers are transported and stored. Photo courtesy Stäubli Robotics
The six-axis robot is designed to operate in an ISO Class 2 clean room.
Silicon Wafers
Robot Automates Handling of
Ralf Högel // Contributing Writer
The dimensions of semiconductors on the surface of a silicon wafer are typically measured in nanometers. Any foreign particle, no matter how small, can impair the function of the microchip. That is why the 100 or so individual steps to produce a microchip take place in a clean room environment.
When the wafers must be stored temporarily, they must likewise be kept under clean room conditions. This is where the CubeStocker from Fabmatics GmbH comes in. Based in Dresden, Germany, Fabmatics specializes in the transport, storage and handling of silicon wafers in semiconductor production. Founded in 1991, the company employs some 250 people. When designing the company’s equipment, engineers focus on precision, reliability and the elimination of particulates.
The CubeStocker is a fully automated storage system for the carriers in which wafers are transported and stored. Each carrier can hold 25 wafers, and one CubeStocker holds 200 carriers. A conveyor system running along the clean room ceiling automatically feeds the carriers into and out of individual storage locations in the stocker unit. Depending on the application, the cell serves as an intermediate buffer in production or as a magazine for the test wafers used to measure, inspect, adjust and calibrate the equipment in semiconductor production.
A special feature of the CubeStocker is that it operates within its own ISO 3 clean room atmosphere. The wafers are thus temporarily stored in absolutely clean conditions before the next processing step or between test cycles, without any risk of contamination.
Super Clean Robot
Handling of the wafer carriers is performed by a six-axis clean room robot from Stäubli Robotics. To ensure that the robot can access all positions, it is mounted on a rigid dual-axis gantry. The additional axes allow it to stack carriers at floor level, as well as reach up to the conveyor level above the storage locations. This space-saving design enables the robot to pick up carriers from the conveyor and stack or retrieve them.
The Fabmatics design team opted for a Stäubli TX2-90XL with 1,450-millimeter reach in the company’s “super clean room” specification, which qualifies it for use in ISO Class 2 clean room environments.
In addition to the clean room specification, the other criterion guiding Fabmatics’ decision was the smooth motion of Stäubli robots. This is due not only to their proprietary high-precision drive technology, but also to the performance of the Stäubli CS9 robot controller.
“Wafers are fragile, and the value of the 25 wafers in a carrier is somewhere between 100,000 euros and the cost of a family home,” explains Martin Däumler, head of product development at Fabmatics. “Consequently, risk- and vibration-free handling, as well as precise positioning in the submillimeter range, must be ensured under all circumstances.”
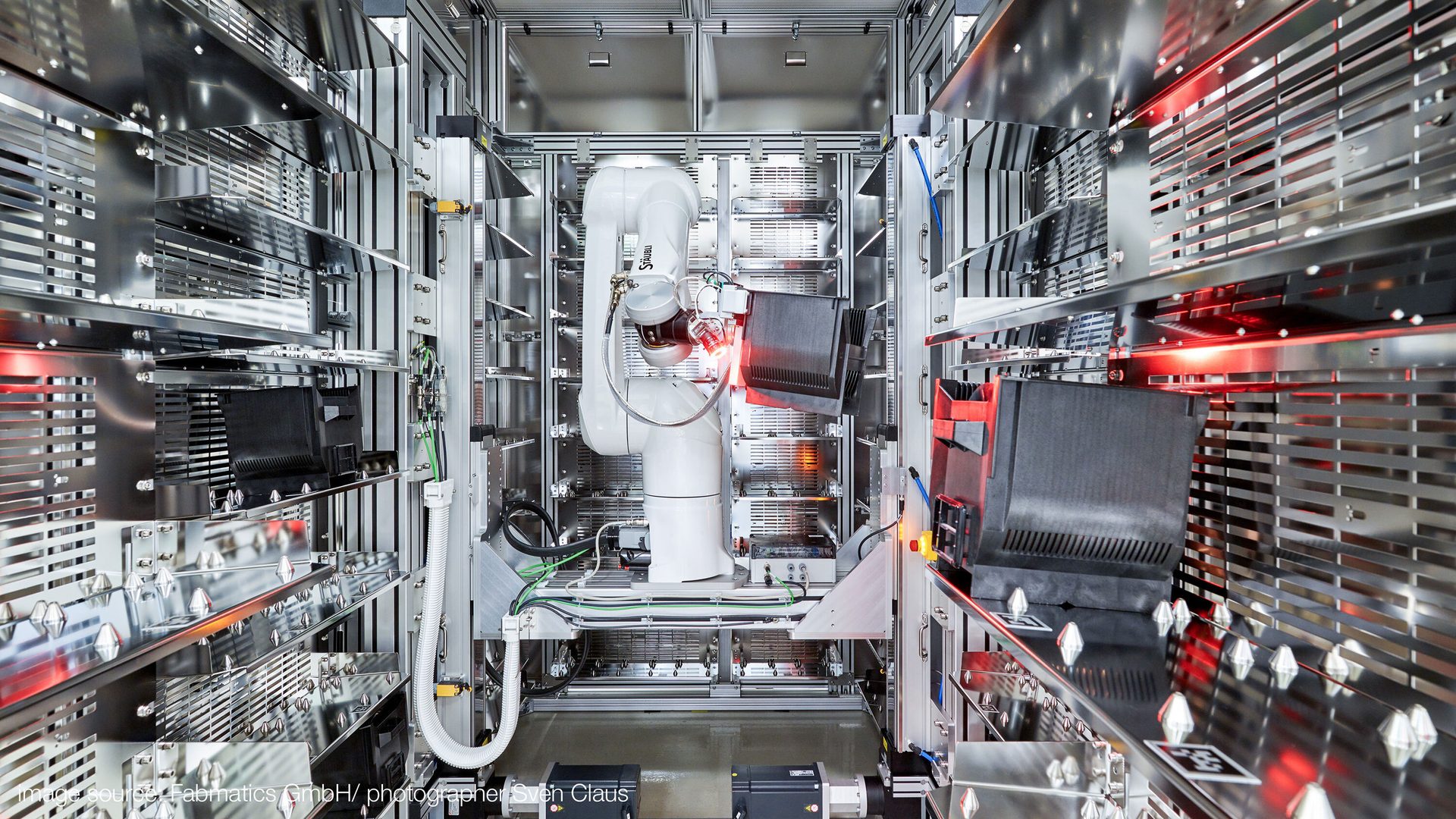
The dual-axis gantry of the CubeStocker enables the robot to easily access all storage locations. Photo courtesy Stäubli Robotics
Stäubli robots were an easy choice for the new machine, since Fabmatics had been already been using the robots in other applications for several years.
“We also use Stäubli robots in many other automation solutions,” says Roland Giesen, Ph.D., managing director at Fabmatics. “They meet our requirements for cleanliness, reliability and precision to the highest degree and enjoy a high level of acceptance among our customers. That is why we also chose a high-performance super clean room robot from Stäubli for the CubeStocker. In addition, we appreciate the collaborative and professional relationship…that has been in place for several decades and has been a vital factor in our growth.”
Industry interest in the CubeStocker has been strong from the start.
“The combination of a compact footprint, good integration into processes, and a built-in clean room atmosphere is unique,” says Däumler. “We have already completed multiple units, and one particular semiconductor manufacturer has ordered several of them.”
Moving forward, Fabmatics plans to create a family of products based on the CubeStocker. “We are currently working on a ‘Test Wafer Center,’” says Däumler. “This will add an area for single-wafer handling to the CubeStocker and allow users to assemble their wafer set for inspection cycles. It will be fully automated, ultra-precise and operate under clean room conditions.”
And, as with the CubeStocker, carrier handling in the new machine will be performed by a Stäubli super clean TX2-90XL robot.
For more information on robots, visit www.staubli.com.
Inspection System
ASSEMBLY ONLINE
For more information on robotic automation, visit www.assemblymag.com to read these articles: