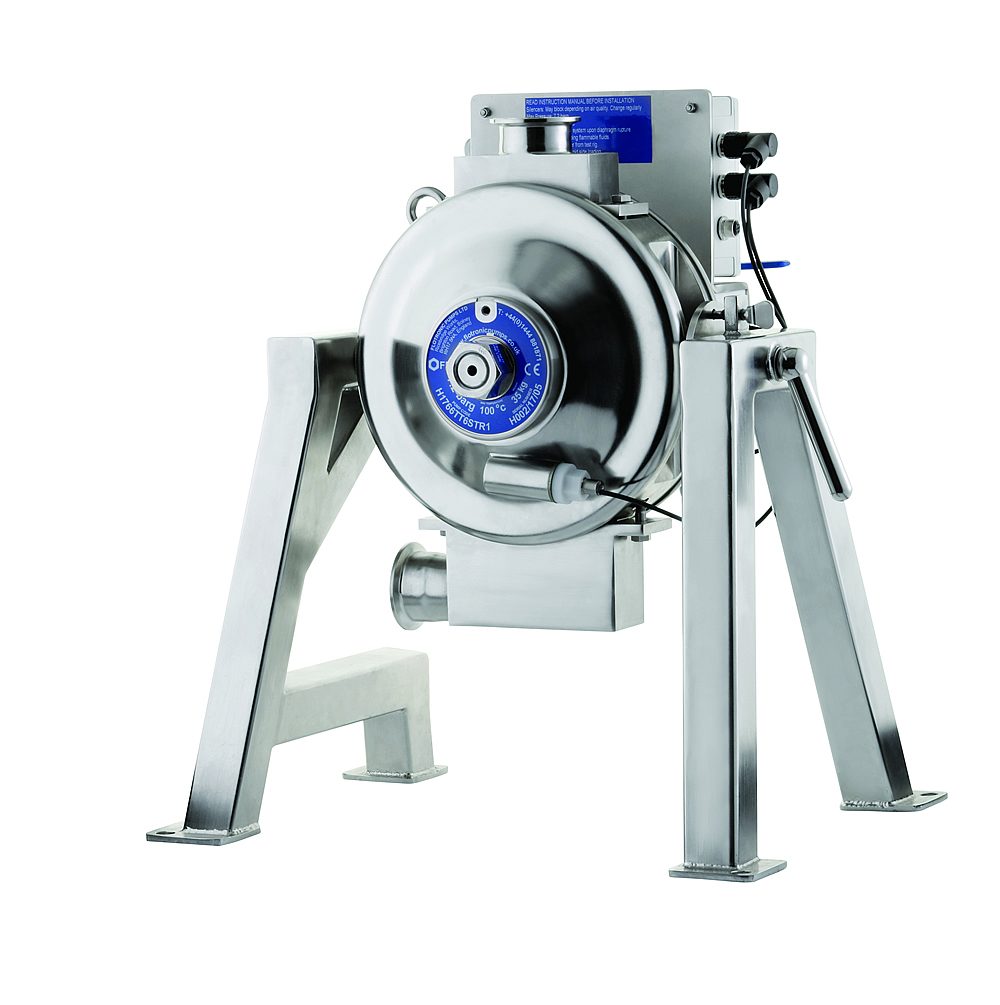
Pumps and valves enable processors to greatly increase efficiency
PROCESSING TECHNOLOGIES
The Unibloc Flotronic Slimline AODD+ pump can be disassembled quickly for maintenance after removing just one large nut. Courtesy of Unibloc.
As input and labor costs remain high, dairy processors are looking to optimize production efficiency and cut costs. Pumps and valves, though a seemingly small aspect of dairy production, enable processors to achieve these goals.
To reach these objectives, processors must stay in the loop on evolving trends and key concerns for pumps and valves in dairy processing.
John McGinn, co-owner and founder of Kenosha, Wis.-based pump manufacturer McFinn Technologies, noted that current trends for dairy pump development reflect the pressures processors are facing, as well as consumer taste preferences. “Efficiency, product yield, product taste are key drivers for the equipment being purchased,” McGinn says. “Pumps and valves that are efficient, gentle to the product and easily cleaned will continue to grow in demand.”
By Sammy Bredar, Associate Group Editor
As input and labor costs remain high, dairy processors look to optimize production efficiency and cut costs.
Pumps and valves enable processors to greatly increase efficiency
Sanitation is a key concern when selecting both pumps and valves at the dairy plant. Sanitary standards like 3A, EHEDG and FDA compliance are driving design development, notes Sumeer Banger, sales application engineer, Food, Petfood & Ag grain for Coperion, (formerly Schenck Process Food & Performance Materials), a company that designs, manufactures and services technologies for bulk material handling.
Banger notes that processors should prioritize crevice-free surfaces to eliminate bacterial buildup, as well as corrosion resistance when deciding on construction material. Additionally, processors should prevent cross contamination while controlling moisture and condensation.
Callee Danielson, sales engineer for Kennesaw, Ga.-based Unibloc Hygienic Technologies, recommends utilizing pumps that are clean-in-place (CIP) capable and fully drainable. Unibloc manufactures industrial equipment, including pumps, valves, strainers and other flow control products. By utilizing systems that are both CIP-capable and drainable, processors can avoid timely system disassembly and manual cleaning.
ZRD Hygienic Valve
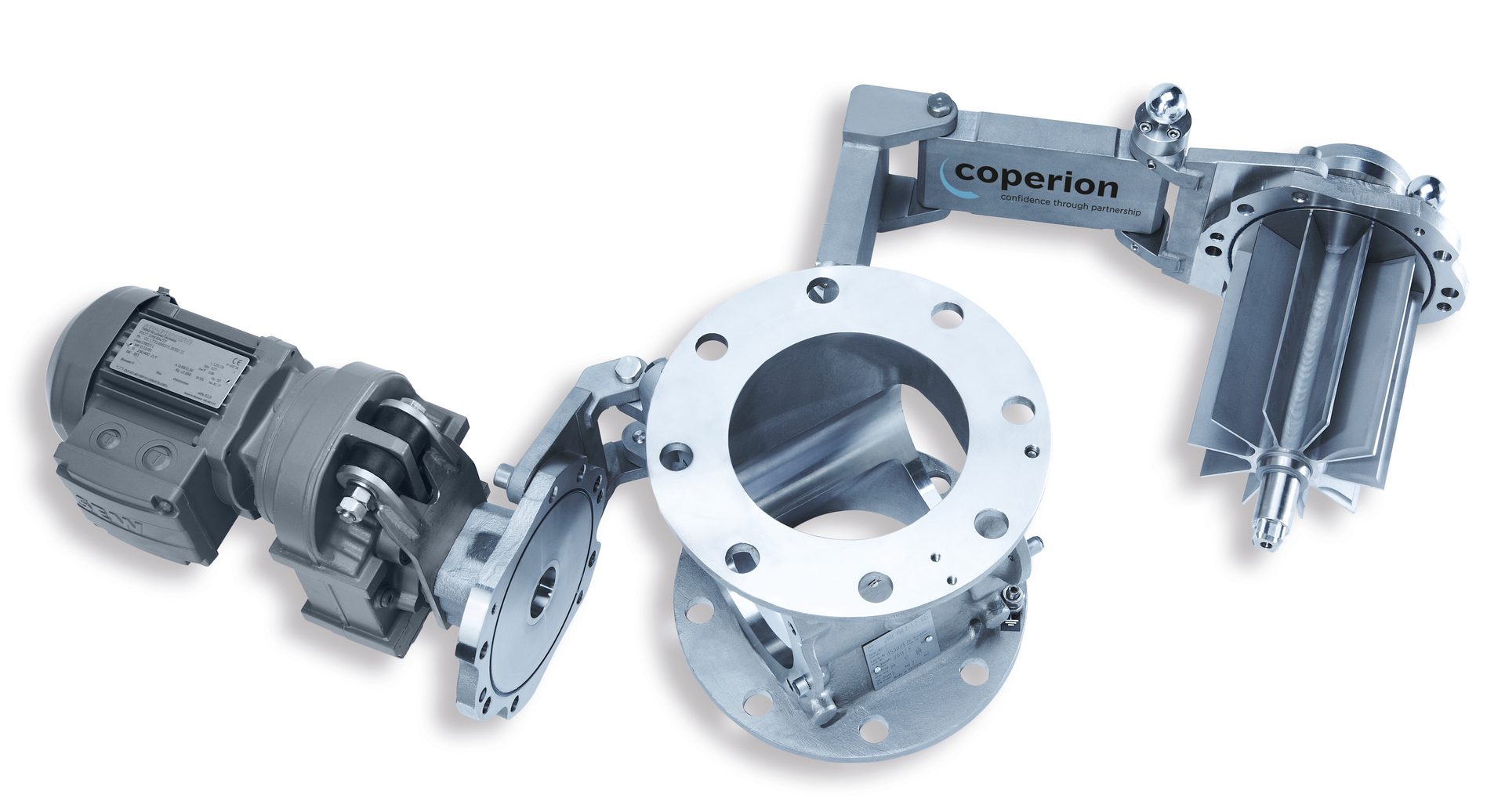
Global Hygienic Blow-Through Airlock
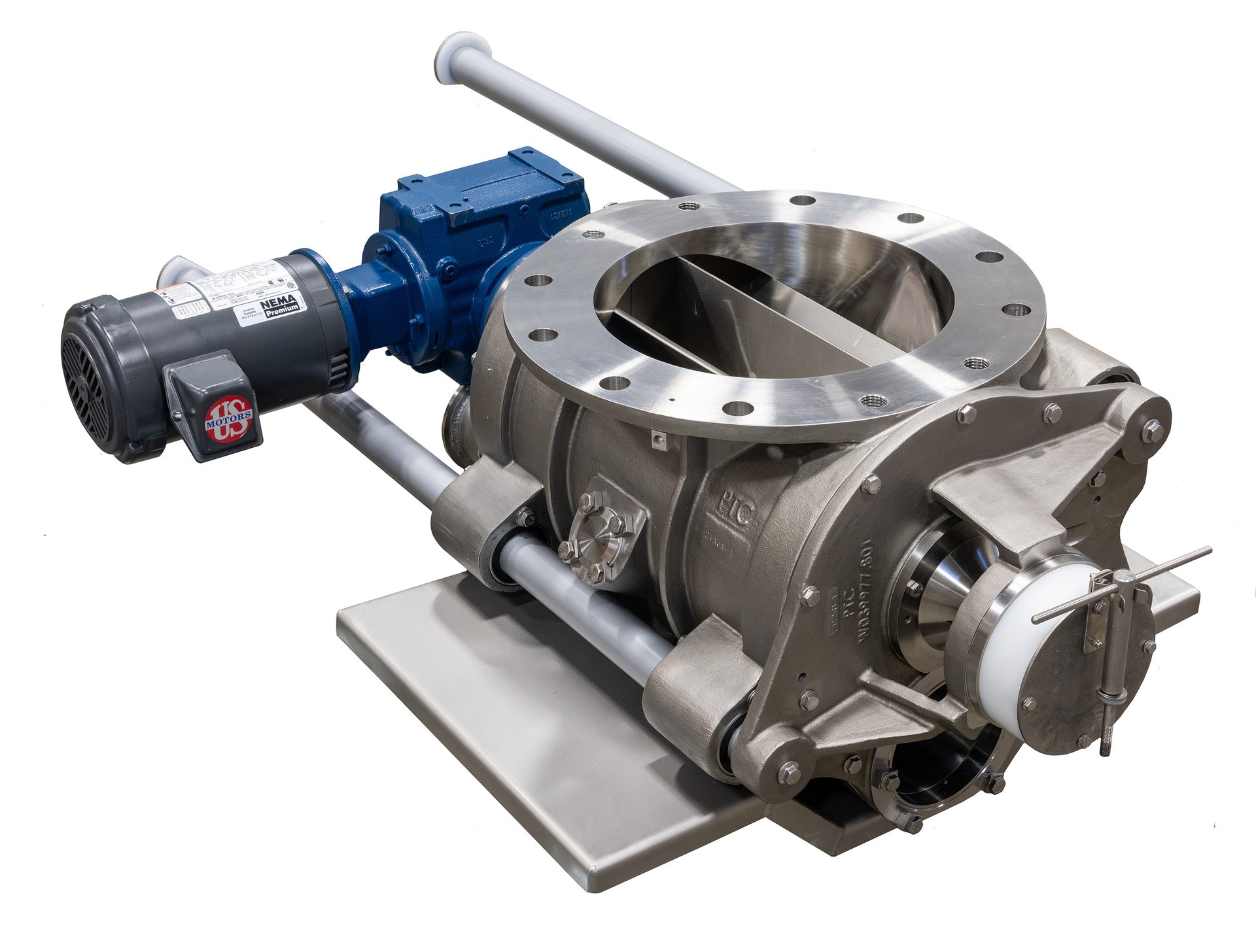
Global Hygienic Airlock
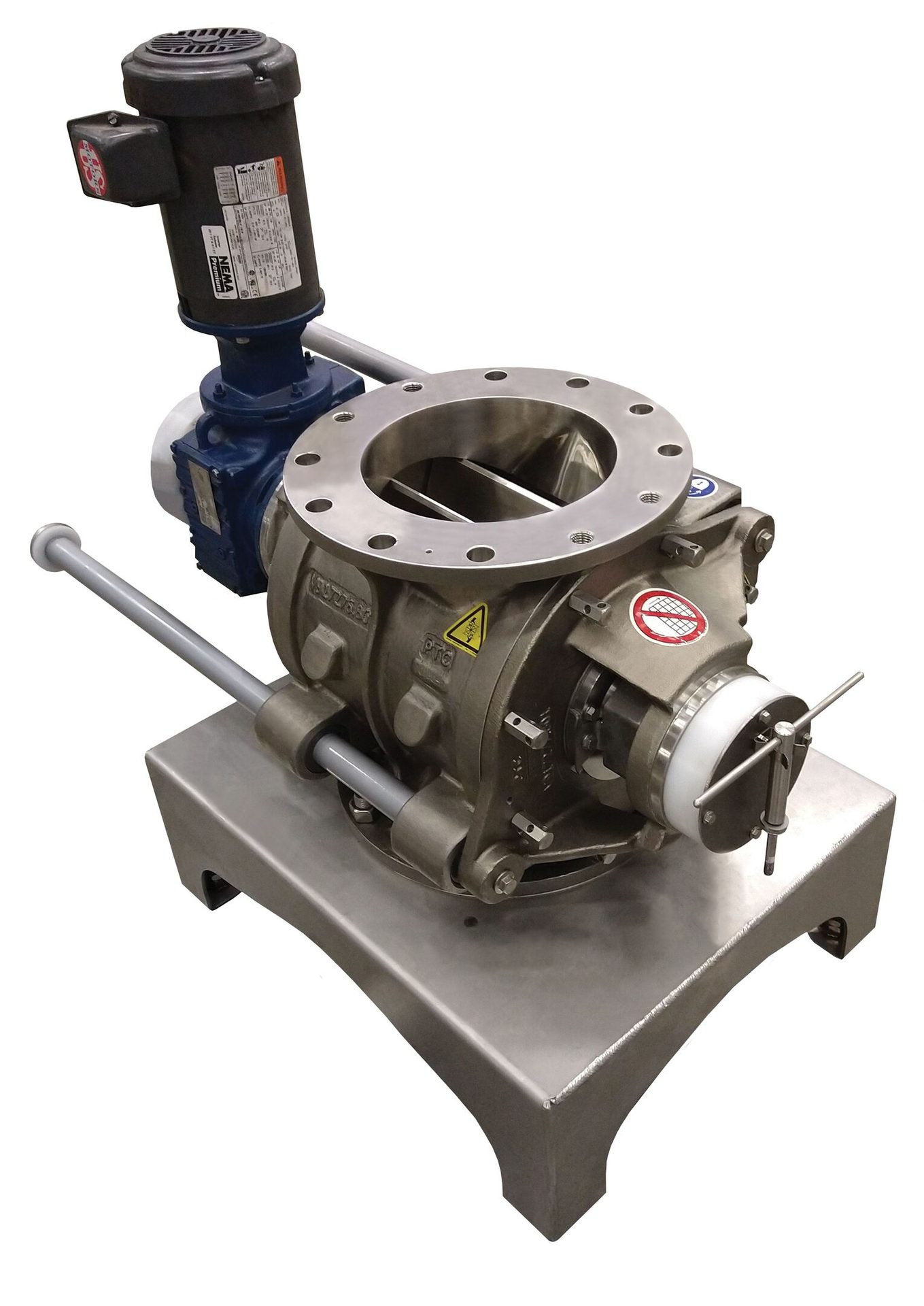
Images courtesy of Coperion
Service requirements
Danielson states that efficiency can be greatly impacted by how a pump can be serviced. “Some pumps are designed with fewer parts to enable fast disassembly for maintenance, freeing up crews for other tasks,” Danielson says. “In addition, to limit the number of spare parts and training needed, operators should standardize on a few preferred pump vendors.”
Processors can further optimize efficiency by cleaning their systems thoroughly and regularly, avoiding air and product leaks, Banger relays.
Choosing the right cleaning solution is essential to optimizing operational efficiency. McGinn notes that velocity of the cleaning solution is the key to success. “Many pumps are fine for pumping the dairy product at lower velocities through the pipe work, but they are unable to provide the high velocity flows of CIP cleaning solution that are required to provide proper cleaning,” McGinn states. “Many pumps cavitate during CIP, causing both seal failure and inadequate cleaning.”
Model B15154 – (1.5”, 2 or 3 HP) Bowpeller
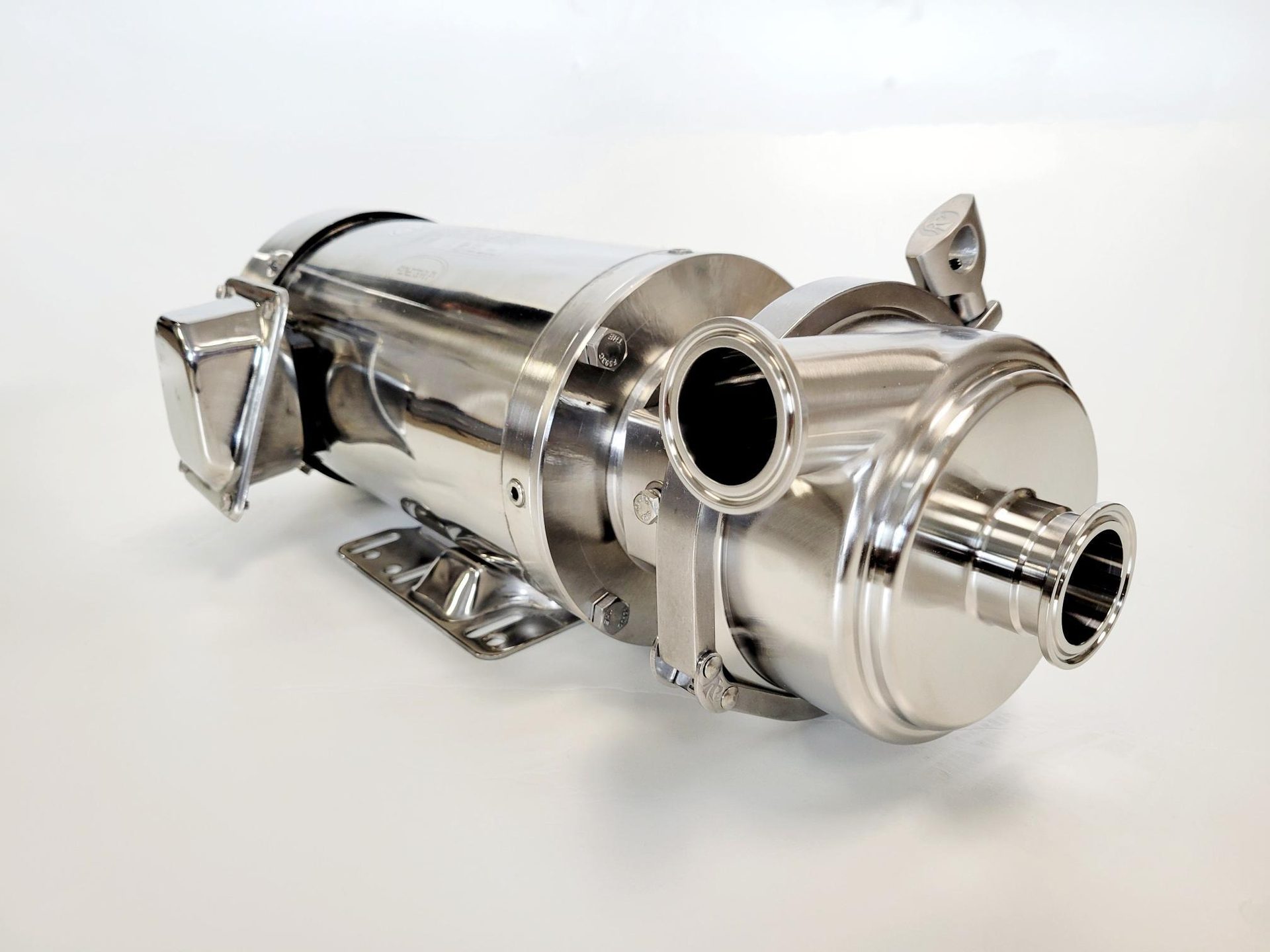
Model B3258 - 8” (5 - 15 HP) Bowpeller
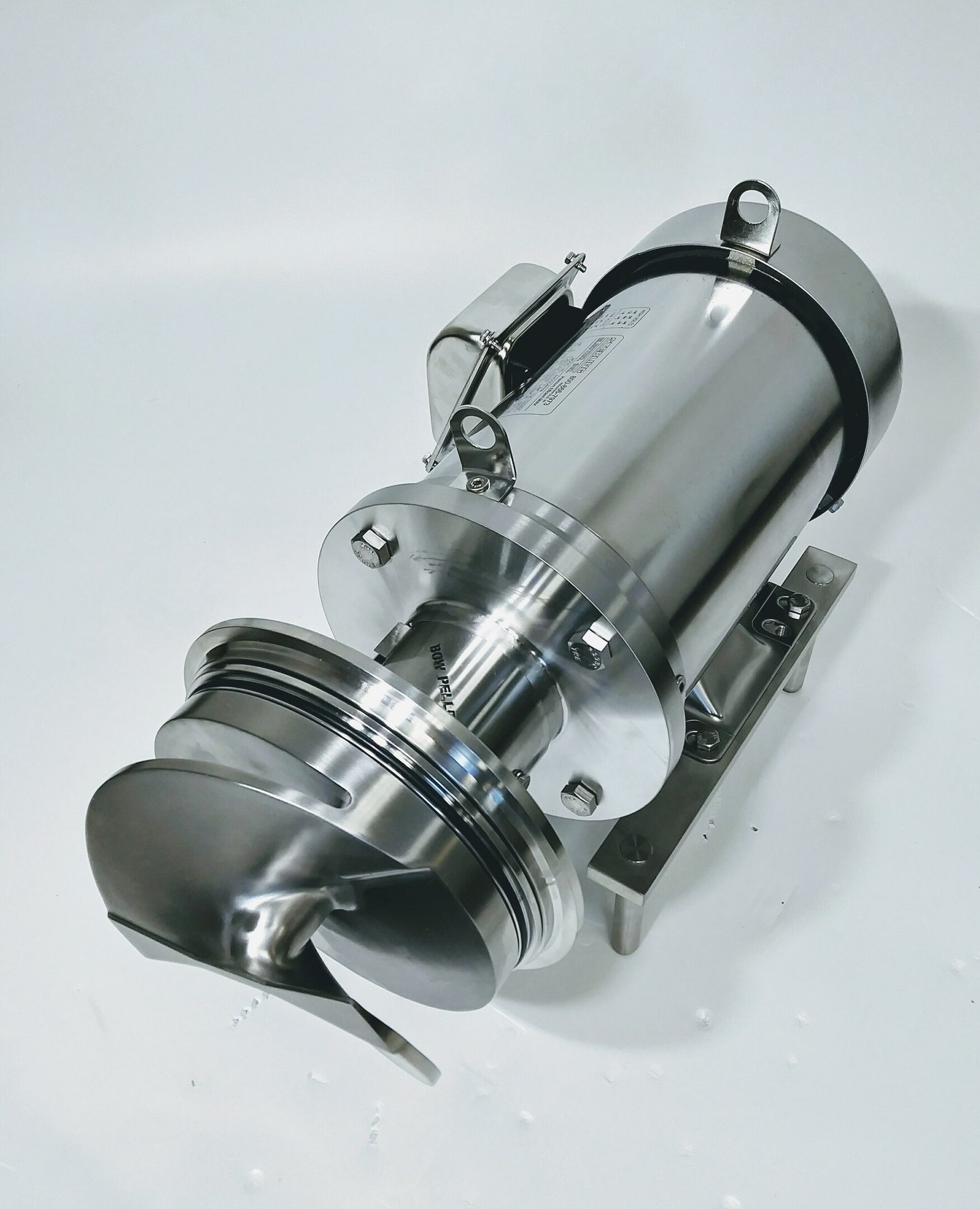
Model B2526 – 6” (3, 5, 10 or 15 HP) Bowpeller
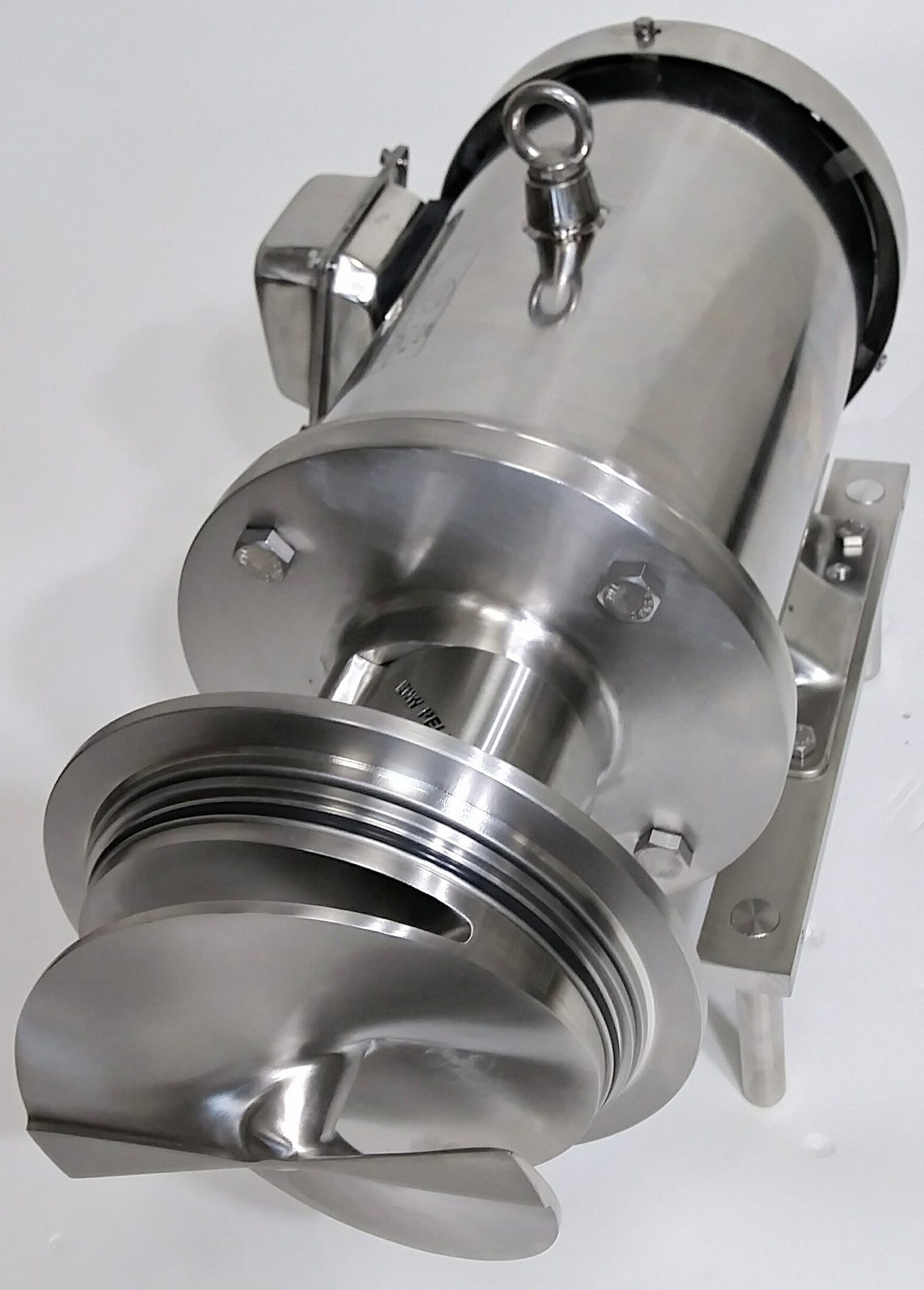
Images courtesy of Katie Patterson, McFinn Technologies
Energy efficiency
Efficiency is a key trend driving modern pump and valve development for dairy processors. In particular, low-energy pumps help producers reduce their energy consumption without compromising on flow rate, Banger reveals. Processors are also utilizing variable frequency drives to control motor speed, therefore optimizing their energy usage.
By improving on energy usage, producers can capitalize on another evolving trend: sustainable production. Sustainability is impacting every segment of the food and beverage industry. Banger notes that VFDs, high-efficiency motors and optimized airlock designs all promote sustainable operations, cutting down on electricity consumption and reducing a processing plant’s carbon footprint.
Optimized energy efficiency is a great way to cut costs. To minimize expenses, processors are increasingly examining the total cost of ownership. Though an initial investment could be expensive, processors are willing to make that initial purchase to offset high costs down the line.
“The initial cost of a pump is only part of the equation,” concludes Danielsson. “Pump manufacturers are prioritizing designs that offer ease of maintenance and durability. More durable products will not need to be replaced as regularly, while ease of maintenance can streamline labor and even minimize labor costs.” DF