FORMULATING WITH MIKE
Concrete Coatings, Part I
The Substrate
Video credit: Hamster3d / Vetta via Getty Images
By Mike Praw, Senior Applications Scientist — Paints, Coatings and Inks, Indorama Ventures: Integrated Oxides and Derivatives, The Woodlands, TX
In this and subsequent columns I will be covering coating concrete. First concrete will be discussed, and in subsequent columns the coating will be covered.
Coating concrete is one of the more difficult tasks due to the variability of the substrate, and the wide variety of properties needed by the coating. The subject of concrete coatings covers a wide area of protective, functional, and decorative coatings. The coating choice is determined by the substrate (concrete) condition, environmental issues, and the desired application and performance requirements as well as by who is applying the coating (a contractor, or a homeowner). Whatever the ultimate purpose of the coating may be, it is critical that we understand concrete as a substrate, limitations on coatings technology, as well as its proper surface preparation.
The most-used building material is concrete. It is a mixture of water, portland cement, aggregates (sand, gravel), pozzolans (soda ash), additives, and air. Simply put, concrete is cement with aggregate filler, and in this mixture, water combines with cement to form a rigid mass. While high in strength, concrete is a brittle and fragile material. Physical attacks cause failure: concrete is porous, and water is absorbed and released within the concrete, causing spalling or cracking. Abrasion wears away the surface, and the porous nature of the concrete permits easy staining. Therefore, it is necessary to protect the surface of the concrete from deterioration and contamination by applying a coating. Surface preparation is the only way to improve the durability and adhesion of applied coatings. In addition, concrete is highly alkaline in nature, so coatings must be alkaline-resistant.
There are several reasons to coat these surfaces:
• To seal against moisture and help reduce dust caused by wear.
• To impart longer life and better wear (chemical and abrasion resistance).
• To impart functional properties, such as non-skid surfaces, luminescent effect, static control, etc...
• For aesthetics (often the most important to the end user).
ADVERTISEMENT
Coating concrete is one of the more difficult tasks due to the variability of the substrate, and the wide variety of properties needed by the coating.
Due to the vast area of concrete coatings, I will concentrate on one-component coatings. In recent years, decorative coatings for concrete have gained popularity. These are primarily acrylic emulsions based. Health, environmental, and ease of application concerns are important, as the applicator experience and skills are extremely variable. I once said 99% of paint problems are on the wrong end of the paint brush, and after almost 40 years in the industry, I feel that number may be low. Increasing government regulations limiting organic solvents (volatile organic compounds or VOCs) continue to be severe and affect the performance of the coatings. It is a challenge to formulators and resin producers to bring user-friendly products that meet the performance levels that the market demands.
These concerns lead to certain restrictions in technologies for this market. While high solids, solventborne, and two-component (2K) systems can be used by contractors, products for the do-it-yourself (DIY) market are generally limited to one-component (1k) waterborne systems.
Concrete is a highly variable substrate, and the aggregate used, ratio of cement to aggregate, and what admixes are added all play a huge role in the final properties. The aggregate size and type are highly variable, anywhere from sand to limestone to granite. The porosity and surface texture of these aggregates will affect adhesion of the coatings. Another area of concern is the porosity of concrete. Liquids and gasses freely move through the concrete. This movement allows water to pass through the concrete, dissolve water-soluble minerals and other components, and allow them to move through the solid concrete with the water. Once the water reaches the surface of the concrete it evaporates, leaving these components on the surface. In fact, salt crystals can form below the surface layer. This transport of minerals leads to efflorescence, a whitish powder left on the concrete surface by mineral crystals deposited there. As we see increased use of visible concrete in construction, efflorescence is often trapped under the film. This leads to issues such as loss of adhesion or unsightly white patches in stained concrete or below the film with clear-coated concrete. Efflorescence plagues all areas of concrete professionals, from general contractors, builders, concrete finishers, and especially concrete coaters, and can be an appearance issue only, but will show the presence of excessive water.
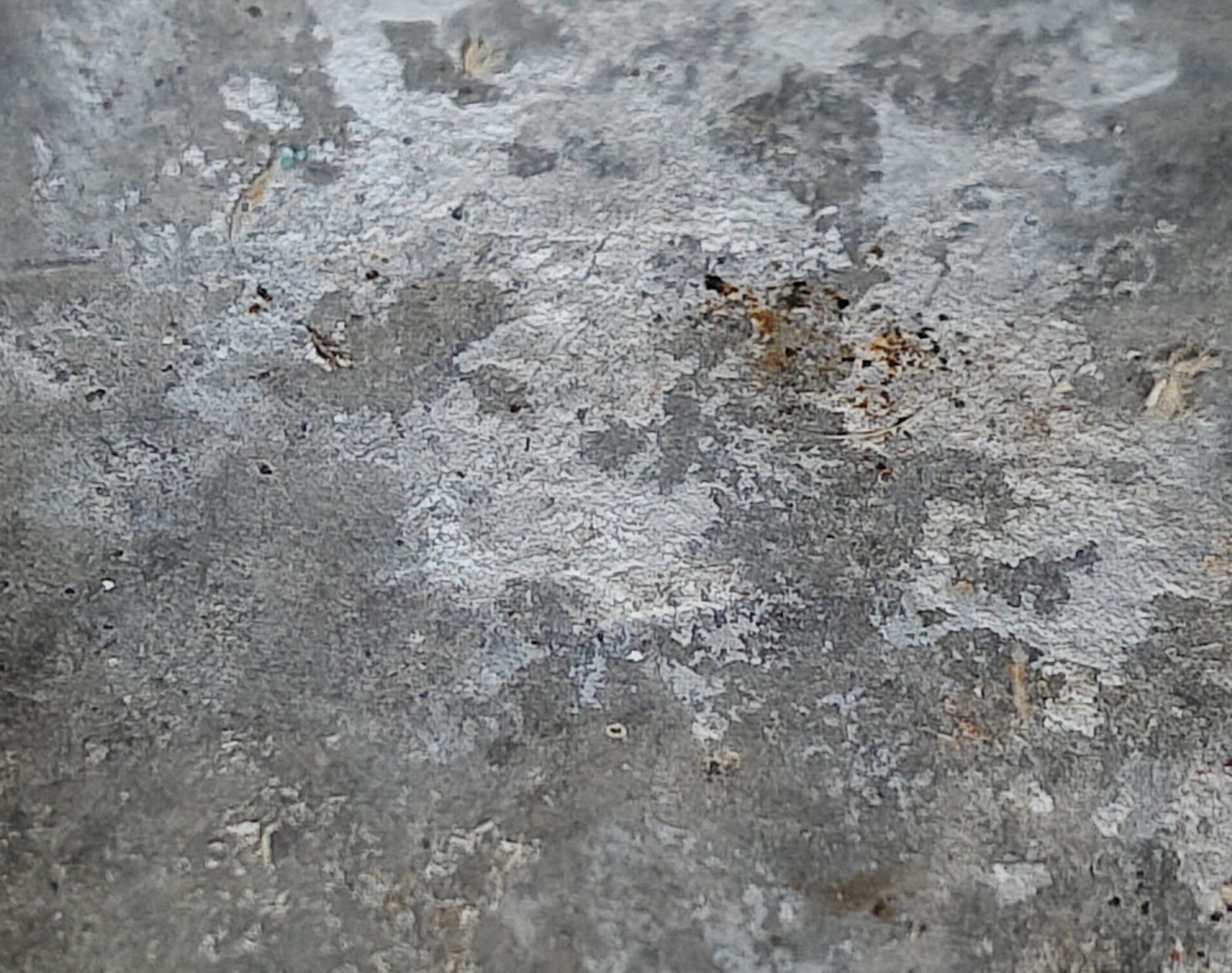
–Courtesy of Michael Praw–
Example of efflorescence.
The aggregate used, ratio of cement to aggregate, and what admixes are added all play a huge role in the final properties of concrete.
Any water can lead to efflorescence, including excess water added to the concrete to aid in flow or application. Often the source of this water is below the concrete, and hydrostatic pressure and concentration gradients increase the movement through the concrete. Minerals dissolved in the sub-grade water will also move through the concrete and crystalize at the air/concrete surface, increasing efflorescence. The efflorescence and hydrostatic pressure can also cause coatings defects. If the coating is permeable to water or vapor pressure, the crystals will form within the top layer of concrete or at the concrete-coating interface. This crystal formation in the top of the concrete will cause the top layer of concrete to lift off (known as spalling) or crumble. The corrosion of the steel rebar in the concrete will cause the steel to expand, and since concrete is brittle, this will also cause spalling. The difference is whether you see rebar below the spalled concrete. As the substrate is weakened the coating will not have a stable substrate to adhere to and will lift. If you look at most concrete coatings where there is loss of adhesion or lifting, the back of the coating will have concrete attached to it, so it is really a substrate failure as opposed to coatings failure.
Hydrostatic pressure is a bit different. If the coating is impermeable to water or has limited water-vapor permeability, coating or substrate failure can arise. The water below the concrete has pressure put on it from the weight of the concrete/building, compressing the substrate and from the weight of water above the concrete. Above-grade water pressure and osmotic pressure within the substrate brings water in, and the only way out is through the concrete. This leads to efflorescence mentioned above, but the pressure also is applied to the coating. There are three main failures this pressure can cause: adhesive failure, cohesive failure, and substrate failure. If the adhesive forces of the coating to the substrate and the cohesive forces within the concrete and the coating are stronger than the pressure forces from the water, the coating will not be affected. If the water pressure exceeds these forces, there will be failure. Adhesive failure is when the coating fails to adhere to the substrate and is common on polished concrete or as a result of a contaminated surface. In most cases, the failure mode will not be adhesive failure. Cohesive failure is when the coating itself fails. In this failure mode, the coating fails perpendicular to the coating substrate axis. I refer to this as the cookie failure, where the creme center fails when you twist the two cookies. This failure is often the result of poor intercoat adhesion, where one coat had poor adhesion to the coat below it. The root cause of this is often where surface energy reducing efforts (flow, wetting, leveling, anti-mar additives, etc.) are incompatible and migrate from one coating layer to the one above it. Additional layers will have more difficulty adhering to the layer below, due to the increased concentration of surface additives. The last and most common failure is substrate failure, where the concrete itself has a cohesive failure.
If the coating is impermeable to water or limited water vapor permeability, potential coating or substrate failure can arise.
This is why substrate surface preparation is so important in concrete coatings. Removing weak concrete from the surface through shot/sand blasting is the most effective method as it also helps remove surface contaminants such as mold release agents, oils, dirt, and efflorescence. The removal of dust left afterwards is critical for proper adhesion. Normally it is recommended to let concrete age before coating it, and 90 days is normally recommended, but check the coating's instructions first.
The alkalinity of concrete is also an issue, as fresh concrete can easily surpass a pH of 14. Over time, acid components from below the concrete will migrate up through the concrete with water and neutralize the concrete. Carbon dioxide in the air will also react with water, forming carbonic acid, and this will also lower pH. If the pH of the concrete is too high, acid neutralizers such as muriatic acid are recommended. However, the salts formed by the acid base reaction need to be removed before coating, and a pressure wash is recommended using copious quantities of water.
In next month’s article, I will discuss the properties needed for concrete coatings, as well as testing.
All information contained herein is provided "as is" without any warranties, express or implied, and under no circumstances shall the author or Indorama be liable for any damages of any nature whatsoever resulting from the use or reliance upon such information. Nothing contained in this publication should be construed as a license under any intellectual property right of any entity, or as a suggestion, recommendation, or authorization to take any action that would infringe any patent. The term "Indorama" is used herein for convenience only, and refers to Indorama Ventures Oxides LLC, its direct and indirect affiliates, and their employees, officers, and directors.