FEATURE
Silane Terminated Polymer Reactions with Non-Tin Catalysts
Silane Terminated Polymer Reactions with Non-Tin Catalysts
By John Florio, Dymin Morillo, and Dylan LaFerriere of King Industries, Inc., USA
Research demonstrates the performance of non-tin catalysts as a replacement for tin, satisfying regulatory concerns and performance requirements.
VIEW FIGURE 1

Figure 1: Organosilane coupling agent.
Polymers based on organosilane chemistries are widely used in a variety of applications including adhesives, sealants, and coatings. Organosilanes are capable of forming covalent bonds between organic and inorganic compounds. They are gaining interest as alternatives to more hazardous chemistries, for example, polyurethane applications that use hazardous polyisocyanates. Organosilane polymers can promote adhesion, weatherability, and reinforcement of coatings, adhesives, sealants, and fillers. Hence, they are widely used for DIY projects and commercial construction projects for a variety of indoor and outdoor applications on a variety of substrates.
Organosilanes can be designed as coupling agents that form links between inorganic substrates and organic polymers (Figure 1). In some cases, organosilane coupling agents can act as co-catalysts to provide a synergistic effect with certain other more conventional catalysts.
VIEW FIGURE 2

Figure 2: Basic silanol condensation reaction forming siloxane and volatile byproduct.
Organosilane crosslinking chemistries include one-component moisture cured systems that can be based on different functionalized backbone polymers that have alkoxysilane terminal groups. The backbone chemistries of these systems could be polyether, polysiloxane, or polyurethane.
Organosilane polymers can crosslink with other functional groups to form products with structural properties through a variety of mechanisms that involve two basic reactions: hydrolysis of alkoxysilane groups and condensation of formed silanol groups with other silanol groups or with alkoxysilane groups. The product of the condensation reaction is a crosslinked siloxane (-Si-O-Si-). The basic silanol condensation reaction mechanism forming a siloxane and a volatile byproduct is shown in Figure 2. The volatile byproducts are sometimes a limiting factor for some applications. All of these reactions can be accelerated by several different catalyst mechanisms. The curing process can be very complex, with cure rates dependent on several variables.
VIEW FIGURE 6
VIEW FIGURE 5
VIEW FIGURE 4
VIEW FIGURE 3

Figure 6: Condensation of silanol and alkoxysilane, siloxane formation.

Figure 5: Condensation of silanol, siloxane formation.

Figure 4: Hydrolysis of dialkoxysilane, silanol formation.

Figure 3: Dialkoxysilane polymer.
This article initially reviews the crosslinking process of alkoxysilane terminated systems, followed by an in-depth summary of different catalyst processes for organosilane chemistries. Finally, catalyst evaluations of three organosilane chemistries is presented to address tin catalyst environmental and toxicity issues.
Crosslinking Organosilane
Figure 3 shows a basic structure for a dialkoxysilane polymer. Both hydrolysis and condensation processes are involved in curing one-component moisture-cure alkoxysilane systems, and the reaction rates for both processes can be increased by incorporating acid, base, or organometal catalysts. Figure 4 shows a sequence for the hydrolysis of a dialkoxysilane generating a silanol and two moles of alcohol byproduct. Siloxane generating condensation reaction mechanisms are shown in Figures 5 and 6. Figure 5 shows the silanol-silanol condensation reaction generating the siloxane and a water byproduct, and Figure 6 shows a mechanism for a silanol-alkoxysilane condensation reaction generating a crosslinked siloxane structure and an alcohol byproduct. In practice, hydrolysis and condensation occur concurrently unless special efforts are made to separate the steps.1
VIEW FIGURE 7

Figure 7: The effect of pH on the organosilane hydrolysis and condensation reaction rates.
Catalysis of Organosilane Crosslinking2
The hydrolysis and condensation reaction rates of organosilane systems are dependent on pH of the system and on the substituents on the silicon. The rate minimum for the hydrolysis and condensation reactions occurs at approximately pH 7 and pH 4, respectively. Each pH change of one unit in either direction produces a ten-fold rate acceleration assuming an excess of water is available. At pH > 10, hydrolysis of the first intermediate, RSi(OR)2OH, is inhibited due to the ionization of the silanol group.3 The effect of pH on the organosilane hydrolysis and condensation reaction rates is illustrated in Figure 7. Both hydrolysis and condensation reactions are reversible. Alcohols will reverse the silane hydrolysis.
VIEW FIGURE 8

Figure 8: Base catalyzed hydrolysis of alkoxysilanes.
Osterholtz and Pohl described specific mechanisms for each of the acid and base catalyzed reactions. Torry, Campbell, Cunliffe and Tod studied activity of organometallic compounds in organosilane systems and propose tin compounds as the most active. Tin catalysts must initially hydrolyze to form the active species.4 Dioctyltin and dibutyltin compounds that catalyze many of these crosslinking reactions include dioctyltin diacetylacetonate and dibutyltin dilaurate. However, concerns about toxicity of tin compounds have driven formulators to explore other catalyst options. Finding a non-tin catalyst that could provide sufficient reaction acceleration for all silane crosslinking chemistries is difficult. Some acids might provide good acceleration of the crosslinking reaction, but the acid might also accelerate rearrangement of the formed polysiloxane backbone, causing product degradation. Some tertiary amines could accelerate the crosslinking reaction, but they might also contribute color and odor.
Base Catalyzed Hydrolysis of Alkoxysilanes
Osterholtz and Pohl proposed a bimolecular nucleophilic displacement reaction depicted in Figure 8 for base catalysis of alkoxysilane hydrolysis, involving a pentacoordinate intermediate, and two different transition states. In the presence of a base and water, the transition state T.S.1 is formed with a partial negative charge on the alkoxysilane silicon. T.S.1 then dissociates to generate the pentacoordinate intermediate, which subsequently breaks down to the desired silanol through a second transition state. Negative charge development on the silicon in the transition state (T.S.1 or T.S.2) is considerable. This is supported by experimental observations where electron-withdrawing substitution on the alkyl groups attached to the Si accelerates the rates of hydrolysis. This is due to the stabilization of the developing negative charge, which lowers the energy of the transition states.
In General Base Catalysis of the hydrolysis of alkoxysilanes, any basic species accelerates the reaction by assisting the removal of a proton from water in the transition state. In Specific Base Catalysis of the hydrolysis of alkoxysilanes, the hydroxide anion accelerates the reaction rate by directly attacking the substrate.
VIEW FIGURE 11
VIEW FIGURE 10
VIEW FIGURE 9

Figure 11: Acid catalyzed condensation of silanols.

Figure 10. Acid catalyzed hydrolysis of alkoxysilanes.

Figure 9: Base catalyzed condensation of silanols.
Base Catalyzed Condensation of Silanols
Chojnowoski and Chrzczonowicz found that secondary and tertiary amines (piperidine, triethyl- amine, tri-n-butylamine) catalyzed the condensation of a series of dialkyl- or diarylsilanediols in aqueous dioxane.5 They proposed that primary and secondary amines catalyzed the reactions by nucleophilic attack on silicon, which was followed by the rapid attack of dialkylsilanediol on the formed silamine, as shown below in Figure 9.
Acid Catalyzed Hydrolysis of Alkoxysilanes
The mechanism for acid catalyzed hydrolysis (Figure 10) is a rapid equilibrium protonation of the substrate, followed by a bimolecular SN2-type displacement of the leaving group by water.
Acid Catalyzed Condensation of Silanols
The acid catalyzed condensation reaction proceeds by an initial protonation of the silanol followed by an SN2 displacement reaction at the Si, leading to formation of water and regeneration of the acid catalyst (Figure 11).
VIEW FIGURE 15
VIEW FIGURE 14
VIEW FIGURE 13
VIEW FIGURE 12
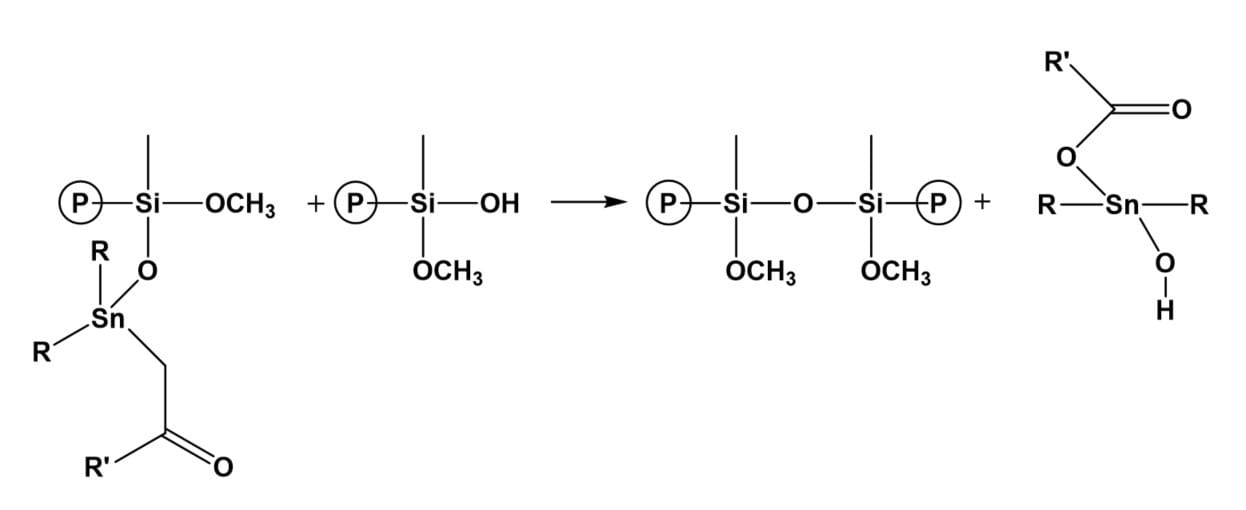
Figure 15: Formation of siloxane groups.

Figure 14: Formation of silanol groups.

Figure 13. Formation of organotin silanolates.
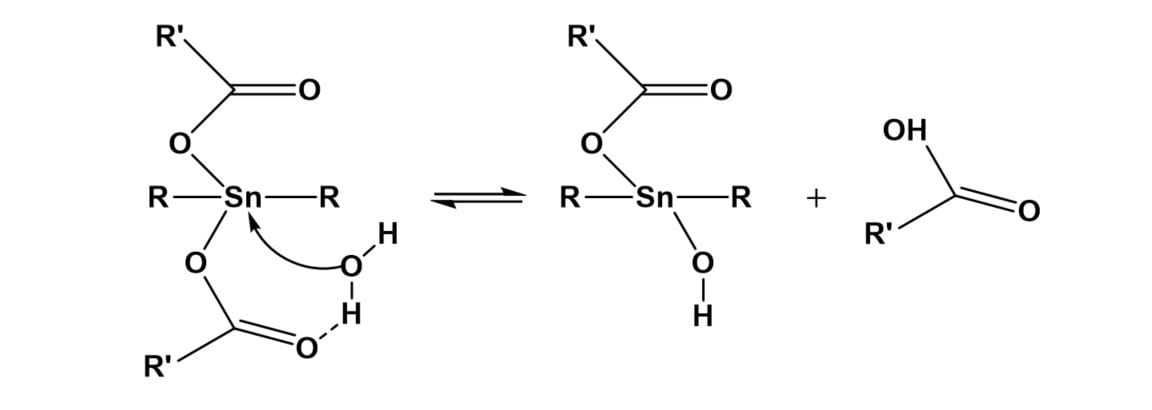
Figure 12. Hydrolysis of tin catalysts.
Tin Catalysis Mechanism
Tin catalyst can be in the form of dioctyltin and dibutyltin diacetylacetonate and dibutyltin dilaurate (DBTDL). Catalysis of organosilanes with tin compounds begins with hydrolysis of the tin compound. The tin compound undergoes hydrolysis and forms an organotin hydroxide (Figure 12), which is the true catalytic species.6 The organotin hydroxide reacts with an alkoxysilane group to form an organotin silanolate (Figure 13). The tin silanolate will react readily with alcohols and water to form the silanol (Figure 14). The organosilanolate will also react with formed silanol groups to produce siloxane linkages, and the organotin hydroxide catalyst is regenerated (Figure 15).
Activity of the tin catalysts can be dependent on the pH of the system. For example, additional acid can affect the hydrolysis mechanism in Figure 12 by forcing the equilibrium to the left and preventing the formation of the active tin hydroxide. Also, strongly acidic species may interact with already formed basic tin hydroxide to prevent further reaction with alkoxysilane groups.
Tin Regulations
There has been increased examination of human health risks and environmental issues associated with tin compounds since restrictions for anti-fouling paints for marine markets began in the early 1980s. In 1999, the International Maritime Organization adopted a global resolution prohibiting the use of organotin compounds acting as biocides in anti-fouling systems by January 1, 2008.7 Organotin compounds are currently regulated by The International Maritime Organization’s Antifouling System (IMO AFS) convention and the U. S. Organotin Antifouling Paint Control Act (OAPCA). The European Commission Decision 2009/425/EC claims organostannic compounds in consumer products pose a risk to human health, increasing the scope of restrictions beyond maritime markets. 2009/425/EC, which includes restrictions on the use of dibutyltin, dioctyltin, and tri-substituted organotin compounds, was incorporated into ANNEX XVII of REACH through regulation (EU) 276/2010.8
EU regulations restrict tin to ≤ 0.1% metal, with global restrictions likely becoming more restrictive. Many formulators of oganosilane systems are proactively striving to develop tin-free systems. The dosage of tin metal that is often required to achieve sufficient cure of moisture cured organosilane polymer systems is typically very close to the REACH ≤ 0.1% limit, with the possible exception of trimethoxysilane polymers that usually require less catalyst.
Catalyst Options
As described in the catalysis section, the organosilane reactions can be catalyzed with acids, bases, and metal compounds. Organotin compounds are very effective catalysts, and they are commonly used in these systems. The motivation for replacing tin catalysts can be for performance issues, but often the motivation is to address regulatory issues. Extensive studies were conducted to identify compounds that could be considered alternatives to tin catalysts in organosilane systems. Amine-type compounds like guanidines can act as catalysts for some organosilane polymers, but even if they sufficiently catalyze the reaction, they are skin sensitizers and can contribute other undesirable characteristics like odor or color.
The control systems in each of the following experiments were catalyzed with a tin catalyst. The non-tin catalyst highlighted in these experiments are CATALYST9 670 (zinc/amine compound) and CATALYST 648, a modified version of CATALYST 670. Compared to tin compounds, zinc compounds do not carry the environmental and biological restrictions of tin compounds. Extensive utilization of zinc compounds in the field of medicine exemplifies their non-toxic nature.
Experiment I is based on a dimethoxymethylsilyl (DMS) polyether polymer and Experiment II is based on a trimethoxymethylsilyl (TMS) polymer. Experiment III addresses the issue of methanol generation by using an organosilane based on a diethoxysilyl (DES) polyether polymer.
VIEW table 1

Table 1: Degree of dryness (DIN 53 150).
Experimental
Fully formulated single-component moisture-cure alkoxysilane systems were used in the following experiments. The uncatalyzed one-component formulations were stored in dispense cartridges. Approximately 30 grams of uncatalyzed material was dispensed into a container with a caulk gun before addition of the catalyst. The material was mixed on a speed mixer. An adjustable doctor blade was used to apply approximately 3 mm of the blends onto a paper substrate. The degree of dryness was determined by using a Model 415 Drying Time Tester.10 The dryness test involved applying a force onto a paper disk that covered a test site on the casting for 60 seconds. The results are based on the amount of tack and on visual impressions that developed from the applied force. The dryness testing was done at 25 °C and 50% relative humidity. Degree 1 of the DIN 53 150 method was substituted with a glove test to determine touch dry. Table 1 defines the rating system.
VIEW table 4
VIEW Table 3
VIEW table 2

Table 4: Experiment I, Mechanical properties. Cure: 2 weeks ambient

Table 3: Experiment I, Degree of dryness (hours).

Table 2: Experiment I, DMS system formulation.
Where tested, hardness of the castings was determined with a Shore A11 hardness tester after the castings were allowed to cure under ambient conditions for 2 weeks. Other mechanical properties were measured on an Instron12 tester using dogbone shaped samples cut from 3 mm thick castings.
Experiment I. Moisture-cure system based on dimethoxymethylsilane (DMS) polymer13
The control system in this experiment was catalyzed with dioctyltin diacetylacetonate (DOTDAA) in a system based on a polyether backbone DMS polymer. The dosage of tin catalyst in the control system was 0.6% DOTDAA. The tin content of DOTDAA is approximately 21%. At 0.6%, the tin content in the formulated control system is approximately 0.12%, which would not comply with EU regulations. The formulation is in Table 2.
Dryness ratings are in Table 3. The DOTDAA and CATALYST 670 catalyzed systems achieved the highest degree of dryness in 6 hours. Mechanical properties were not significantly different (Table 4). The DOTDAA and CATALYST 670 castings developed similar tensile stress (toughness), modulus (stiffness) and strain (elongation).
Tested guanidine compounds were not effective catalysts except for high dosages of 1-phenylguanidine. The high dosage, however, caused severe surface and appearance defects in the cured product.
VIEW table 7
VIEW Table 6
VIEW table 5

Table 7: Experiment II, Mechanical properties. Cure: 2 weeks ambient.

Table 6: Experiment II, Degree of dryness (hours).

Table 5: Experiment II, DES system formulation17.
Experiment II. Moisture-cure system based on diethoxysilane (DES) polymer16
The basic uncatalyzed DES formulation is in Table 5. DOTDAA was essentially not active in this system. At 0.5% and 1.0% on total formulation weight, DOTDAA catalyzed castings required more than 120 hours to achieve a dryness rating of 7 (Table 6). Dry times with CATALYST 670 were significantly faster than the tin catalyzed systems. The CATALYST 670 system developed dry times that were comparable to the DMS system.
The DOTDAA system required a month of ambient cure before it was suitable for mechanical testing. Even so, the casting had very weak properties (Table 7).
Diethoxysilanes are of particular interest from a toxicity perspective, as the volatile byproduct of the crosslinking reaction is ethanol instead of toxic methanol.
VIEW table 10
VIEW graph 1
VIEW table 9
VIEW table 8

Table 10. Experiment III, Mechanical properties. Cure: 2 weeks ambient.

Graph 1.

Table 9. Experiment III, Degree of dryness (hours).
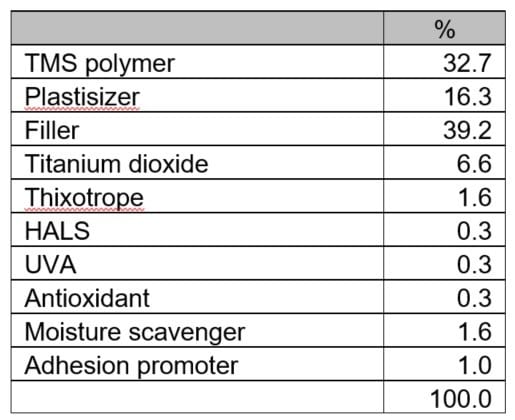
Table 8: Experiment III, TMS system formulation.
Experiment III. Moisture-cure system based on trimethoxysilane (TMS) polymer
Typical tin catalyst dosages in trimethoxysilane polymer systems are less than in dimethoxysilane polymer systems. The control system in this experiment was catalyzed with 0.06% DBTDL. Although the CATALYST 670 and 648 dosages in this experiment were still higher than the tin catalyst dosage, sufficient cure was achieved when their dosages were reduced by half. CATALYST 670 can work synergistically with additional silane adhesion promoters like 3-aminopropyltriethoxysilane.
The mechanical properties in Table 10 show similar hardness development for each system. However, the DBTDL system had lower % strain (elongation) than each of the non-tin systems.
Conclusion
Increasing regulatory restrictions have formulators of organosilane adhesives and sealants searching for alternatives to tin catalysts. CATALYST 670 and CATALYST 648 were effective non-tin catalysts in three one-component organosilane experiments that required acceleration of both the hydrolysis and condensation reactions.
Also addressed in this work was the catalysis of a non-methanol-emitting moisture-cure organosilane system based on a diethoxysilane polymer. In this case, CATALYST 670 catalyzed the crosslinking reaction while tin catalysts were essentially not active even at levels that doubled the maximum tin concentrations allowable in current EU regulations.
Acknowledgements
The authors would like to thank Dr. Ravi Ravichandran, David Switala, and Matthew Gadman for contributions made to this article.
Learn more about King Industries at www.kingindustries.com.
References:
1 Osterholtz, F. D.; Pohl, E. R. Kinetics of the hydrolysis and condensation of organofunctional alkoxysilanes: a review, J. Adhesion Sci. Technol. Vol. 6 No. 1, pp. 127-149 (1992)
2 Florio, J.; Ravichandran, R. Non-Tin Catalysts for Crosslinkable Silane Terminated Polymers. Coatings Tech Magazine, pp. 46-57 (2016)
3 Osterholtz, F. D.; Pohl, E. R. Kinetics of the hydrolysis and condensation of organofunctional alkoxysilanes: a review, J. Adhesion Sci. Technol. Vol. 6 No. 1, pp. 127-149 (1992)
4 Torry, S.A.; Campbell, A.; Cunliffe, A.V.; Tod, D.A. Kinetic analysis of organosilane hydrolysis and condensation. International Journal of Adhesion & Adhesives, 26 (2006) 40-49
5 J. Chojnowski and S. Chrzczonowicz, Bull. Pol. Acad. Sci. 13, 41 (1965)
6 Frederik Willem, Makromol. Chem. 181, 2541-2548 (1980)
7 International Maritime Organization, https://www.imo.org/en/OurWork/Environment/Pages/Anti-fouling.aspx
8 Commission Regulation (EU) No 276/2010 of 31 March 2010 http://eur-lex.europa.eu/LexUriServ/LexUriServ.do?uri=OJ:L:2010:086:0007:0012:EN:PDF
9 K-KAT non-tin metal catalyst, King Industries, Inc.
10 Model 415 Drying Time Tester, Erichsen GmbH & Co. KG
11 Shore A durometer, Instron Corporation
12 Dual column table top model, 30 kN (6700 lbf) load capacity, Instron Corporation
13 Florio, J.; Ravichandran, R. Non-Tin Catalysts for Crosslinkable Silane Terminated Polymers. Coatings Tech Magazine, pp. 46-57 (2016)
14 MS PolymerTM S303H dimethoxymethylsilane polymer , Kaneka Corporation, Osaka, JP
15 DISPARLON 6250 rheology modifier, Kusumoto Chemicals, Ltd.
16 Florio, J., Ravichandran, R., Non-Tin Catalysts for Crosslinkable Silane Terminated Polymers. Coatings Tech Magazine, pp. 46-57 (2016)
17 Florio, J.; Ravichandran, R. Non-Tin Catalysts for Crosslinkable Silane Terminated Polymers. Coatings Tech Magazine, pp. 46-57 (2016)
18 Diethoxysilane polymer, Easterly Research, Warminster, PA
Open image courtesy of ClaudioVentrella / iStock / Getty Images Plus via Getty Images.