ASSEMBLY LINES
BMW Conducts Successful Test of Humanoid Robots
SPARTANBURG, SC—BMW engineers recently conducted a test with humanoid robots at its assembly plant here. They used a Figure 02 machine made by FigureAI Inc.
The robot successfully inserted sheet metal parts into specific fixtures, which were then assembled as part of the chassis. It saved humans from having to perform ergonomically awkward and tiring tasks.
“The developments in the field of robotics are very promising,” says Milan Nedeljković, a member of the board of management for production at BMW AG. “With an early test operation, we are now determining possible applications for humanoid robots in production. We want to accompany this technology from development to industrialization.”
During the trial run, BMW engineers focused on how to integrate multipurpose robots into an existing production system, including how humanoids communicate with it under real conditions.
BMW recently conducted a test of humanoid robots in its body shop. Photo courtesy BMW Group
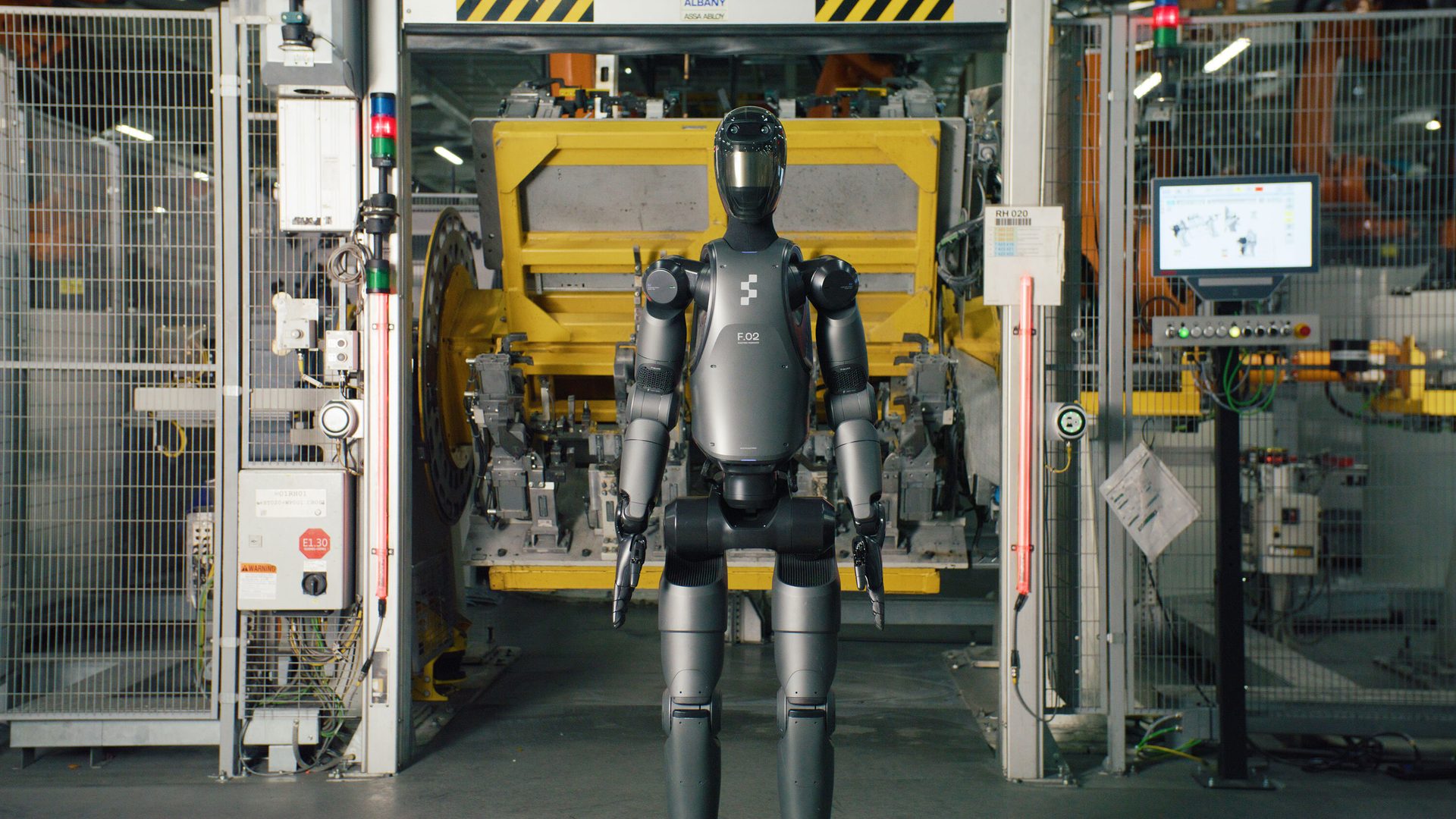
“Figure 02 has significant technical advancements, which enable the robot to perform a wide range of complex tasks fully autonomously,” says Brett Adcock, CEO of FigureAI, who claims the machine is “the world’s most advanced humanoid robot currently available on the market.”
The combination of two-legged mobility and advanced dexterity means that Figure 02 is ideally suited for use in areas with physically demanding, unsafe or repetitive processes. According to Adcock, the next-generation machine features three times the processing power of its predecessor, improved voice communication, and better cameras, microphones and sensors.
The robot is capable of fully autonomous execution of human-like, two-handed tasks requiring varied and dynamic manipulation, complex grasping and coordination of both hands in unison.
Toyota Programs Focus on Workforce Development
GEORGETOWN, KY—Toyota Motor Co.’s flagship assembly plant here recently unveiled several workforce readiness initiatives. The goal is to develop future talent and upskill current assemblers who build popular vehicles such as the Toyota Camry and RAV4.
Toyota Motor Manufacturing Kentucky is the automaker’s largest vehicle plant in the world and employees nearly 10,000 people.
“Our most valuable assets are our team members—they are our heart,” says Kerry Creech, president of Toyota Kentucky. “That’s why we continuously invest time and resources into developing our people and providing students with strong career pathways for our future.”
As part of that effort, the facility is working with Scott County Schools and investing up to $1 million to launch and sustain the 4T Academy (Team, Teach, Together, Toyota), a hands-on training program that will provide high school juniors and seniors with a direct pathway to a manufacturing career.
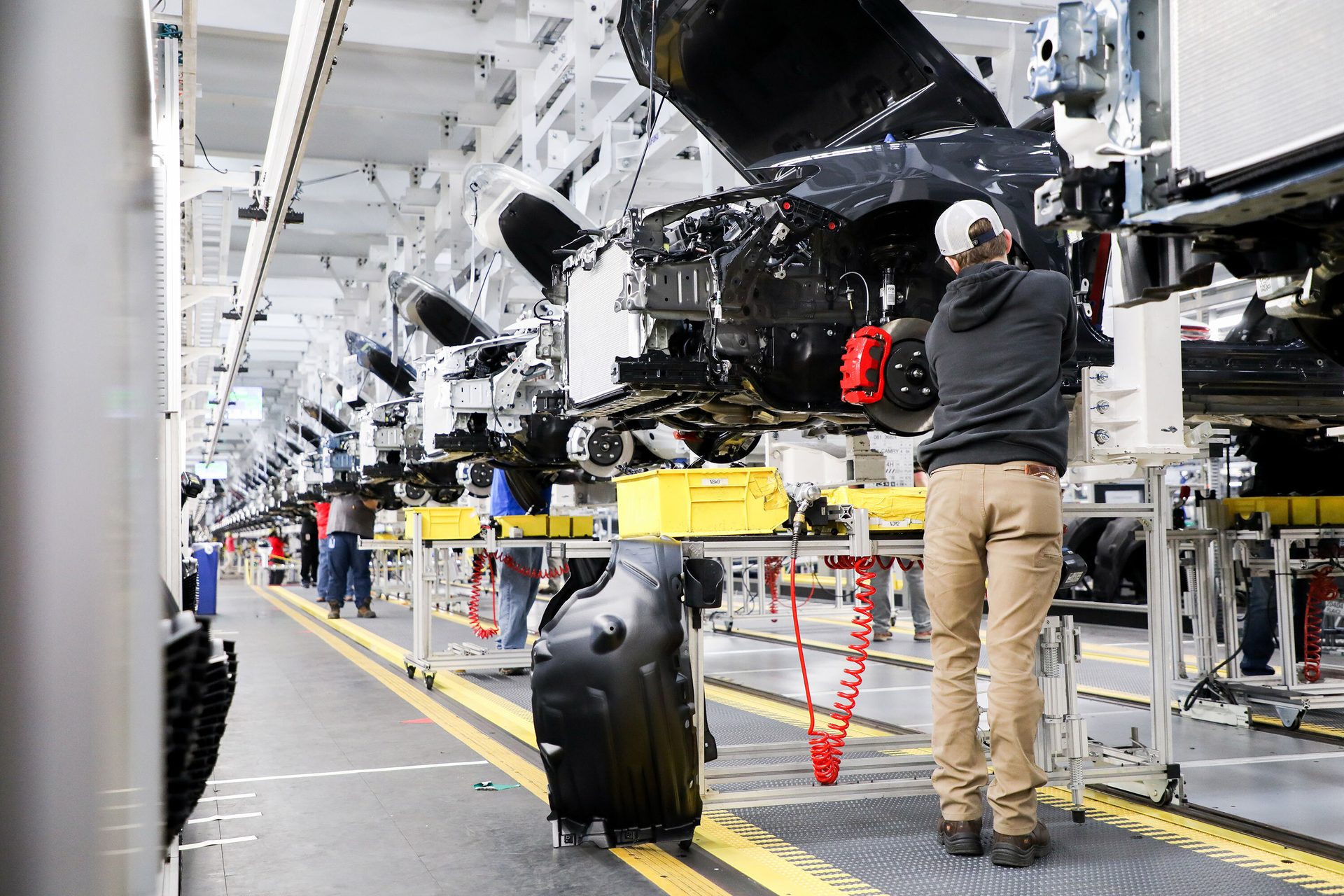
Toyota Motor Co. has launched several workforce development initiatives at its flagship assembly plant. Photo courtesy Toyota Motor Co.
Students in the program will follow a state-approved curriculum in traditional high school classes, while learning and training in a simulated factory environment. 4T Academy will house a collaborative classroom space, electric and pneumatic tool training stations, a simulated vehicle production line and many other high-tech components. Seniors enrolled in 4T Academy will earn around $18 an hour while working alongside industry experts at Toyota's assembly plant.
Toyota Kentucky also recently celebrated the one-year anniversary of its Driving Possibilities program in partnership with schools in Fayette and Scott Counties. As a next step in its strategic plan, Toyota is providing 10 Sienna vehicles to local schools to help meet student transportation challenges.
Driving Possibilities focuses on ways to expand literacy and language resources, build education and industry partnerships, and address transportation barriers. The career readiness initiative aims to close educational gaps through hands-on science, technology, engineering and math programming, while addressing the essential needs of students and families.
In addition to developing its future workforce, Toyota Kentucky continues to invest heavily in its current employees. For instance, it is opening a new 20,000-square-foot, $3 million onsite training center that will enable assemblers to learn about new technologies and advanced manufacturing processes.
Cyberattacks Are Huge Threat for All Manufacturers
CHICAGO—Manufacturing is the most targeted sector worldwide for cyberattacks. To address the issue, MxD (Manufacturing x Digital) and the National Center for Cybersecurity in Manufacturing recently created a report on the topic. According to “Behind the Firewall,” many manufacturers are overestimating their capabilities.
“The supply chains that support U.S. manufacturing are only as strong as their weakest link,” warns Berardino Baratta, CEO of MxD. “We must strengthen at every level to ensure a resilient domestic manufacturing capability, including within the defense industrial base.
Both large and small manufacturers are increasingly vulnerable to cyberattacks. Photo courtesy Rockwell Automation
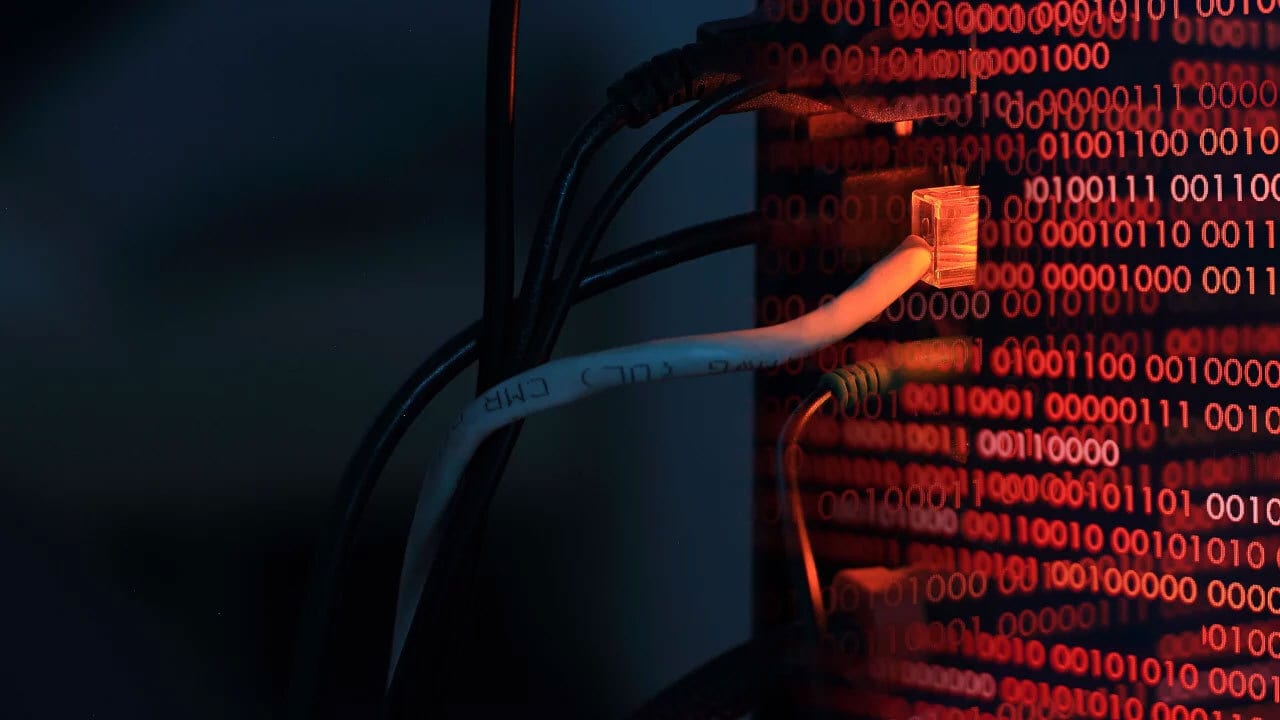
“We see a sense of overconfidence in our research results, which is concerning,” says Baratta. “Everyone is at risk, from the largest multinational to small- and medium-sized manufacturers that often lack the proper resources to protect themselves from cyberattacks.”
“Manufacturing sector cyberattacks are no longer rare, one-off events," adds Michael Tanji, director of cybersecurity at MxD. “The rise in incidents shows repeated and concerted efforts to steal intellectual property or other company data, resulting in production shutdowns, logistical delays and more.
“Our manufacturing sector must stay ahead of these growing threats,” claims Tanji. “We can only do that by updating and upgrading cyber capabilities across the industry."
Nissan Rogue Named ‘Coolest Thing’ Made in Tennessee
FRANKLIN, TN—The Nissan Rogue was recently named the “Coolest Thing Made in Tennessee.” The online popularity contest was sponsored by the Tennessee Manufacturers Association.
The Rogue is a midsized crossover vehicle that’s assembled at Nissan’s 41-year-old factory in Smyrna, TN. It’s powered by engines built at Nissan’s power train plant in Decherd, TN. In addition to the Rogue, Nissan Smyrna produces vehicles such as the Leaf, Murano and Pathfinder.
The Nissan Rogue was recently named the “Coolest Thing Made in Tennessee.” Photo courtesy Nissan Motor Co.
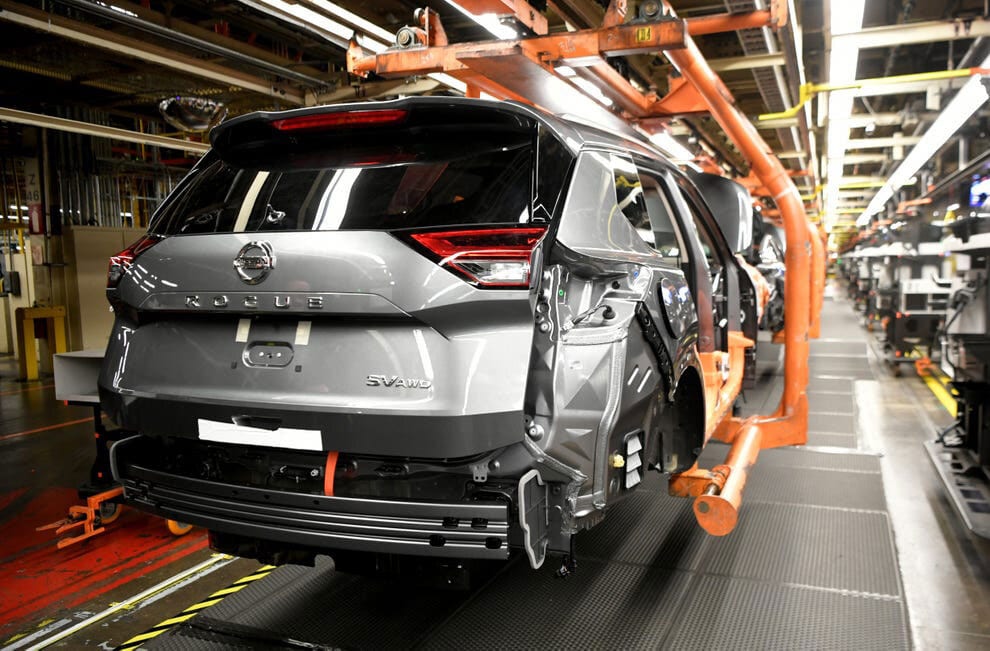
“Our [employees] put their heart and soul into the Rogue, and this award is a huge validation of their hard work,” says Brian Crockett, vice president of manufacturing at the Smyrna Vehicle Assembly Plant. “They have helped make the Rogue a standout vehicle, and this achievement shows just how much passion and effort they exhibit every day. It’s incredible to see their efforts recognized like this.”
The inaugural “Coolest Thing Made in Tennessee” competition received more than 100 nominations, highlighting the diversity of the state’s manufacturing sector. The Rogue advanced through three competitive rounds of voting to claim the top spot with more than 75,000 votes from residents of the Volunteer State.
Other companies nominated for the award included Bell Textron Inc. (helicopters), Eaton Corp. (safety switches), John Deere (zero-turn mowers), Smith & Wesson (pistols) and Volvo Penta Marine Products (outboard engines).