MOSER ON MANUFACTURING
U.S. workforce demographics and weak manufacturing infrastructure are undermining our national defense goals. These deficiencies threaten our military readiness, national resiliency and global competitiveness. Having a larger, well-staffed U.S. manufacturing industry will provide a comprehensive framework to manage risk and support our national defense.
Recent data shows China-owned enterprises continue to be entrenched in the supply chains for critical defense-related products. Re-establishing domestic supply chains for these products is vital.
In the past, the U.S. military could call upon and employ a large domestic industrial base. America was able to switch gears and ramp up to manufacture essential items. For example, my father worked for Singer Sewing Machines, but during World War II his department produced bombsights.
The pandemic was a painful reminder that such reserve capacity no longer exists. As the United States enters an era of fierce global competition, workforce development and manufacturing infrastructure are essential.
Regarding infrastructure, a higher priority should be placed on manufacturing infrastructure rather than transportation infrastructure. In case of a war, our transportation system would be quite adequate. In contrast, experts agree that we would run out of artillery shells and missiles in a few weeks despite a current multiyear plan to double production.
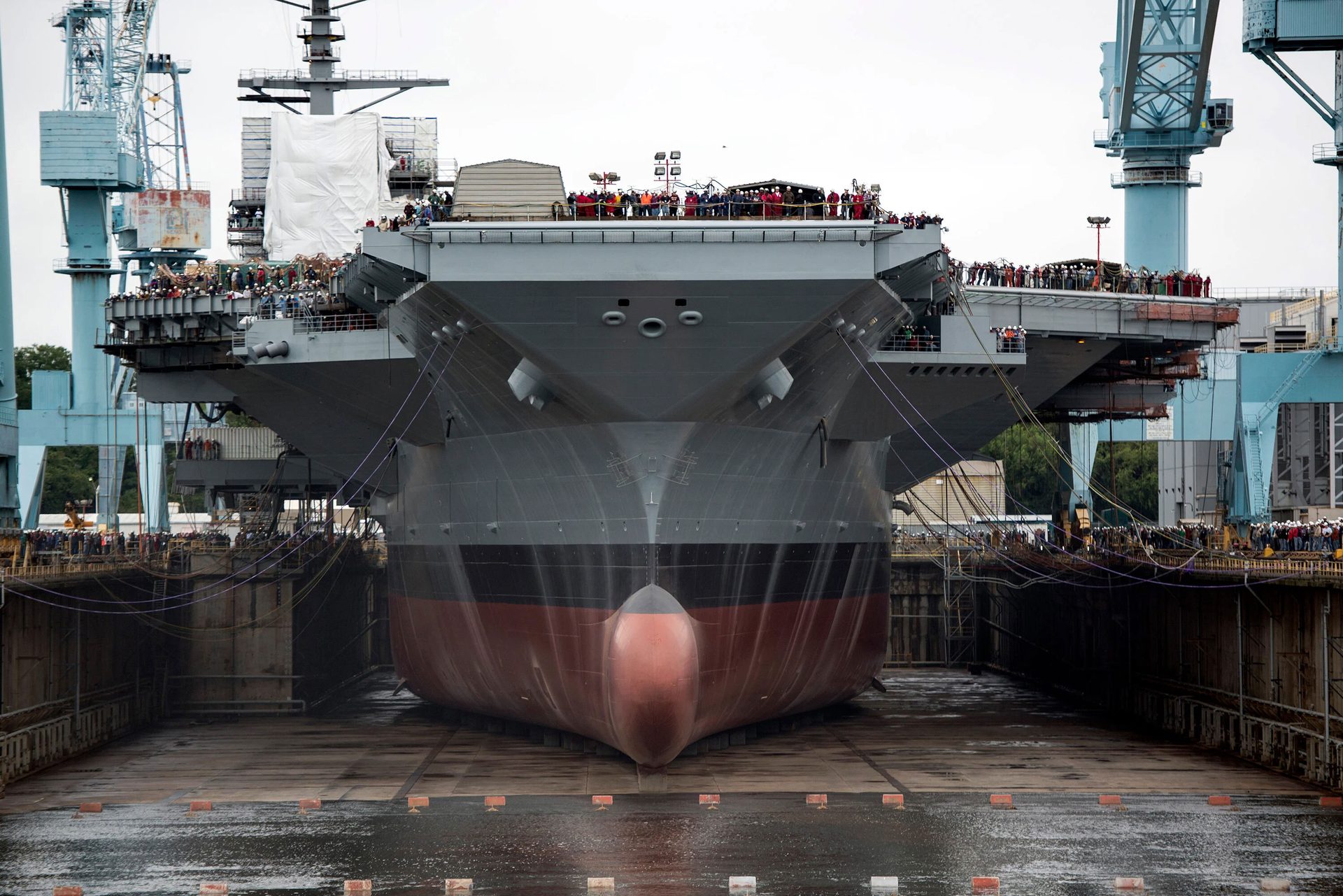
The Navy’s shipyards report that it is nearly impossible to find qualified pipe fitters, plumbers and welders for repairs and maintenance. Photo courtesy U.S. Navy
Skilled Workforce—No Small Challenge
Infrastructure aside, senior military officials say their No. 1 quagmire is hiring and retaining skilled employees. The Navy’s shipyards report that it is nearly impossible to find qualified pipe fitters, plumbers and welders for repairs and maintenance.
Matthew Paxton, president of the Shipbuilders Council of America, told the House Armed Services Committee that the No. 1 challenge the nation’s private shipyards face is the ability to attract and retain a proficient workforce to deal with the changing demands of their government customers.
In testimony to the same committee, former deputy defense secretary and current president and CEO of the National Defense Industrial Association David Norquist noted that just 1.1 million Americans are employed in the defense industry, compared to 3 million in 1985.
Creating a pipeline of skilled workers is therefore critical to our national defense goals. To achieve this, a national mind shift is needed. We must promote skills-based education and demonstrated proficiency as pathways to the high-paying new-collar careers of the future.
According to a report from Jobs for the Future, 81 percent of employers think they should be hiring based on skills rather than degree. Recently, companies like Google, IBM, Accenture, and others are putting greater emphasis on skills-based hiring and dropping some degree requirements. According to a recent Harvard Business Review study, this reset could have major implications for how employers recruit new talent.
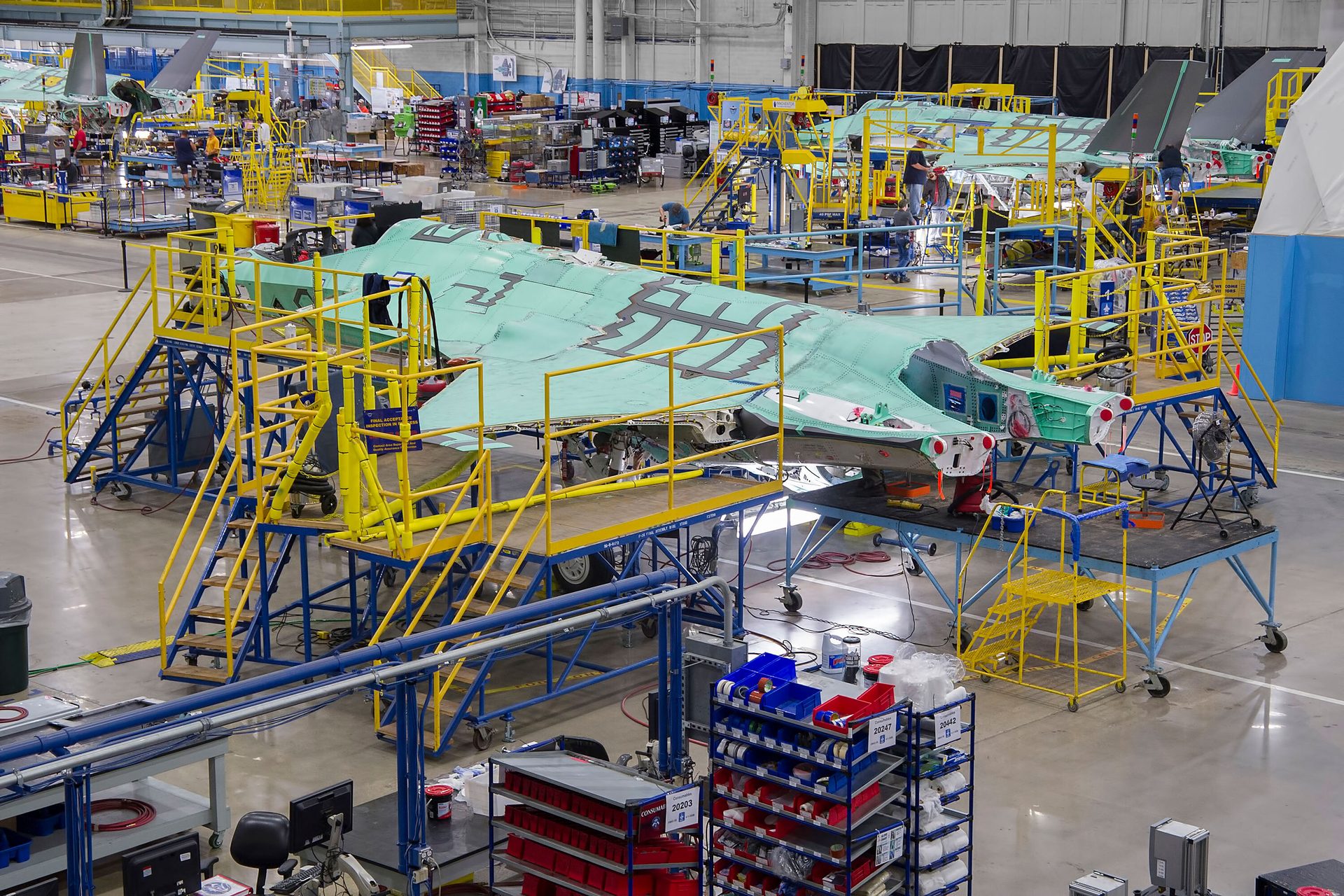
Having a larger, well-staffed U.S. manufacturing industry will provide a comprehensive framework to manage risk and support our national defense. Photo courtesy Lockheed Martin
Keeping Up
Advanced manufacturing technologies are just as important as a skilled workforce to maintaining a strong national defense.
Collaborations between universities and manufacturers are helping. For instance, Tetramer Technologies is collaborating with the University of Chicago on a $1 million U.S. Army project to expand the capabilities of infrared photodetectors used in military applications like night vision and thermal imaging. The upshot of the project will be manufacturing process improvements that will reduce costs and improve performance for civilian applications.
The government is also helping. For example, the Defense Department operates nine of the 17 U.S. Manufacturing Innovation Institutes. These institutes are engaged in research and development, growing our manufacturing ecosystems, and providing education and workforce development. For example, the DOD is forming a domestic supply chain for critical materials used in both commercial products and military systems. The Pentagon has awarded $440 million to establish a domestic supply chain ecosystem for “mine to magnet” rare earth elements by 2027.
The $1.2 trillion Bipartisan Infrastructure Law directs federal funds toward infrastructure and competitiveness spending, including $800 million dedicated for workforce development. The $280 billion CHIPS and Science Act appropriates $52.7 billion to revitalize the U.S. semiconductor industry, including a $200 million Workforce and Training Fund. The goal is to train 100,000 new technicians through apprenticeships, career and technical education, and career pathway programs, over 10 years.
Larry Fink, chairman and CEO of BlackRock, world’s largest investment firm, said this about infrastructure investments: “Infrastructure is one of the most exciting long-term investment opportunities, as a number of structural shifts reshape the global economy. We believe the expansion of both physical and digital infrastructure will continue to accelerate, as governments prioritize self-sufficiency and security through increased domestic industrial capacity, energy independence, and onshoring or near-shoring of critical sectors.
What You Can Do
Improving our industrial base to support national defense is not solely the province of the federal government, however. Manufacturers in any industry can help simply by bringing more work back from other countries. Using the “total cost of ownership” model, companies can reshore 20 or 30 percent of what is now imported without impacting margin or price.
Military readiness, global competitiveness, and continued reshoring success all require a resilient infrastructure and a larger, well-staffed U.S. manufacturing industry. Let’s collaborate to support skilled workforce development and rebuild the U.S. manufacturing base. To get help or to give help, contact me at 847-867-1144 or harry.moser@reshorenow.org.