FEATURE
UV-LED Curing for Insertable Medical Devices
UV LED Curing for Insertable Medical Devices
By Peter Cop, Senior Product Manager, OmniCure and Roy Kayser, Senior Manager, Global Applications & Custom Projects, Excelitas Technologies
UV LED systems offer the potential for improved performance of established and new designs of insertable medical devices.
Catheters and other insertable medical devices are long, flexible, tubular instruments inserted into the body during minimally invasive medical procedures. These devices are used to extract substances, remove clots, deliver drugs or insert stents as part of angioplasty or neurovascular coronary treatment. They can also guide wires for other essential interventions and diagnostic and monitoring procedures. Catheters are widely used and represent a large and growing market, with an estimated 2022 global market size of $23.1 billion. With aging populations in need of increasingly complex medical procedures, the market is expected to grow at a rate of 8.7% and reach $54.7 billion in 2032.1
The application of hydrophilic outer coatings to medical catheters is a key manufacturing process that enhances lubricity of the device, which enables easier and safer navigation of veins and arteries. While many manufacturing processes use heat-cured coatings, ultraviolet (UV) curable coatings provide significant benefits to medical device manufacturing such as ultra-fast, uniform and complete curing of the coating with minimal stress effects and low volatile organic carbon (VOC) emissions. Although there are several UV light source options for curing systems, compact and efficient UV LED systems offer several cost-saving advantages including decreased demand for facility space, minimal heat generation at the curing site, reduced downtime, and reduced energy consumption. These systems also offer the potential for improved performance of established and new designs of insertable medical devices.
Heat Curing of Catheter Coatings
Many catheters are made of multiple layers of metals, nanowires, and plastic-like materials depending on their application. The materials used in the device are often, but not exclusively, extruded into the desired shape, laser cut and tipped, and braided or reinforced. However, most of these materials are usually hydrophobic and friction-inducing, which make them difficult to insert into the human body. Therefore, catheters are usually coated with a thin, hydrophilic and biocompatible hydrogel polymer that is durable, flexible, and mechanically and chemically stable. These coatings are also engineered to become lubricious, or slippery, when in contact with bodily fluids to simplify the use of the catheter and minimize tissue damage and patient discomfort, while also enabling easier targeting of complex areas of the human body.
Many manufacturers use heat curing to treat and cure hydrophilic outer catheter coatings. The in-process catheter surfaces are cleaned, dip-coated or brush-coated with a thin layer of lubricious material, then hung vertically and heat cured in ovens typically at 60 °C for 30-60 minutes. While a reliable and proven method, heat curing of catheters has some drawbacks as it employs large, tall ovens that consume facility space, significant amounts of electrical power, and require heat management. As the curing proceeds, the coating compounds typically emit VOCs that require complex ventilation systems and scrubbers in production facilities to comply with EN14001. Heat curing also limits the type of materials that can be used in a catheter since they must be resistant to heat during the curing process.
Balloon catheter example. Image: Christoph Burgstedt / iStock / Getty Images Plus.
Options for UV Curing
Curing with high-intensity UV light sources solves many of the challenges related to heat curing of the outer coatings of insertable medical devices. To employ UV curing, standard heat-cured outer coatings are replaced by equivalent UV-curable materials. These coatings include an appropriate concentration of photoinitiators that absorb UV light and initiate a series of chemical reactions that harden the material in just a few seconds. Many such commercially available UV-curable coatings for medical devices combine a lubricious hydrogel polymer with UV-sensitive photoinitiators that deliver comparable or even superior performance compared to heat-cured coating materials.
There are three primary UV light sources for curing systems — mercury arc lamps, electrodeless microwave lamps, and UV light-emitting diodes (LEDs). These high-intensity UV sources are widely used in many industries, including printing, electronics, and industrial materials, with each having its own advantages and disadvantages.
Mercury arc lamps, the most established of the UV-curing sources, emit light in the range 250 nm to >1,000 nm, and many UV-curable adhesives and polymers are designed to work at wavelengths produced by the energized mercury atoms in these high-pressure lamps. Mercury arc lamps have several disadvantages including high power consumption, high cost of operation and maintenance, and the need for ventilation to remove ozone from the work area. Mercury lamps generate and deliver unwanted heat in the form of infrared light to the curing site, which can cause product shrinkage and deformation. These lamps also have a fairly short lifespan of several hundred to several thousand hours, and after their service life, require proper disposal to prevent toxic materials from entering the environment.
Microwave (or electrodeless) lamps emit light in the range 250 nm to >1,000 nm, typically have longer lifespans than arc lamps since electrodes are a major wear mechanism and have a rapid start capability. However, electrodeless lamps produce significant amounts of unwanted UV light through a microwave-induced plasma stream. They also require a large amount of energy to operate, produce ozone that must be vented, and the systems are large and bulky.
Figure 2: Balloon catheter in situ. Image: Christoph Burgstedt / iStock / Getty Images Plus.
UV LED Curing
The use of UV LED-based curing systems can mitigate many of the disadvantages of UV lamp-based systems. As compact semiconductor devices, similar to lasers, UV LEDs convert electrical current to light over a narrow range of wavelengths. These devices leverage decades of advances in electronics and optics for telecommunications, an industry that demands high performance and reliability. In a UV LED curing system, hundreds of tiny UV LEDs are integrated into an addressable modular system with drive and monitoring electronics along with an optical delivery system to shape light from the LEDs into a uniform beam delivered to the curing site.
A single compact UV-LED curing system, for example, can produce high-intensity UV light with an irradiance of 10-30 W/cm2 UV light over an area of 300 mm x 25 mm with a uniformity of +/-10% at a working distance of 5-20 mm. Since UV LED curing systems are compact with respect to their counterpart arc lamp-based systems, these devices are easily combined into customized larger curing systems that deliver UV light to the curing site. UV LEDs can be engineered to operate in tight spectral bands at, for example, 365 nm, 385 nm, 395 nm, and 405 nm, that work with many UV-curable coatings already on the market as well as new materials specially optimized for UV LED curing. More recently, LED area curing sources that emit in the UVC spectrum (220-280 nm) at wavelengths such as 275 nm, have also recently emerged to help cure the top surface of some UV-curable formulations.
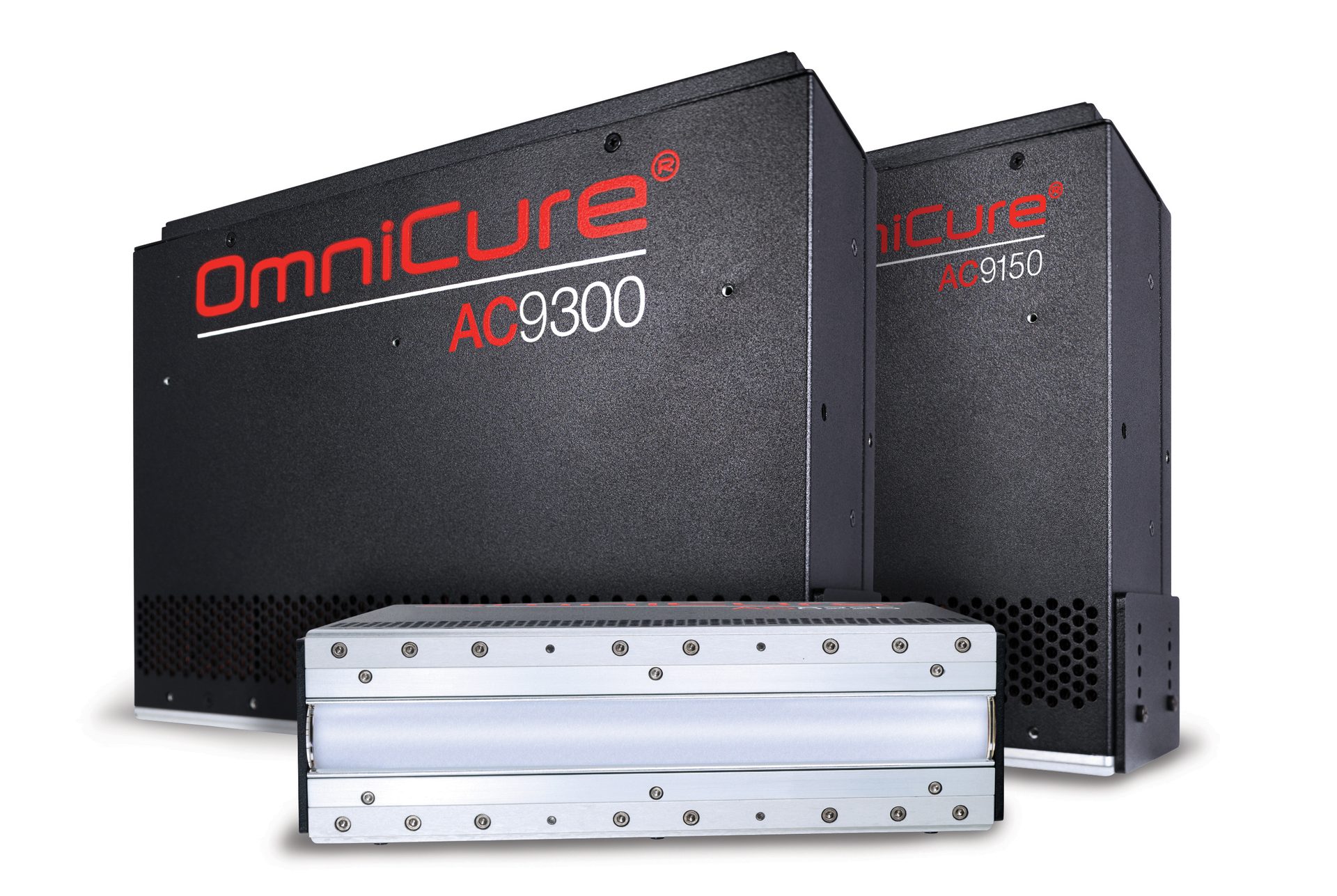
Figure 3. The OmniCure® AC9 Series UV-LED curing system is used for medical catheter coating applications.
Advantages of UV LED Curing
Compared to heat curing, UV LED curing systems have many advantages that offer the potential of substantial savings in manufacturing costs as well as a more environmentally friendly manufacturing process. With a power consumption of 1,000-2,800W per system, they require less electrical power than traditional heat curing due to their much higher energy efficiency. UV LED curing systems do not generate significant heat and therefore do not require complex heat exhaust systems. As UV-sensitive catheter coatings cure, they emit virtually no VOCs, reducing the need for complex and expensive scrubbers and ventilation systems.
Adding to this, UV LED curing systems prevent damage and heat-induced stress on the cured part, an essential consideration when curing critical components such as catheters and insertable devices made from soft, heat-sensitive plastics. Low-heat-curing processes also enable the use of new catheter coating materials that have not been traditionally used for heat curing. These factors make UV LED curing systems ideal for the development of new insertable medical devices within a laboratory R&D setting.
Beyond the advantages that UV LED curing systems offer over traditional heat and arc lamp-based curing systems, these systems also deliver advantages over lamp-based UV curing systems. Unlike UV arc lamps, UV LED systems produce no ozone and relatively little heat, reducing the need for ventilation systems. They have a longer service life (more than 20,000 hours), which minimizes the expense of downtime and the cost of replacement parts. Additionally, with a wall-plug efficiency of typically 20-40%, UV LED curing systems are much more energy efficient than lamp-based UV systems, leading to lower operational costs and a more environmentally-friendly curing solution that conforms to EN14001 standards.
Integrating UV LED Curing in Production Systems
The compact size and relative ease of customization of UV LED curing systems enable a range of options for integration into catheter development and volume-production facilities. These curing systems can be incorporated into a conveyor system or a stationary linear system in a face-to-face configuration to facilitate highly uniform UV curing around the circumference of the part in new production facilities. To save space and energy for a boost in overall productivity and efficiency, they can also be easily retrofitted into older facilities. Replacing other curing techniques with UV LED curing is often as simple as replacing the heat-curable hydrogel coating with a UV-curable coating, and there are many options on the market that result in a final product with the same or better performance than heat-cured coatings.
Summary
In conclusion, UV LED curing systems offer an environmentally friendly and cost-effective alternative to heat curing of the outer hydrophilic coatings of catheters and insertable medical devices. These systems have the potential to simplify production and development environments by providing fast and efficient curing of commercially available UV-curable coatings with minimal extraneous heat and virtually no VOC or ozone production. UV LED curing technology can also enable development of new catheter designs that are not amenable to heat curing.
References
1. https:gminsights.com/industry-analysis/catheters-market
To learn more about Excelitas Technologies Corp., visit www.excelitas.com.
Cover image courtesy of ivan68 / iStock / Getty Images Plus.