special report
DISTRIBUTION STRATEGIES
keeping their
cool
Processors need enough cold storage to meet current needs as well as anticipated growth.
Chief Editor
By Fred Wilkinson
Among the top priorities for suppliers and handlers of meat and poultry products is keeping their cool – literally.
Ensuring access to adequate cooling capacity is a key consideration for processors and suppliers that handle regional and/or local refrigerated storage and delivery of meat and poultry products.
Processors need enough cold storage to meet current production and handling needs as well as anticipated growth, said Dan Parsenow, regional sales manager for Polar King International Inc., adding that moving processors’ cold storage outside their facility or adding cold storage outside frees up room inside their facility to be used for processing.
“They don’t want to cut themselves short but also don’t want too big of a walk-in where they are cooling a lot of empty space,” Parsenow said. “Consider redundant refrigeration to ensure back up in case a system was to go down and temperature monitoring with alarm so you can be notified of a problem.”
As costs for refrigerated storage space continue to increase, processors can help contain those costs by having their own cold storage, allowing them greater control over that portion of their business, Parsenow said.
As the costs for refrigerated storage space continues to increase, processors can help contain those costs by having their own cold storage, allowing them greater control over that portion of their business.
Loading efficiencies
A crucial link in the cold chain and a potential source for inefficiency exists when loading or unloading frozen or refrigerated meat or poultry products from a refrigerated trailer at a loading dock.
The need to open trailer doors on the drive approach presents inefficiencies to the loading process, as either the driver or the dock attendant must leave their workspace to open the trailer doors before backing into the dock position, said Walt Swietlik, director, loading dock automation solutions for Rite-Hite.
“This increases the time to load or unload, and it exposes the frozen or refrigerated food to the outside environment,” Swietlik said. “Depending on the length of exposure, this could result in damaged goods. Prevention of outside air infiltration during the loading and unloading process is especially important for the refrigerated food industry due to their strict regulations that must be followed for temperature control, sanitation and security. If there is an infiltration of dirt, pests, or even the wrong air temperature, this can greatly affect the quality of the refrigerated foods being transferred.”
To help ensure the cold chain remains intact during loading and unloading, the trailer must be backed flush against the building, leaving the security seal intact until the trailer doors are unlocked and opened inside the facility, Swietlik said.
“This helps ensure that the trailer was not tampered with or opened from the time it left the last facility for greater supply chain security and product temperature control,” he said. “The same will happen as the trailer is reloaded and leaves the facility. The trailer doors are locked, and security tag is added inside the facility to help prevent any other outside interaction.”
Due to labor shortages in many facilities, there is a need to automate processes to keep up with demand, and that includes loading and unloading product from refrigerated trailers. Adding automation in this area of product handling doesn’t necessarily mean replacing workers but finding areas that can free up workers to do roles better suited to their job, Swietlik said.
“Facilities can choose the right ratio of automated vs. manual processes to best meet their needs and increase productivity,” he said. “No matter the level of automation chosen, it’s important to select partners early in the planning process to collaborate with every step of your automation journey.”
With labor issues escalating and consumer preference rapidly growing, cold storage services solutions provider Lineage Logistics determined the answers lie in adding automated functionality to their facilities, said Brian Beattie, president Western U.S. operations for Lineage Logistics.
“Our data science team is constantly working to create the most efficient cold chain warehouses in the world,” he said.
That includes designing and engineering simulations that result in the development of specific technologies to solve the company’s most challenging operational problems, which include waste in the supply chain, ensuring trucks are at the right place at the right time and reducing the amount of time team members are exposed to the freezing temperatures of the facilities.
“Automation at Lineage is also core to our commitment to energy efficiency and sustainability,” Beattie said. “We combine deep institutional knowledge with industry-leading transformative thinking to implement several energy reduction technologies that are achieving dramatic decreases in consumption. As an example, flywheeling, an innovative process that proactively manages energy consumption, lowered our energy usage by 34% — an annual savings of 33 million kilowatt hours, in the first three years.”
Opening image credit: GettyImages / Dragos Cojocari / iStock / Getty Images Plus
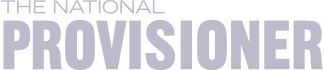