Food Safety - Part 2
Getting Pressure to Remove the Heat?
High-pressure processing—or cold pasteurization—can be a significant investment, but if your product is perceived as organic, high-end, minimally processed and nutritional, it may well be worth the investment.
Packaging Requirements for HPP
Materials commonly used for HPP packaging are flexible films, pouches, skin pack, trays, bottles and cups with at least 15% compressibility as products will compress at least 15% of their volume at 6,000 bars, says Quintus’s Williams. Packages need to be hermetically sealed to prevent leakage. Sealing surfaces for top films on trays and cups need to be relatively wide, uniform and preferably flat.
For plastic bottles without an induction safety seal on the lips, specially designed caps/closures are needed to prevent leakage, adds JBTAvure’s Raghubeer. PET and materials with high oxygen (low OTR) and good moisture vapor barrier (MVTR) properties are commonly used for HPP applications to optimize microbial shelf life and reduce oxidative reactions. Care should be taken when thermoforming materials with oxygen barrier (EVOH) layers as overstretching of the material can compromise the EVOH layer, particularly in corners.
Packages must be able to withstand pressure transmitted during HPP. Most plastics and laminated films have enough elasticity, but packages should always be tested, says Zapata.
Hiperbaric has an HPP USA packaging supplier list, which outlines compatible HPP packaging options. Complimentary packaging testing is also offered at its HPP pilot plant facility.
A pair of Quintus Technologies high-pressure processing (HPP) QIF 400L-6100 systems will begin operation in Yiqing Food’s new beverage facility in Danjiangkou, Hubei province, China by year’s end. The machines feature VFD motor drives, SmartPress cloud-based management software, fewer moving parts and easy access to all components requiring regular maintenance or inspection. Image courtesy of Quintus Technologies
by Wayne Labs, Senior Contributing Technical Editor
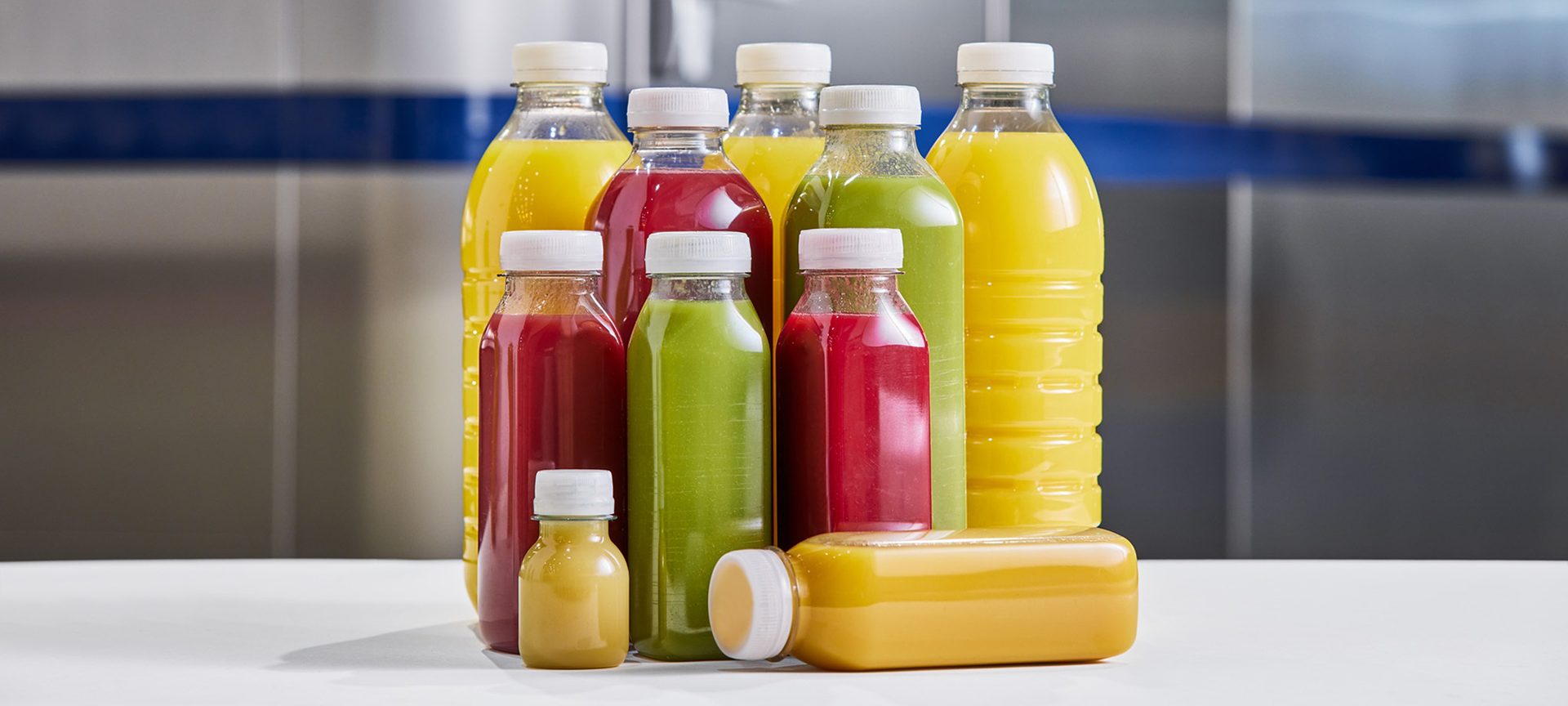
Pre-packaged bottled juices and RTE meals are two candidates for HPP, provided they meet the sealing requirements specified by the HPP manufacturer. Images courtesy of Quintus Technologies
Bulk Liquid Processing
HPP is a batch process. There are costs associated with the startup and shutdown of any batch process, so running fewer, larger batches reduces those costs, says CRB’s Moses. It can also improve throughput time.
Hiperbaric attacked this issue a few years ago (see FE’s Engineering R&D, FEB 2020) with the introduction of a bulk liquid processing machine that could handle up to 10,000 liters/hour when processing liquid in bulk and equipped with two processing chambers of 525-liter volume. Two machines are available—the Model 525 Bulk that handles 525 liters in a single batch or the Model 1050, which handles 1050 liters in a single batch. “The process begins by liquids filling the inlet tank,” says Zapata. “After pressurization, the HPP beverage fills the outlet tank through sterilized tubes and is ready to be bottled in an ultra-clean filling line.”
“Bulk processing of pumpable product will increase product throughput with better usage of the space in an HPP carrier,” says Raghubeer. “This post-HPP fill system, such as JBTAvure’s FlexiBulk system, will give more options in the final packages used, particularly with the environmental constraints of plastic materials. However, these benefits do come with some added cost and restrictions as ultra-clean filling or aseptic filling systems are required.”
“We are looking into more environmentally friendly consumer bulk packages; compressible materials such as plant-based ‘plastic’ materials do not provide the necessary oxygen barrier properties to get the benefits of shelf-life extension afforded by HPP technology,” says Quintus’s Williams. “Bulk systems increase product throughput, which reduces energy cost since a larger volume of products are processed per cycle. This allows for more environmentally friendly packaging options such as glass and paper.”
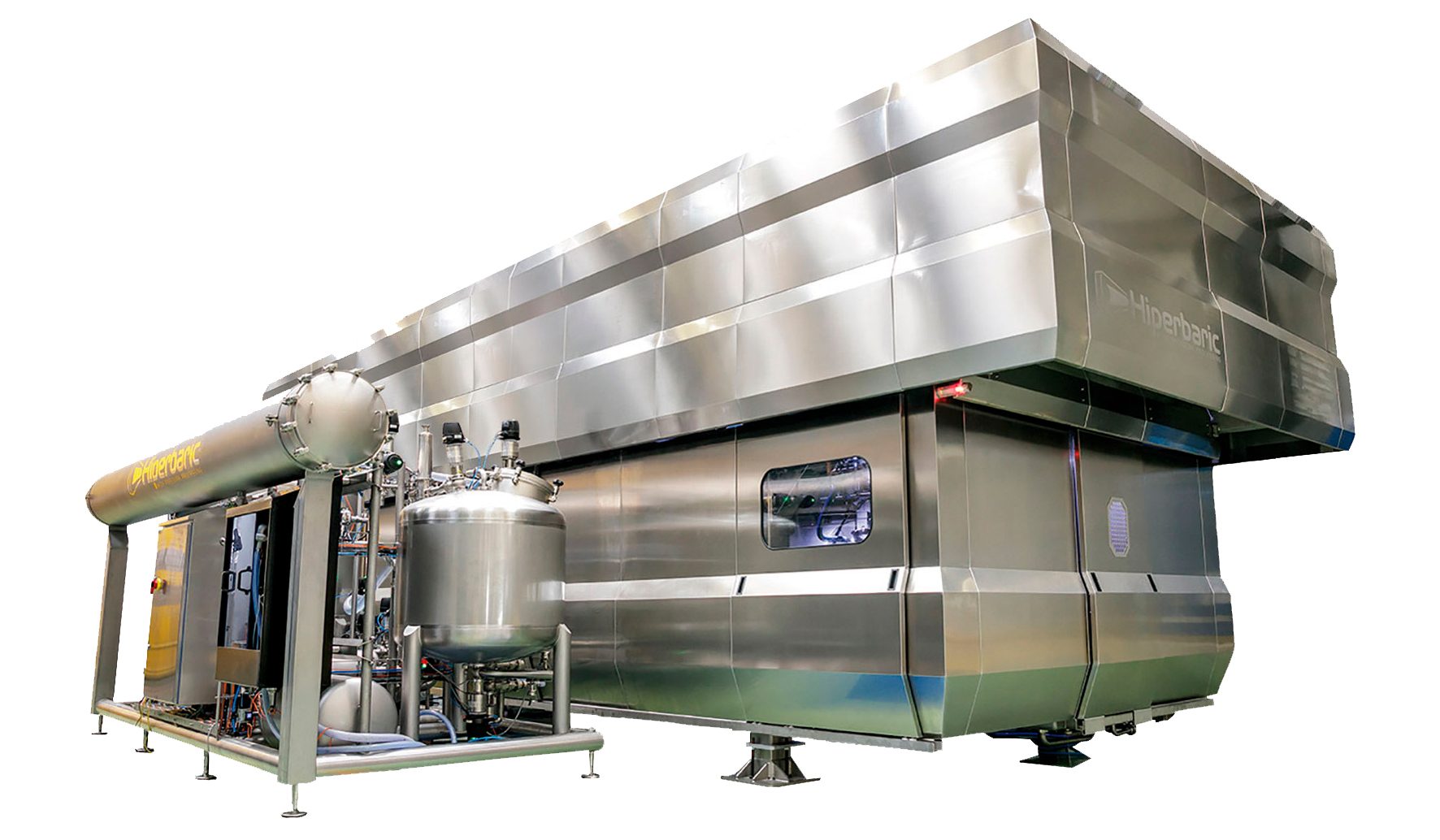
For handling bulk liquids before packaging, Hiperbaric’s In-Bulk processor allows a 90% filling efficiency, reaching a maximum capacity of 1,300 gallons per hour. Image courtesy of Hiperbaric
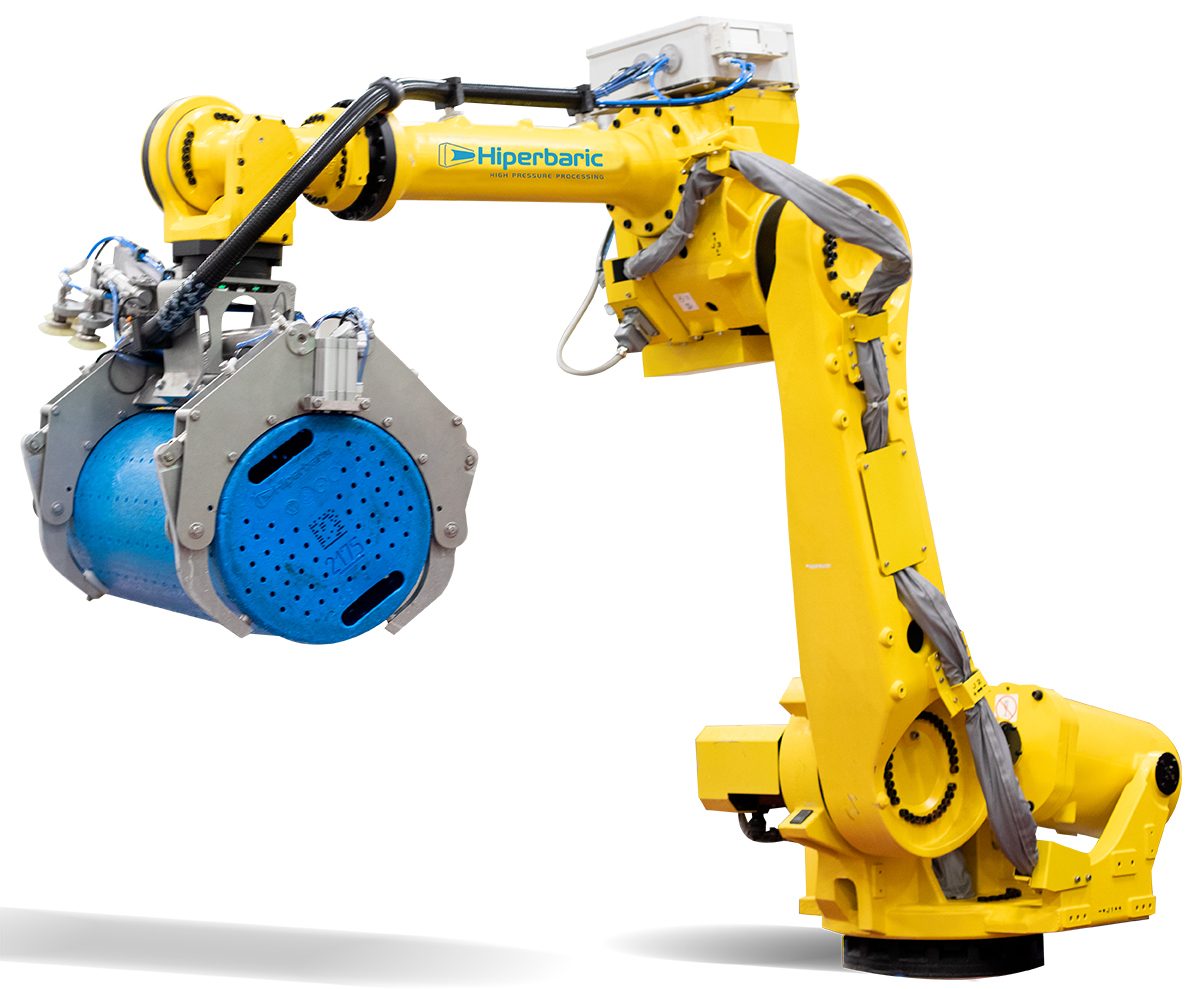
Hiperbaric’s automation system includes a robot arm for loading and unloading of baskets. In addition to this, robots are also available for material handling after unloading of baskets. Image courtesy of Hiperbaric
Automating Material Handling?
Whether or not you decide to integrate automated material handling to, from and for loading/unloading an HPP system will depend on product flow and weight plus throughput. Obviously, the more you can keep the HPP operating, the lower the cost to your final product if you own the HPP equipment.
“HPP systems are typically fed via a conveyor system that may have automation,” says CRB’s Jerry Steenhoek, senior director of automation technology. “The takeaway system is typically some type of conveyor or packaging line. There may be some automation on these systems. Most HPP systems have a basket system that needs to be loaded prior to processing and unloaded after the processing. If the product(s) you are running through the HPP process are consistent, you perhaps could utilize robots in this capacity. The HPP systems I have seen, the baskets tend to be cylindrical, which could be an issue for robots.”
“We are investigating fully and semi-automatic loading and unloading systems,” says Quintus’s Williams. “Currently there are limited options particularly with the geometrical issues of dealing with a round cylinder basket.”
With the help of system integrators, Hiperbaric has been able to integrate robots with specially designed grippers to handle the cylindrical product baskets. The robots can aid in the loading/unloading of the baskets with product and placing them on the loading belt going into the HPP machine. Material handling is simplified with RFIDs and data matrix codes placed on the HPP baskets to track inventory, automate setup and provide trace capability. Pick-and-place-robots can also be used to sort products for packaging after exit from the HPP equipment.
Who Uses HPP?
In the earlier days, Quintus Technologies built a large number of HPP systems under Avure’s name, says Williams. “Customers who are using the technologies were pleased with their products. HPP systems performed to high standards in the food industry with high consumer satisfaction.”
“Several companies producing RTE meat, pet food, guacamole, seafood, baby food, beverages have successfully implemented HPP systems in North America, Europe, Latin America and APAC regions,” says JBTAvure’s Raghubeer. “In addition to the large global network of HPP service providers, many companies operate their own HPP systems such as Wholly Guacamole, Good Foods, Prestige Oysters, Hormel Foods, Hyungkuk F&B, Gordian, Motivatit Seafood, Frutas Montosa, Stella & Chewy’s, and several others.”
Hiperbaric’s Zapata added to the list Suja Juice, MUSH, Demakes Enterprises (Old Neighborhood Foods), The Alpine Wurst, Greenleaf Lobster, Seafarers and Suzannah’s Kitchen. Tolling companies—aka contract manufacturers—include Youngstown Distributors, Dora’s Naturals, Universal Pure, Green Plant, Lineage, LiDestri Foods and Maryland Packaging. Evolution Fresh and Lineage provide automation services.
Tolling Services
Tolling, or contract manufacturing, is well established for HPP, and there are multiple locations throughout the U.S., says CRB’s Moses. The Cold Pressure Council is another place to find contract manufacturers, including Universal Pure, West Liberty Foods and American Pasteurization Company. You can even find universities with capabilities, such as University of Nebraska.
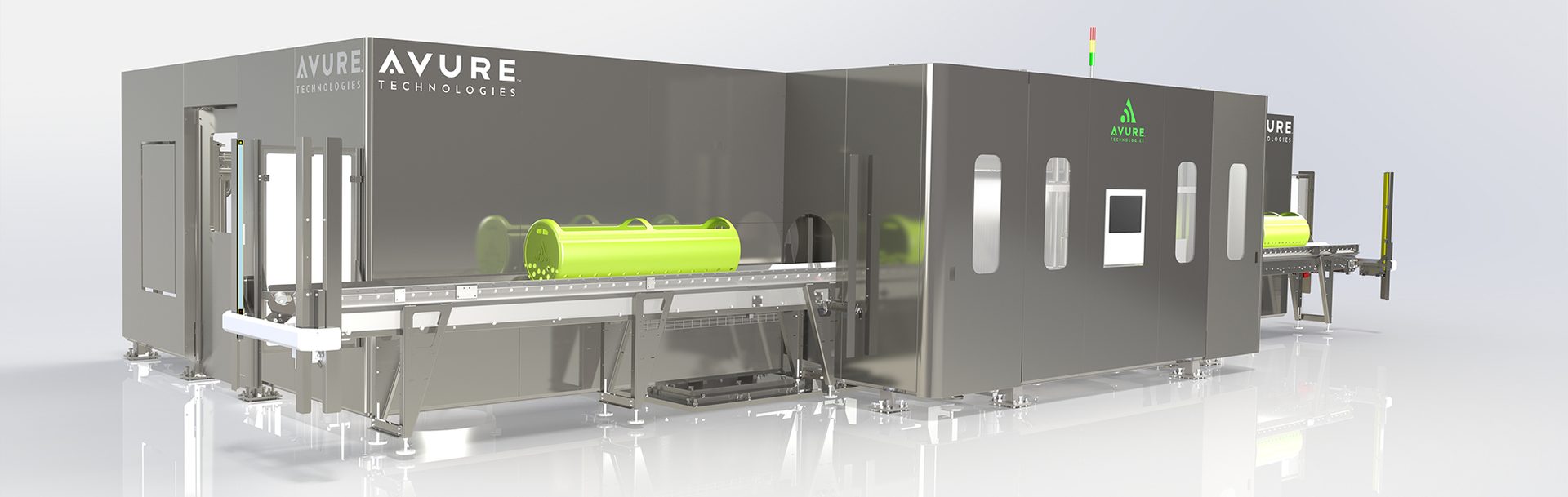
JBTAvure’s Model AV-X is an expandable machine that allowed HPP Food Services, a toll processor in Wilmington, Calif., to increase its system capacity in three days from 40 million pounds to 60 million pounds of products per year, thanks to the “long basket” capability of the equipment. Image courtesy of JBTAvure
Thoughts on the Future of HPP
Aided by digital systems, HPP will see several improvements and operational benefits. Our contributors listed a few:
• Maintenance costs will decline with advanced designs and materials. Maintenance programs will become smarter with automatic scheduling and parts ordering.
• Automation will reduce labor and increase consistency and throughput.
• Lower-cost systems and novel food applications will widen adoption, such as ready-to-eat meals, raw pet food and upcycling suboptimal produce.
• Continued innovation in HPP equipment design and manufacturing will increase energy and water efficiency, throughput, automation and ease of operation while decreasing operating and maintenance costs per unit.
• Data analytics and Industry 4.0 technologies will also enable HPP adopters to maximize process insights, productivity, flexibility and end-to-end integration.
• HPP systems generate vast amounts of data on process parameters, performance, diagnostics etc. Advanced analytics will help extract more value from this data.
• Data mining can optimize HPP treatment for each product by correlating processing data with quality results. Machine learning can continuously improve programs.
• Analytics will also improve preventative maintenance as systems analyze data to predict potential failures or service needs.
• Augmented reality can provide remote guidance for workers doing maintenance.
• Scalable design will lower installation cost and decrease the number of moving parts and components for less wear.
• Smart machines, smart maintenance and use of VFDs throughout will decrease costs.
• Incubator programs will let potential new users test new foods and beverages and their applicability to HPP.
According to Zapata, there are more than 30 commercial tolling facilities in the U.S. alone. Most tolling centers are located strategically based on food industry hubs. For example, in the U.S., California, Texas, Illinois, New York and Florida have multiple tolling sites. Facilities near fresh produce regions (e.g., California) or meat processing centers (e.g., Nebraska) allow easier access for those industries. International tolling providers target processors exporting to or located near their region. There are also tollers in Salt Lake City (Intermountain HPP) and Miami (Green Plant).
According to Kevin Kennedy, JBTAvure North American sales manager, the company’s tolling network serves an important role for many HPP prospects/customers by facilitating their entry into the commercial market. Currently, there are more than 20 companies in 28 locations throughout North America, Canada, South America, South Africa, Europe and Asia. FE
Resources:
“Engineering R&D: MAP for HPP,” FE, 3 May 2012, Kevin Higgins
“Fully-automated HPP Production Line Featuring Hiperbaric 525 System,” YouTube video, https://www.youtube.com/watch?v=U21mrjc7Cy4
Cold Pressure Council, website: https://www.coldpressurecouncil.org/