Shortcut to a Natural Look
Inherently Matte Acrylic
–Credit: Arand, via Getty Images–
By Fabian Gyger, Michael Lucas, and Benjamin van den Boom, Zschimmer & Schwarz GmbH & Co KG, Lahnstein, Germany; Kim Öhlenschläger, Zschimmer & Schwarz, Wissembourg, France; and Kaitlyn Funk, Zschimmer & Schwarz, Louisville, Kentucky
Matte paints and coatings are a major trend across multiple substrate and application fields. From automotive surfaces to furniture and beyond, matte finishes have become synonymous with sophistication and contemporary aesthetics.
In the realm of wood coatings, achieving a "natural look" has become a hallmark of modern design. To accomplish this, not only low gloss is required but also high transparency to preserve the vibrant colors of the wood. Beyond visual aesthetics it is also important to preserve the genuine, natural feel of wood. The essential function of the coating is, of course, to preserve the aesthetics or the natural look of the wood or surface. For this purpose, the coating requires good scratch and burnishing resistance. As wood surfaces are subjected to daily wear and tear, mechanical resistance ensures that the matte surface of the coating is maintained, preserving the natural appearance over time. Another crucial property is stain resistance. The protective layer acts as a barrier against potential stains, safeguarding the wood from unsightly blemishes that could compromise its natural appearance and a stain-resistant coating significantly contributes to the longevity of the wood's natural look.
In a similar manner, matte overprint varnishes (OPVs) play a crucial role in high-quality print products, as they enhance both visual appeal and functionality. Alongside a very-high transparency that ensures color strength, particularly in dark hues, resistance to polishing and scratching, as well as a velvety touch, are essential here. Since OPVs are frequently adjusted to intermediate gloss levels, precise formulation is crucial in this context.
A primary discriminator between glossy and matte coatings lies in the surface roughness characteristics. Glossy coatings typically exhibit a smoother surface, resulting in specular reflection and a mirror-like shine. In contrast, matte coatings introduce controlled surface irregularities that diffuse light, creating a subdued and non-reflective appearance (Figure 1).
FIGURE 1–ǀ–Light diffraction in glossy and matte surfaces.
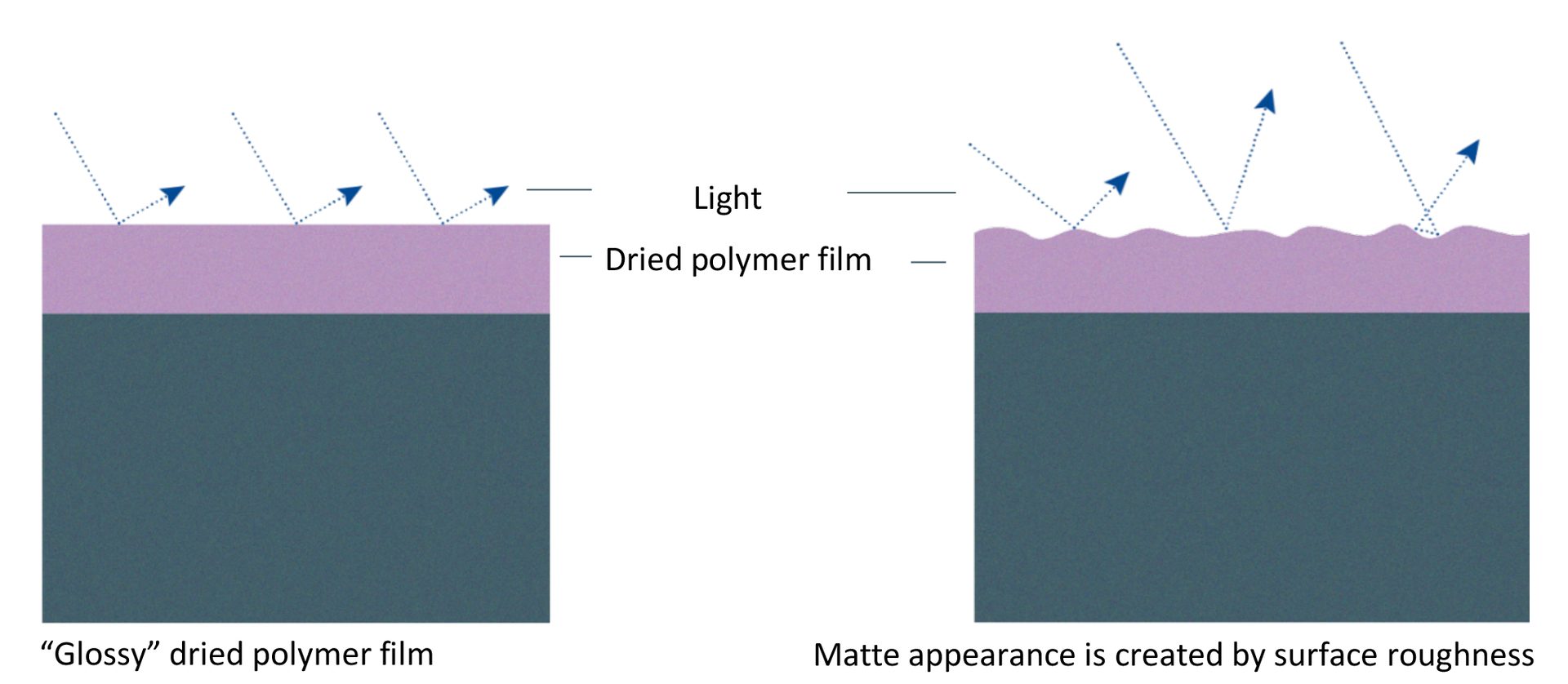
For the matting of coatings, conventional matting agents such as micron-sized particles, including micronized waxes, silica particles, and polymer beads, are widely employed to achieve desired surface properties. While these agents often effectively produce a matte appearance in the coating, they also present various challenges both in formulation and in the dried film.
In conventional matting agents, micron-sized particles contribute to surface roughness, imparting a matte appearance to coatings. Although they yield a matte surface, their distribution across the entire film results in limited transparency. Achieving burnishing resistance is often a challenge, particularly with silica-based matting agents. In addition, the settling of pigments in the coating is problematic, leading to uneven distribution and potential optical inconsistencies. Similar issues arise with polymer beads. In the case of micronized waxes, challenges such as surface migration, where wax particles migrate to the surface of the coating, can affect the overall visual effect. In formulation, particle settling can lead to an unstable gloss value, impacting the appearance of the coating. The addition and dispersion of particles potentially increase viscosity, providing less flexibility in adjusting the application-specific rheology profile. Moreover, hydrophilic dispersing additives commonly used with these matting agents can compromise stain resistance. Burnishing resistance is often lacking when particles cannot be effectively fixed within the coating matrix. Addressing questions related to transparency, distribution, stability, and fixation remains an essential component of optimizing the performance of matte coatings.
Inherently Matte Acrylic Technology
Zschimmer & Schwarz has developed an inherently matte, water-based acrylic technology. Polymers based on this technology form a transparent film with low gloss during the drying process. It is a water-dispersed pure acrylic polymer without the addition of additional matting agents. It can and must be formulated like a conventional acrylic to develop the matte properties.
The matting properties are based on a particle size distribution in the dispersion that is in the correct range to provide a matte appearance to the film when interacting with light and kept during film formation (Figure 2a and 2b).
FIGURE 2–ǀ–a. Particle size distribution leads to light diffraction; b. Particle size distribution during film formation phase.
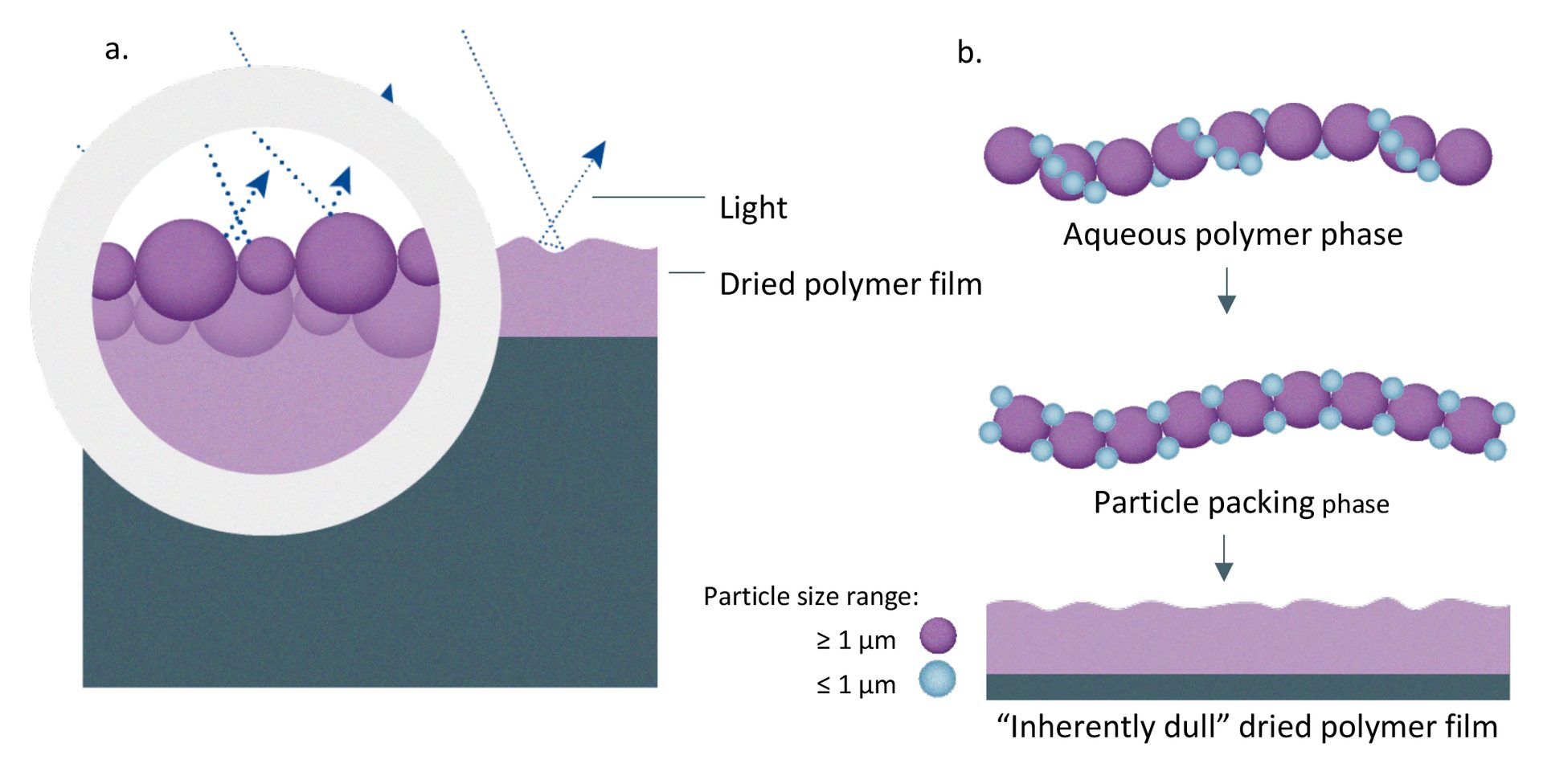
This particle size distribution can be maintained beyond the aqueous phase through suitable formulation during the film-forming phase. The result is shown in Figure 3, where scanning electron microscope (SEM) images of a dried film formulation of an inherently matte polymer are presented. In the formulation, this polymer was formulated without additional co-binders. The rough surface structure, clearly visible here, is responsible for the matte effect. This rough surface, composed of a hard acrylic, also provides a tooth-like touch that effectively imitates finely sanded wood.
FIGURE 3–ǀ–xxx
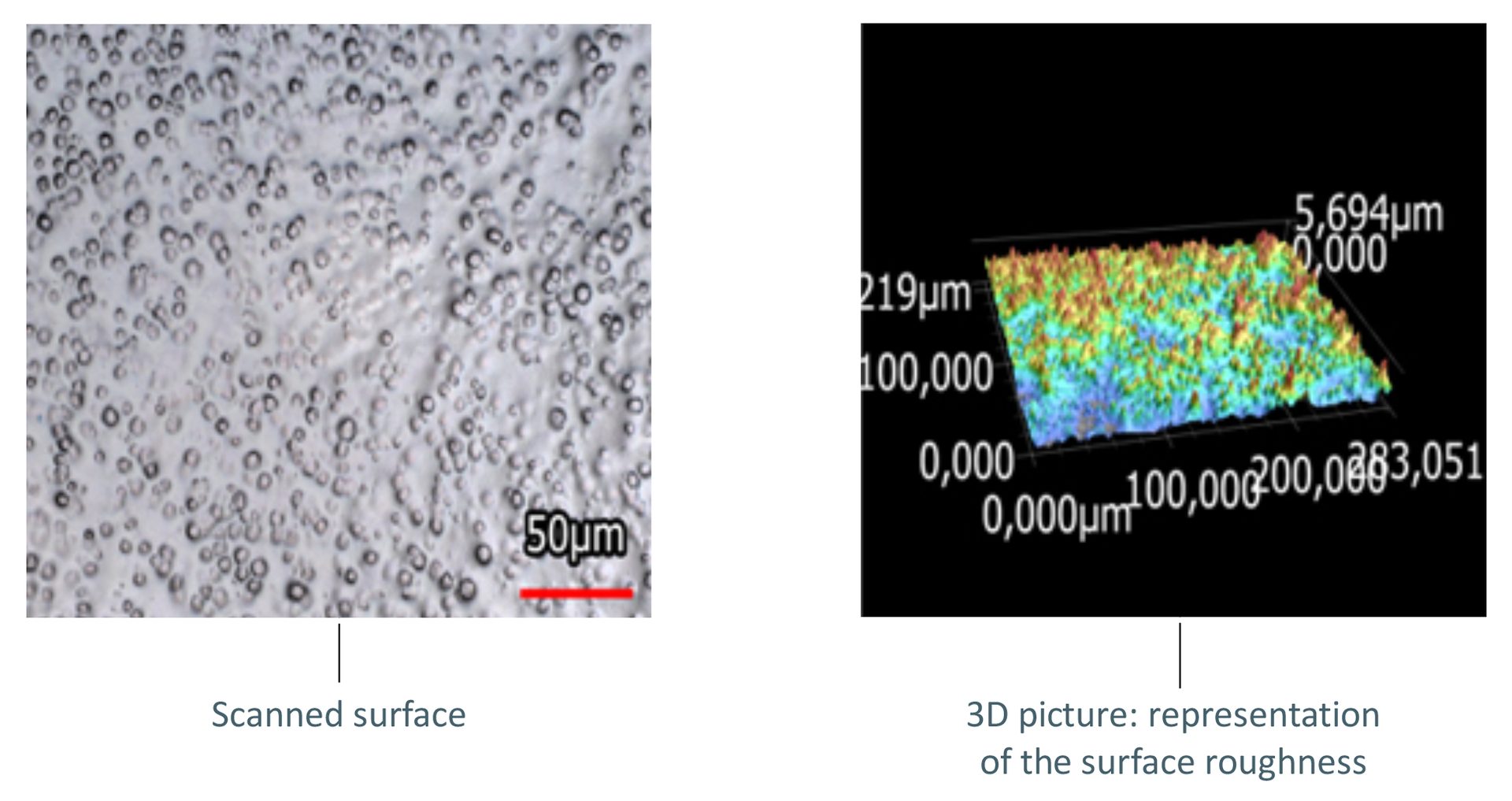
Crucial for maintaining the particle size distribution after film formation is the choice of the coalescent, which can be made from a reasonably common selection but should be chosen carefully. As is typical for a water-based polymer, the coalescent facilitates improved film formation at lower temperatures, thus lowering the minimum film formation temperature (MFFT). Optimal film formation is a prerequisite for achieving effective protection, such as stain resistance. However, the particle size distribution can be disrupted by the action of larger quantities of high solvency and especially high-boiling solvents, ultimately resulting in a significantly increased gloss. A simplified working formulation is shown in Table 1. The choice of solvents, for example, from DPM, DPNB, texanol, corresponds to a typical selection in the realm of room-temperature drying coatings.
TABLE 1–ǀ–Exemplary formulation of the pure inherently matte acrylate.
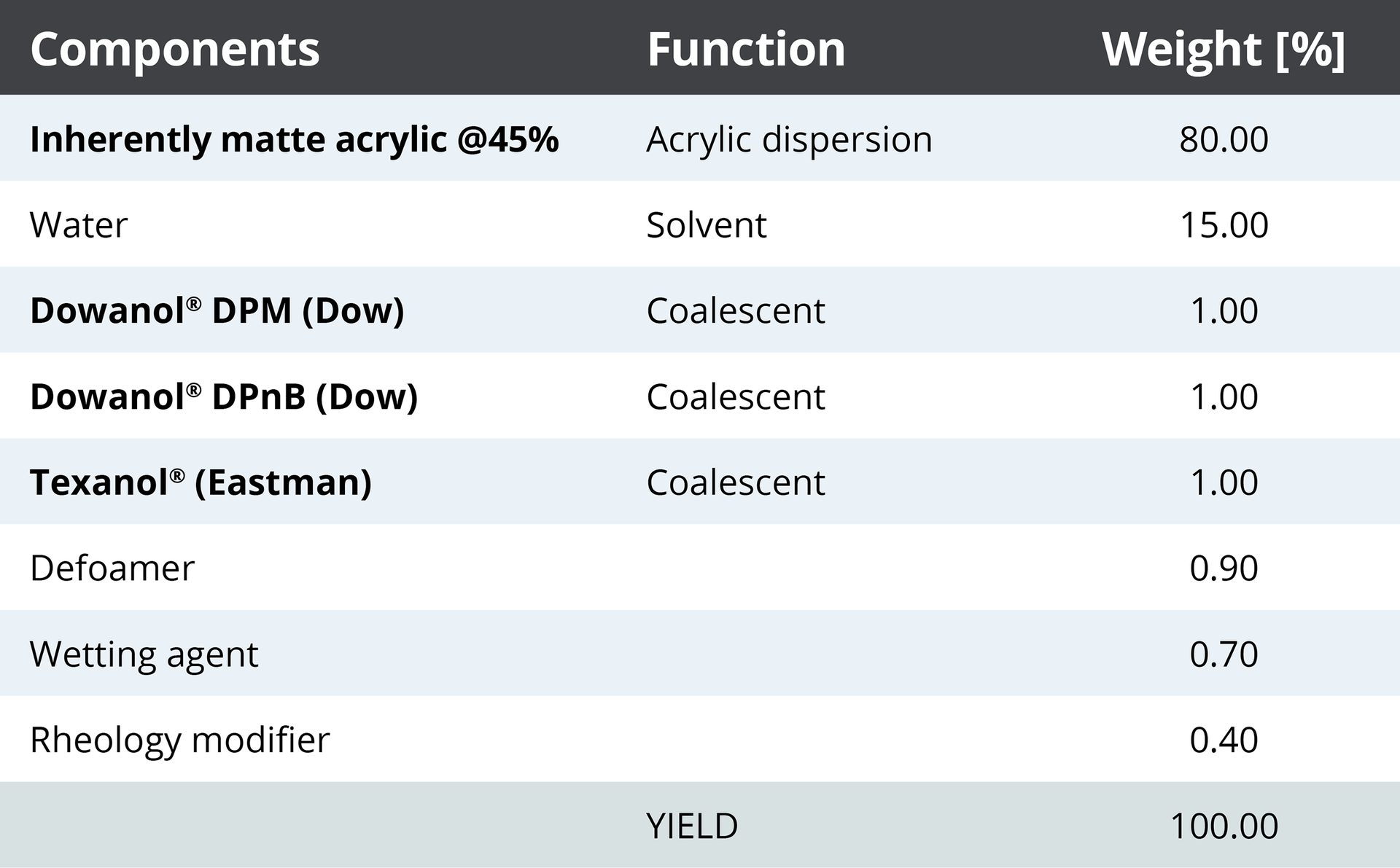
A major advantage of this technology is its perfect transparency. Crucial for the matting effect in all systems, whether conventional matting agents or inherently matte polymers, are always the surface characteristics. In the case of conventional matting agents, this means that all particles not on the surface do not contribute to the effect but naturally lead to a loss of transparency. This effect also scales with the thickness of the coating. In the case of the inherently matte polymer an acrylic film is formed with a surface roughness. This effect only affects the surface, meaning transparency is not influenced by matting and, in particular, is independent of the coating thickness. Figure 4 shows a blend of a pure acrylic with an inherently matte acrylic. Here, it is evident that transparency remains constant across the entire blending range, resembling a "normal" acrylic. Furthermore, it can be observed that the gloss level is proportional to the proportion of the inherently matte polymer used in the total binder. In other words, the greatest matting effect can be achieved with the pure inherently matte polymer. On the other hand, the graph also demonstrates that especially in the medium-matte range, a very precise adjustment of the gloss level can be achieved.
FIGURE 4–ǀ–Gloss reduction/transparency of a mixture of a pure acrylic and an inherently matte polymer.
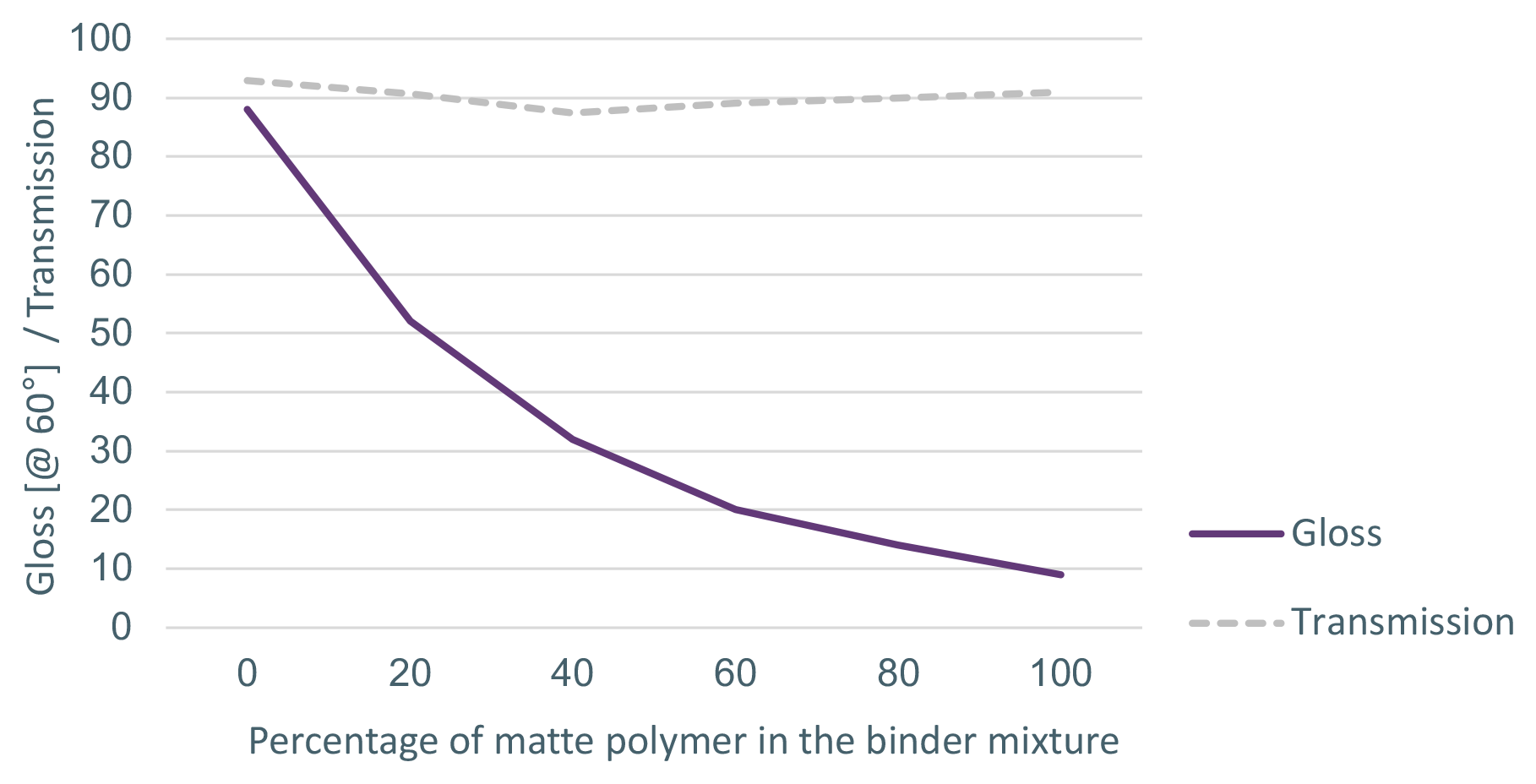
The benefits of high transparency combined with a very simple and precise gloss adjustment can be utilized, for example, in overprint varnishes. Table 2 shows a simplified, very straightforward formulation of an OPV, which was adjusted to the silk matte range with the help of a co-binder.
TABLE 2–ǀ–Exemplary formulation of a matte OPV.
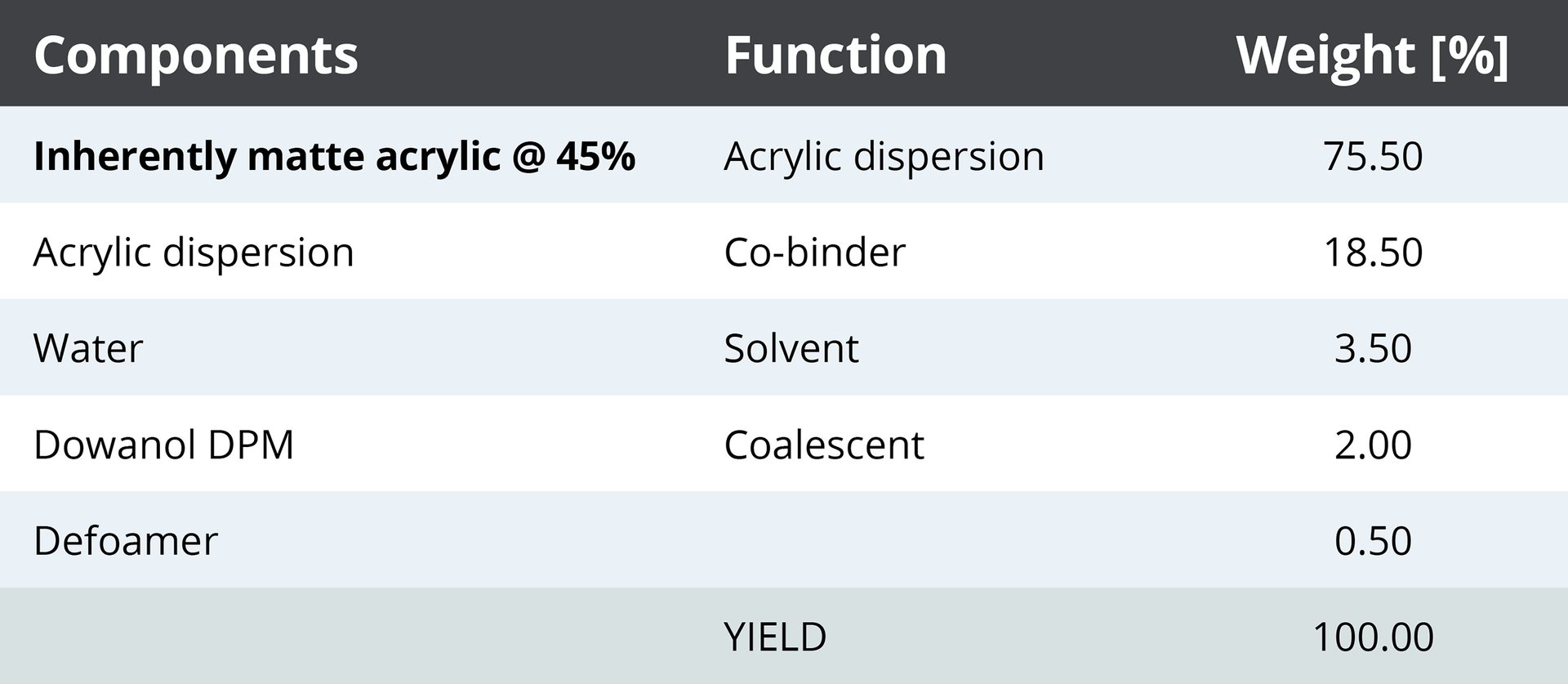
Figure 5 illustrates a simple comparison between a (strongly) matted overprint varnish and the matte clear coat of the formulation shown in Table 2. Due to the loss of transparency, color intensity, especially in darker tones such as red or black, significantly decreases in the former. This is not the case with a matte clear coat with high transparency, where color intensity can be perfectly preserved.
FIGURE 5–ǀ–OPV with inherently matte polymer and conventional matting agent.
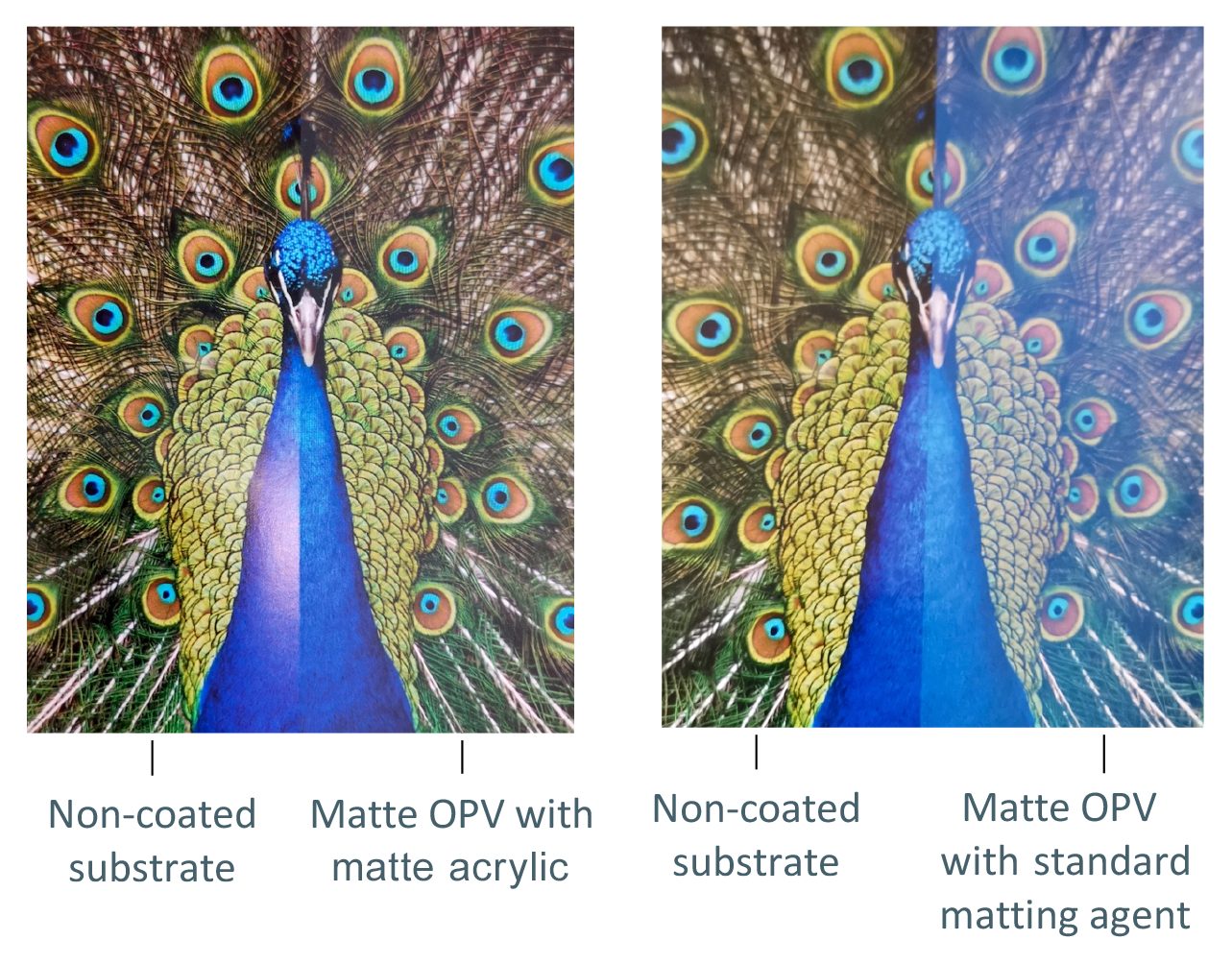
Another important application of this technology, as described earlier, is as a topcoat on wood, preserving the "natural look" of the wood. For the experiments, in addition to the formulation shown in Table 1 (see above), another formulation supplemented with a 20% co-binder content is used. In this case, the co-binder is a water-based acrylic with good stain resistance. Alternatively, polyurethane dispersions could be used to achieve further improvements in scratch and stain resistance. Another possibility to influence chemical and mechanical resistance is additional crosslinking, where, for example, acid groups or existing hydroxy functionalities can be utilized. In the formulations shown and tested, a polyaziridine or a polyisocyanate was used in a two-component formulation (2K). Table 3 and 4 give an overview the tested formulations.
TABLE 3–ǀ–Exemplary formulation of a matte clearcoat (1K).
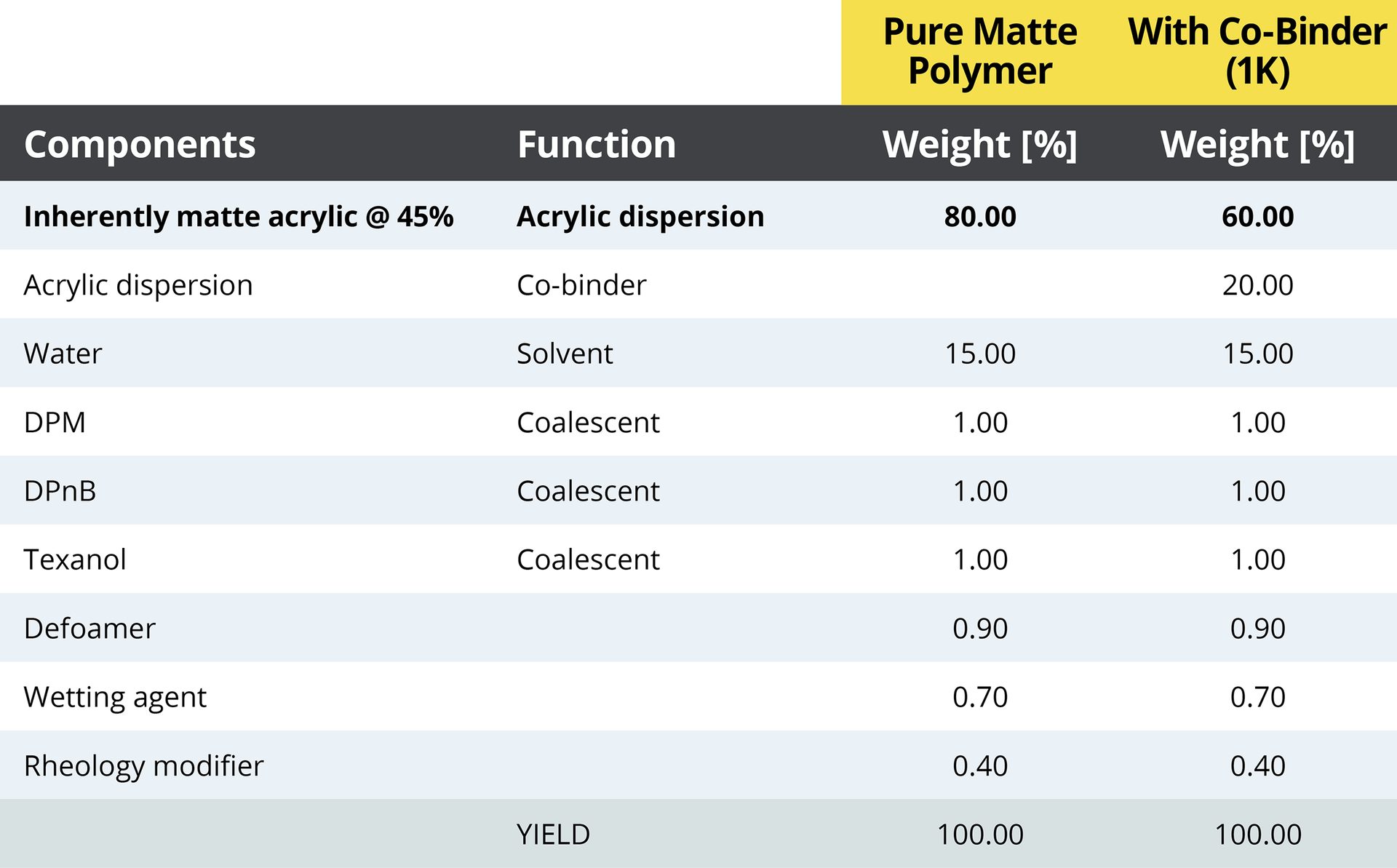
TABLE 4–ǀ–Exemplary formulation of a matte clearcoat (2K).
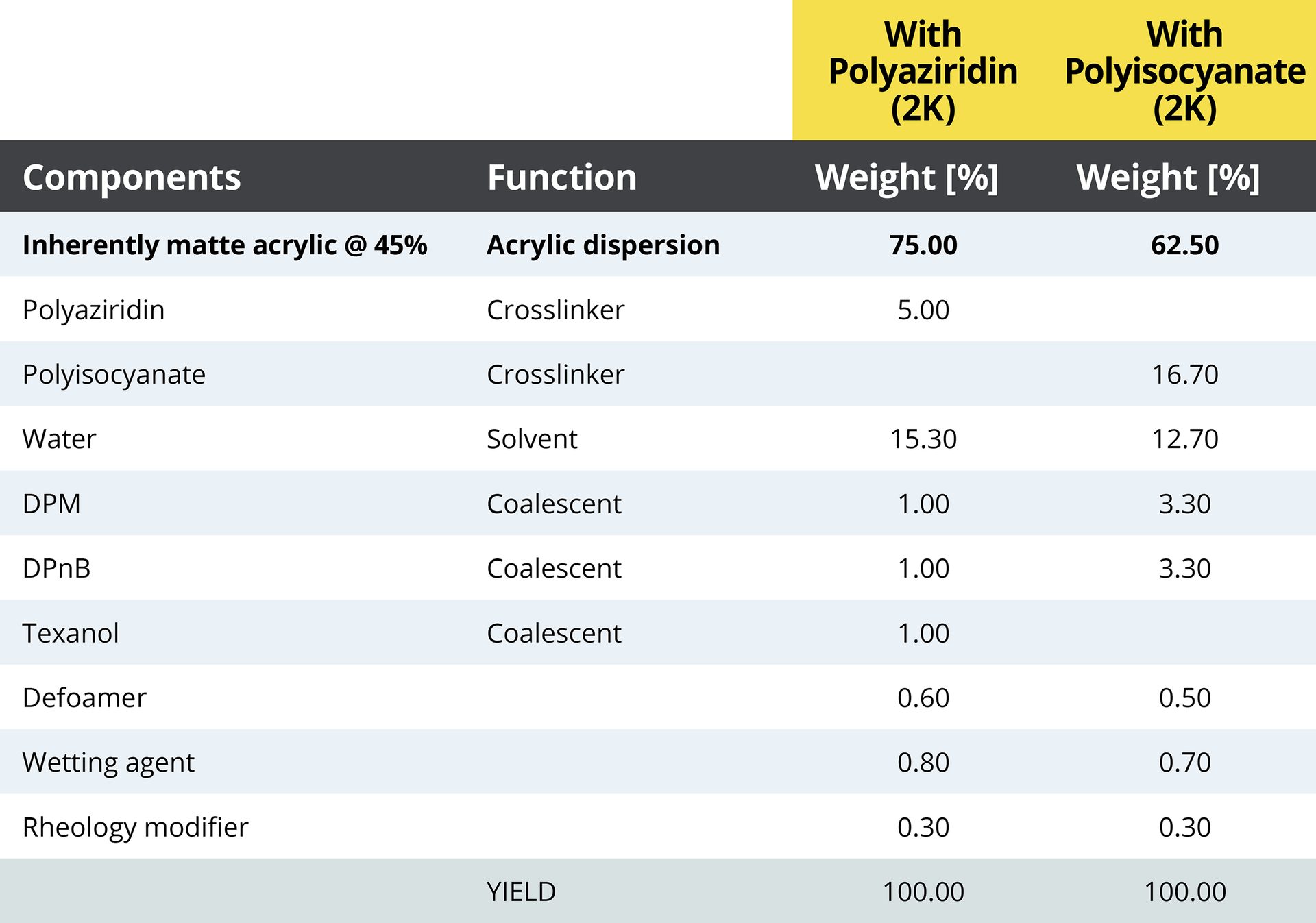
The results of spot test are presented in Table 5 and Figure 6 for both the 1K and 2K formulations. Here, the scale ranges from 0 as the worst to 5 as the best result without any color changes after cleaning the surface. Results of gloss levels are also presented here.
TABLE 5–ǀ–Comparison of different formulation variants of the inherently matte polymer.
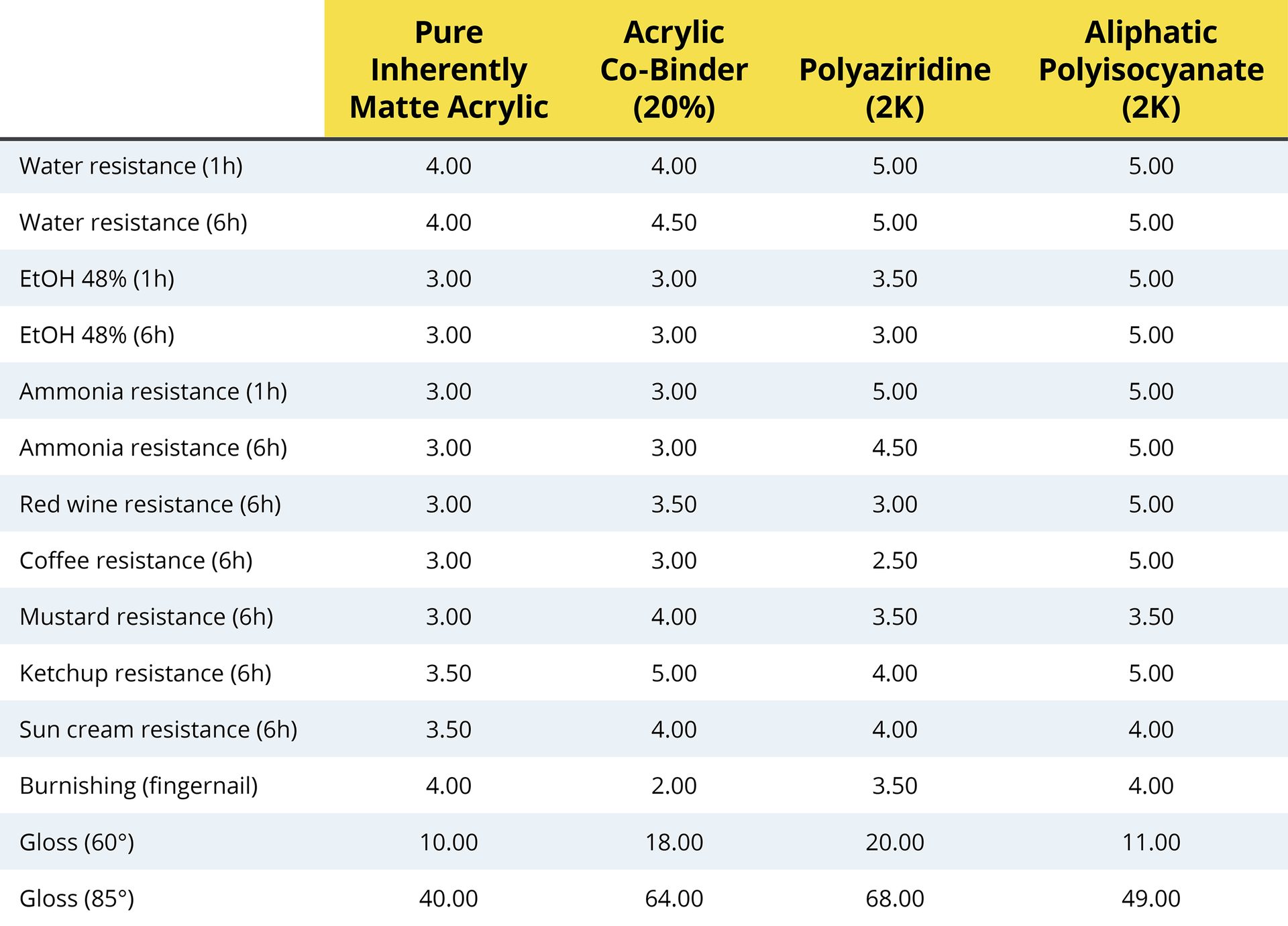
FIGURE 6–ǀ–Comparison of different formulation variants of the inherently matte polymer.
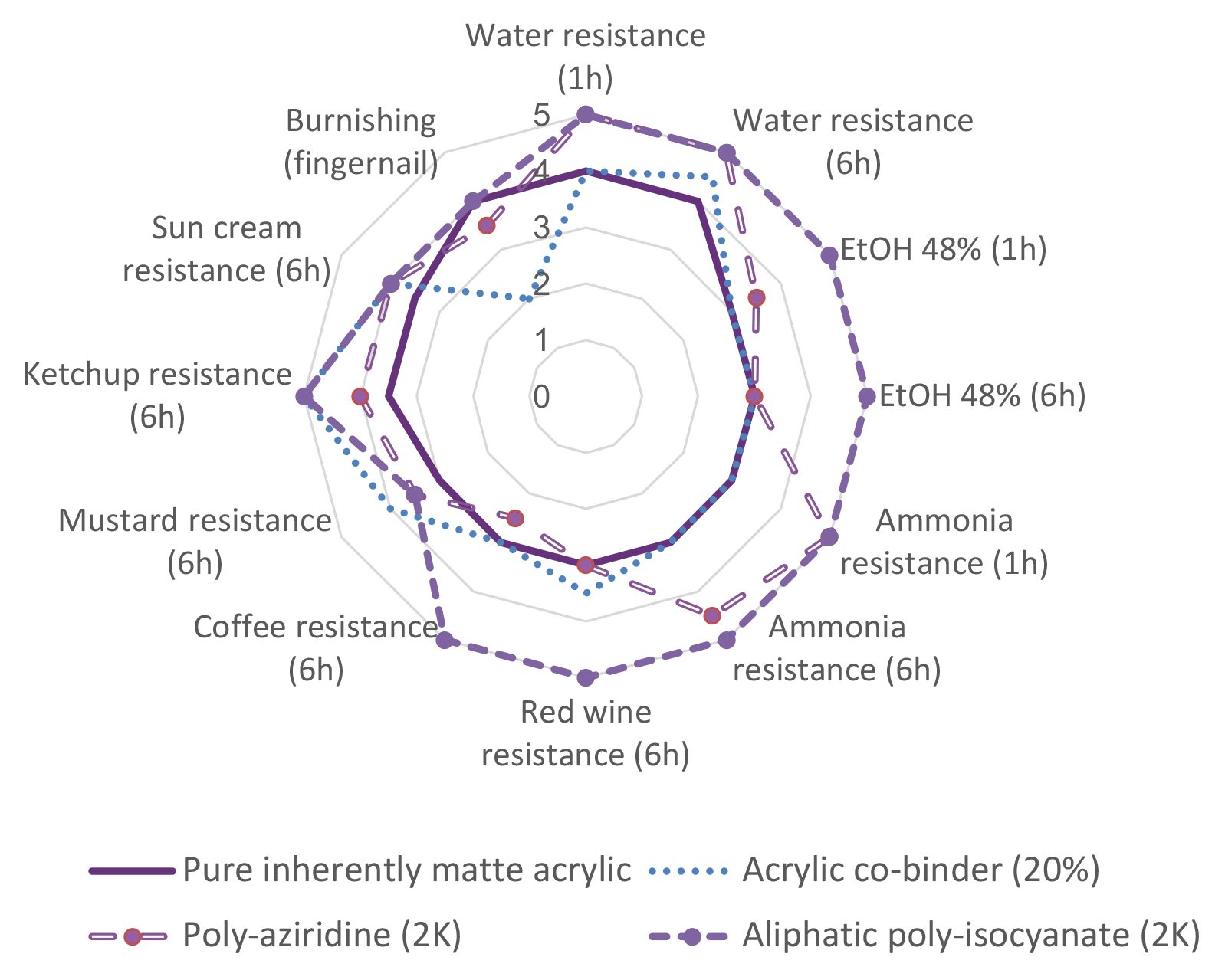
In summary of the results, the matte polymer yields good results regarding burnishing resistance but still has room for improvement in terms of stain resistance, especially for topcoats with high-quality requirements, such as in the furniture industry. However, this challenge can be addressed primarily through the right formulation. Suitable co-binders offer a possible path to improved resistance, especially for coatings intended for a medium-matte range, where a larger amount of co-binder can be used.
Another highly effective way to enhance mechanical and chemical properties is through 2K formulations, such as aziridines or isocyanates. With a suitable formulation, a significant improvement can be achieved through post-crosslinking of the inherently matte polymer, as shown in the results in Table 4 and Figure 6. These findings allow for the realization of topcoats for furniture as well.
In addition to performance-related advantages, the use of an inherently matte acrylic polymer provides a range of economic, logistical, and safety benefits in various applications, particularly in clear coatings. The production environment benefits from the absence of dust, contributing to a cleaner and safer workspace. Moreover, the inherently matte acrylic enables a more efficient production process, resulting in shorter production times and reduced energy consumption.
The reduction in the number of required raw materials also leads to a decrease in material costs. The formulated product, unlike other matte systems, exhibits no settling behavior and maintains a stable gloss value, ensuring consistent quality.
Conclusions
Zschimmer & Schwarz's inherently matte acrylic technology offers a novel approach to creating high-quality matte formulations on an acrylic basis. It demonstrates comparable or even superior performance to traditional matte coatings in many applications within the semi-low gloss range, making it a cost-effective and efficient alternative. In specific applications, such as wood coatings, the inherently matte acrylic stands out for its "natural look." Its use ensures optimal color strength in printing inks and coatings, contributing to the aesthetics of the end product.
Moreover, the acrylic polymer distinguishes itself with stability and precision in adjusting gloss values. Additionally, the inherently matte acrylic provides a stable and natural tactile experience, emphasizing its adaptability across various industries. In terms of stain resistance, it exhibits a decent performance and is therefore more suitable for use in areas with somewhat lower requirements. Coatings in the higher requirement range, such as furniture or floor coatings, can be formulated using a post-crosslinking chemistry with compounds such as aziridine or isocyanate.
This paper was presented at the 2024 Waterborne Symposium in New Orleans.