ASSEMBLY LINES
American Manufacturers Continue to Invest in Robotics
CHICAGO—American manufacturers are investing in robots to improve productivity and boost quality. According to the International Federation of Robotics (IFR), total installations of industrial robots rose by 12 percent in 2023, reaching 44,303 units. The automotive industry continues to be the No. 1 adopter, followed by the electrical and electronics sector.
“The United States has one of the most advanced manufacturing industries worldwide,” says Marina Bill, president of IFR. “[Our first] outlook on preliminary results shows strong robotics demand across all major segments of U.S. manufacturing in 2023.”
Sales in the automotive segment rose by 1 percent, with a record number of 14,678 robots installed. This comes after installations in 2022 skyrocketed by 47 percent, reaching 14,472 units. Automotive OEMs and suppliers account for 33 percent of all industrial robot installations in the U.S.
“Automotive manufacturers currently invest in robotics mainly to drive the electric vehicle transition and respond to labor shortages,” explains Bill, group vice president for robotics and discrete automation at ABB Inc.
Manufacturers are investing in robots to improve productivity and boost quality. Photo courtesy Neura Robotics GmbH
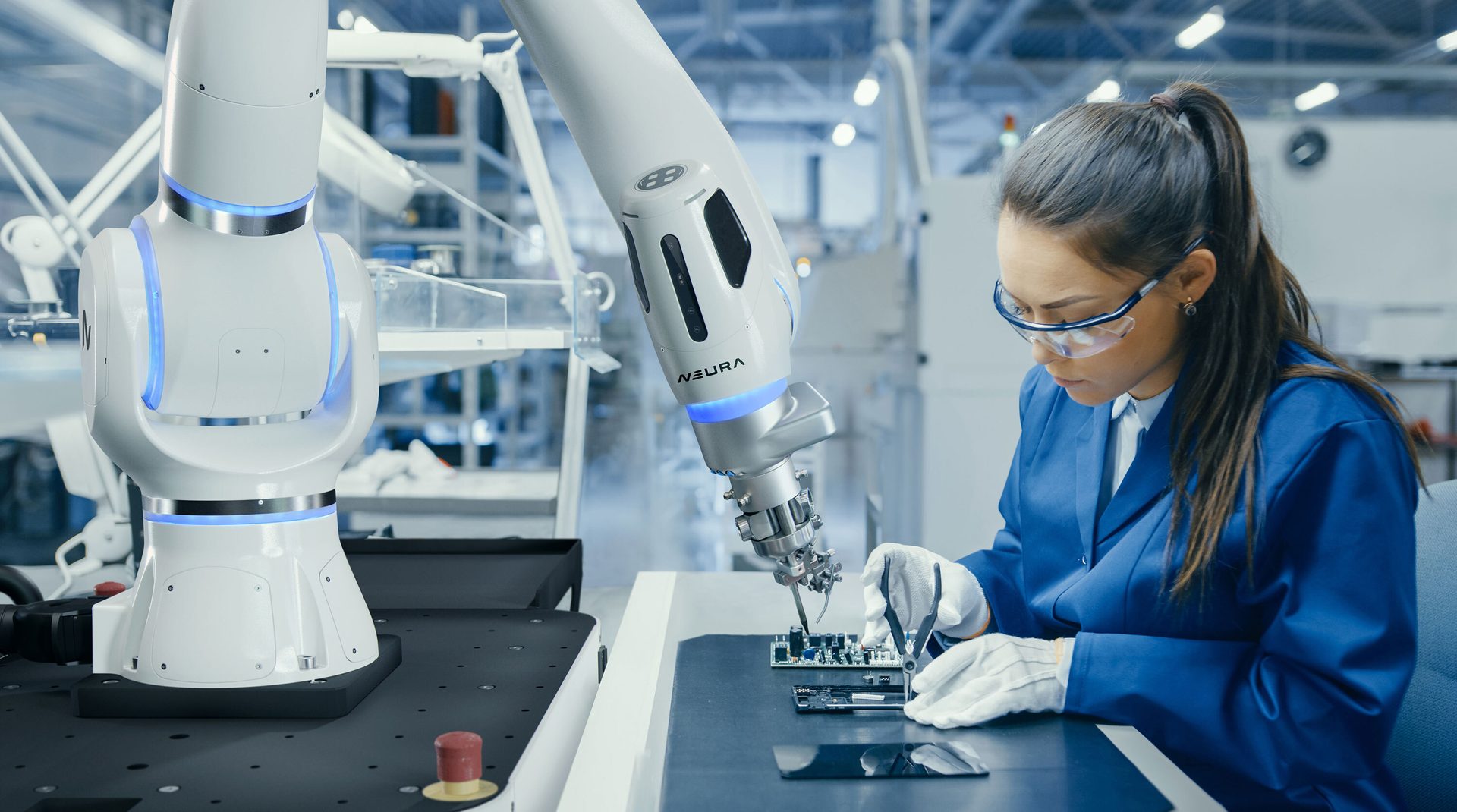
Installations in the electrical and electronics industry rose by 37 percent in 2023, to 5,120 units. This number almost reached the record pre-pandemic level of 5,284 units, seen in 2018. The latest result represents a market share of 12 percent of all industrial robots installed in the U.S. manufacturing industry.
Bill says demand for industrial robots in this segment is influenced by a trend to strengthen domestic supply chains and projects that drive the clean-energy transition.
Installation counts in other industries exceeding the 3,000 unit mark in the U.S. include metal and machinery (4,123 units, a 6 percent increase) and plastic and chemical products (3,213 units, a 5 percent increase). They represent a market share of 9 percent and 7 percent, respectively.
Robot installations in Canada reached 4,616 units in 2023, up 43 percent. The automotive industry accounts for 55 percent of the country´s robot installations. Sales to the automotive sector rose by 99 percent, with 2,549 units installed in 2023, which is an all-time high.
NIST to Launch AI-Focused Manufacturing Institute
GAITHERSBURG, MD—The U.S. Department of Commerce’s National Institute of Standards and Technology (NIST) plans to create a new Manufacturing USA institute focused on artificial intelligence technology. NIST anticipates that $70 million in federal funds will be invested in the initiative over five years, with an equal or greater contribution from private and other nonfederal funding sources.
“AI is an accelerator of our productivity and of human abilities,” says U.S. Secretary of Commerce Gina Raimondo. “It can make us better, faster and stronger in so many ways. I’m particularly excited about the potential for AI to supercharge manufacturing, and the ways it can strengthen American workers and businesses and make our country more competitive in the global economy.
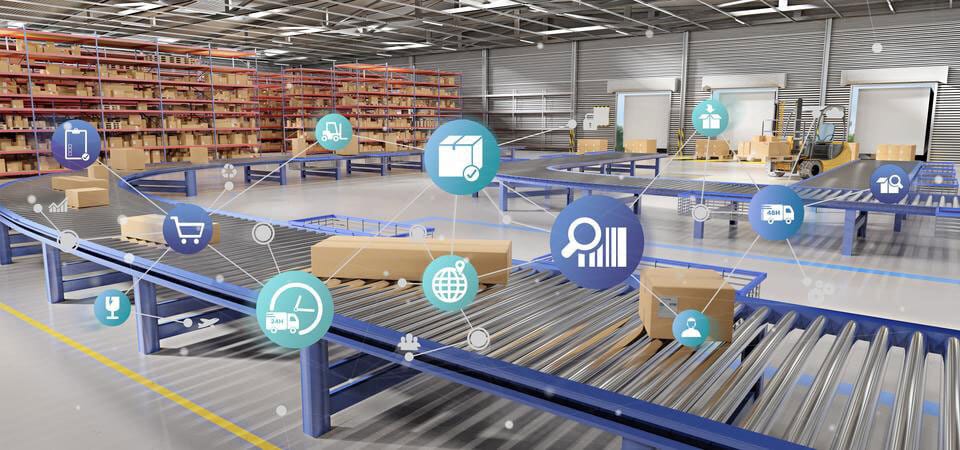
A new federal institute will help U.S. manufacturers stay competitive by applying artificial intelligence technology. Illustration courtesy National Institute of Standards and Technology
“Manufacturers that make smart use of AI to improve operational performance and strengthen supply chains will be more productive and resilient as they compete in an increasingly crowded global marketplace,” adds Under Secretary of Commerce for Standards and Technology and NIST Director Laurie Locascio. “We look forward to reviewing applications for a new Manufacturing USA institute that will strengthen the national economy by helping domestic manufacturers maximize the potential of AI.”
Manufacturing USA is a national network of institutes that brings together people, ideas and technology to solve advanced manufacturing challenges. All institutes are public-private collaborations focused on technology, supply chain, and education and workforce development.
According to Locascio, the AI institute will conduct R&D projects, establish employer-led sectoral partnerships to develop training resources, and create pathways for the skilled workforce needed to move innovation into industrial practice.
NIST plans to use a two-stage process for soliciting applications for the institute. Concept papers will be considered in the first stage of the competition. In the second stage, applicants with the best concepts will be invited to submit full proposals.
BMW Deploys Robo Dog to Monitor Production Equipment
HAMS HALL, England—A four-legged robot is roaming the plant floor at BMW’s engine factory here. “SpOTTO” is an autonomous “dog” that supports maintenance and ensures production processes run smoothly.
Equipped with visual, thermal and acoustic sensors, the machine is used to collect valuable data for the plant’s digital twin, while also serving as a watchdog overseeing operations. The data is used for quality assurance and production planning applications.
SpOTTO monitors the temperature of manufacturing equipment and immediately recognizes if an installation is running too hot, which is an early sign of potential failure. The robot also identifies leaks in compressed air lines, which helps identify waste and reduce energy consumption.
BMW is using a quadruped robot to support plant maintenance and ensure that production processes run smoothly. Photo courtesy BMW AG
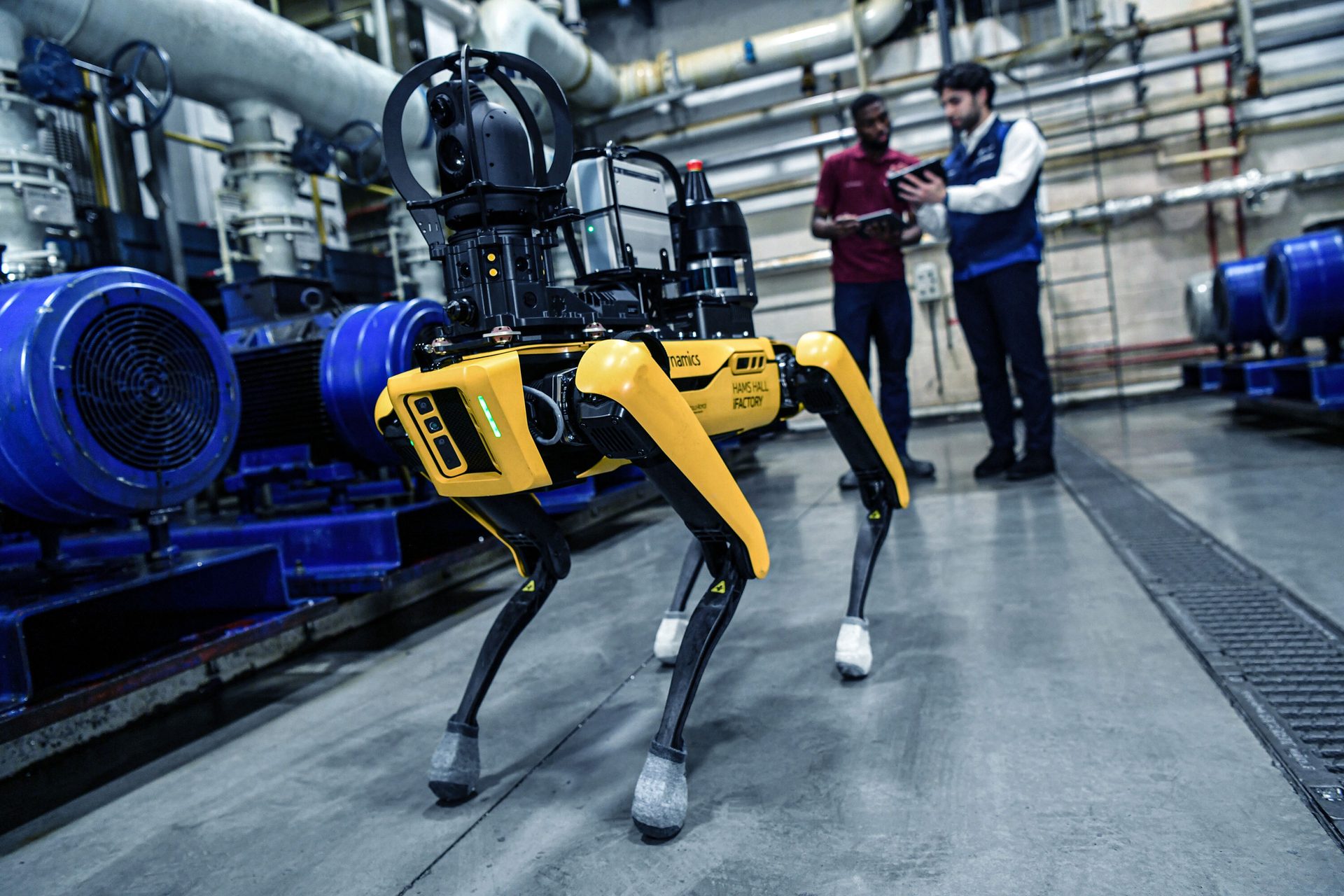
Future applications may include reading analog operating controls and accessing hard-to-reach areas of the factory.
“Thanks to the digital twin, we have an enormous quantity of precise data and evaluations, as well as a real-time picture of production processes,” says Dirk Dreher, plant manager. “The project team…has created unique use cases for our four-legged friend and integrated him perfectly into our processes.”
SpOTTO is named in honor of Gustav Otto, one of the founders of BMW and son of Nicolaus Otto, inventor of the four-stroke internal combustion engine.
NREL Automates Wind Turbine Blade Finishing Operation
ARVADA, CO—Engineers at the U.S. Department of Energy’s National Renewable Energy Laboratory (NREL) are using robots to improve the consistency of wind turbine blades. Although robots have been used by the wind energy industry to paint and polish blades, automation has not been widely adopted.
In the new application, a six-axis machine safely trims, grinds and sands blades. Those steps occur after the two sides of the blade are made using a mold and then bonded together.
Traditionally, post-molding operations require workers to perch on scaffolding and wear protective suits, including respiratory gear.
“This work is critical to enable significant U.S.-based blade manufacturing for the domestic wind turbine market,” says Daniel Laird, director of the National Wind Technology Center at NREL.
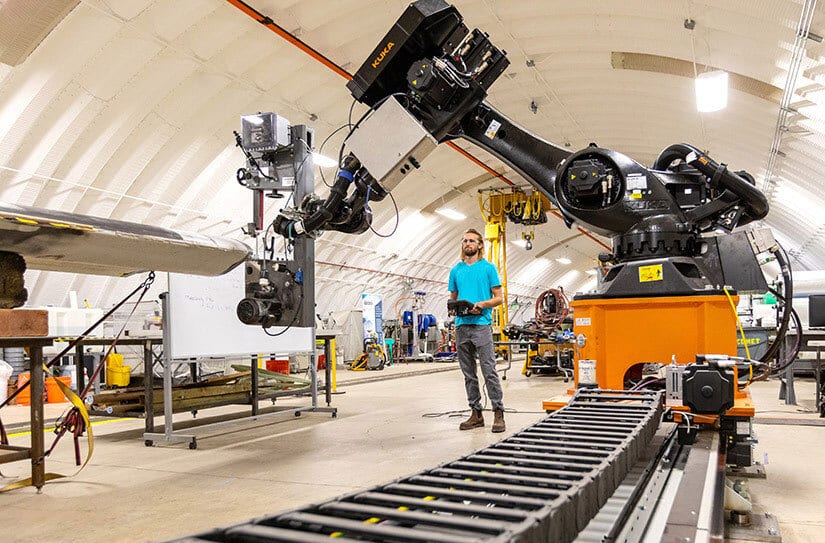
Robots can safely trim, grind and sand wind turbine blades. Photo courtesy National Renewable Energy Laboratory
“Though it may not be obvious, automating some of the labor in blade manufacture can lead to more U.S. jobs, because it improves the economics of domestic blades vs. imported blades.”
“The motive of this research was to develop automation methods that could be used to make blades domestically at a cost competitive price,” adds Hunter Huth, a robotics engineer at NREL who worked on the R&D project. “Currently, offshore blades are not produced in the U.S. due to high labor rates.
“The finishing process is very labor intensive and has a high job-turnover rate due to the harsh nature of the work,” explains Huth. “By automating it, domestic offshore blade manufacturing can become more economically viable.”
The research was conducted at NREL’s Composites Manufacturing Education and Technology facility. A six-axis robot worked on a 5-meter-long blade segment.
Wind turbine blades are considerably longer, but because they bend and deflect under their own weight, Huth says a robot would have to be programmed to work on the bigger blades section by section.
Huth and his colleagues used a series of scans to create a 3D representation of the position of the blade, and to identify precisely the front and rear sections of the airfoil. Then, they programmed the robot to perform a series of tasks, after which it was judged on accuracy and speed.
The engineers found areas for improvement, particularly when it came to grinding. For instance, the robot ground down too much in some parts of the blade and not enough in others.
“Not everything operated as well as we wanted it to, but we learned [how] to make it meet or exceed our expectations,” claims Huth.
“As we’ve gone through this research, we’ve been moving the goal posts for what this system needs to do to be effective,” says Huth.
According to Huth, an automated system would provide consistency in blade manufacturing that is not possible when humans are doing all the work. For instance, a robot would be able to use “tougher, more aggressive abrasives” than a human could tolerate.