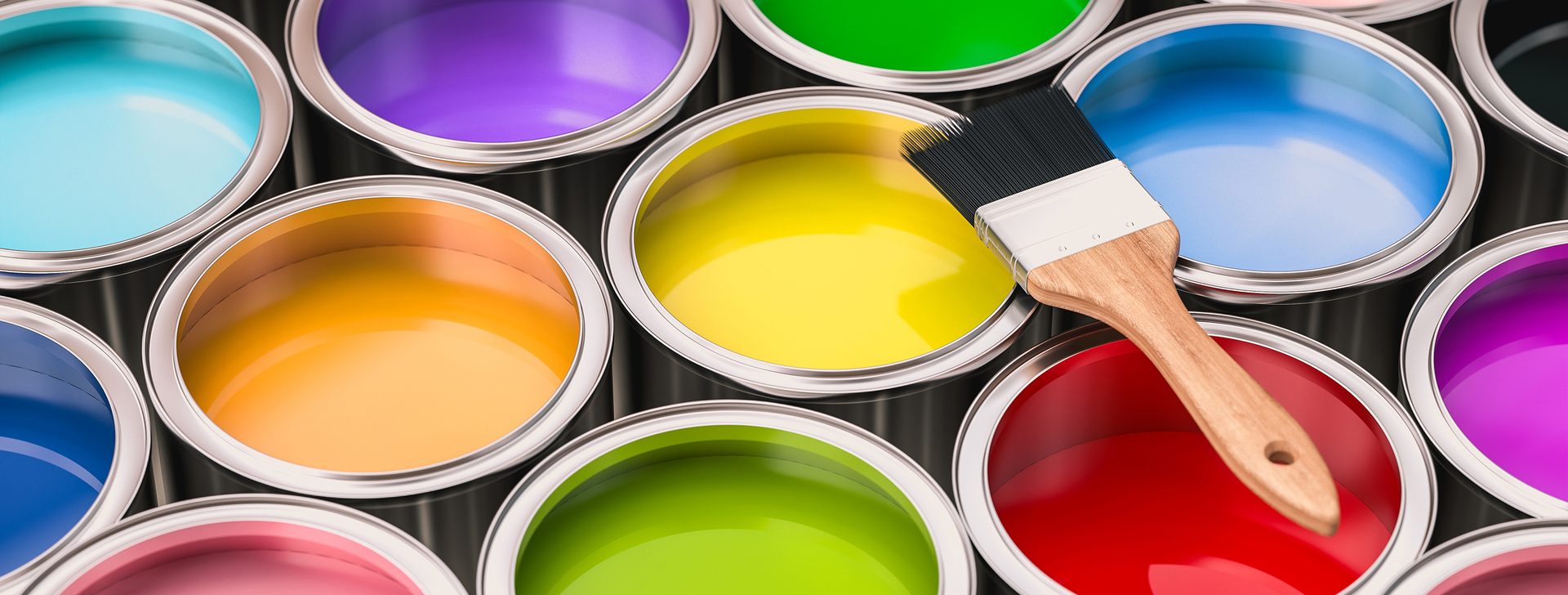
–Credit: tiero, iStock, via Getty Images–
A New
High-Performance Alternative
to Cobalt Driers
By Hiroaki Nakano, Manager, DIC Corporation, Ichihara, Chiba, Japan
Cobalt carboxylates are commonly used as catalysts for the oxidative crosslinking of alkyd resins, which accelerate the drying of paints, inks, and coatings. Despite their effectiveness, alternatives are increasingly sought after, due to concerns surrounding cobalt toxicity. Cobalt 2-ethylhexanoate, specifically, is labeled as Reprotoxic Category 1B by the European Chemicals Agency (ECHA), taking effect from November 2023. Although manganese driers with various ligands are available, few alternatives have been recognized that can match the performance of cobalt driers. To address this issue, the authors of this paper have developed a novel cobalt-free drier that has excellent drying performance and satisfies the requirements of the Globally Harmonized System of Classification and Labelling of Chemicals (GHS).
Design for New Cobalt-Free Drier
For this new design, a new, safer amine ligand with high catalytic activity was selected, along with manganese, a cobalt-free element with much lower toxicity. Manganese neodecanoate was combined with the amine-based ligand, and VOC-free esters used as the solvent in the newly developed DICNATE MV130A.
TABLE 1–ǀ–GHS pictograms.

“O.”
Exxx
Paint Formulation
A paint was prepared with the composition shown in Table 2 and used for the drying performance test of the newly developed drier.
TABLE 2–ǀ–Paint formulation.
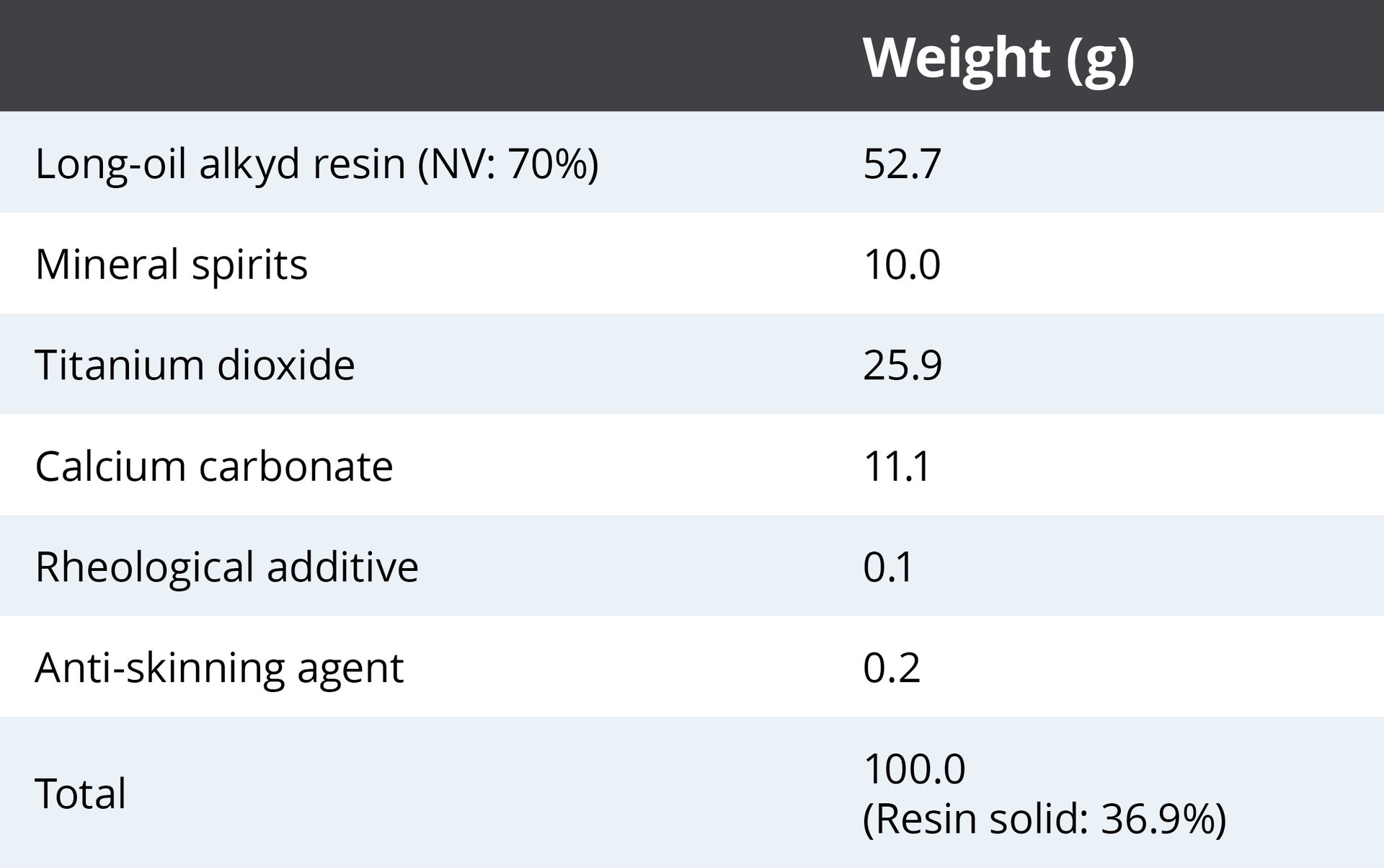
Various driers were added in the amounts shown in Table 3 to the paint prepared by the above formulation. Drier performance was evaluated by drying recorder tests (Table 4, Figure 1, and Figure 2). To confirm the drying performance of the new cobalt-free drier, the performance was compared with that of conventional cobalt driers. In this study, a conventional blend containing Co/Zr/Ca was used as a standard blend, and DICNATE MV130A was examined so that the amount of manganese added to the resin in the paint would be 0.01%, 0.02%, and 0.03%. In addition, for DICNATE MV130A, Zr/Ca was also used as the auxiliary drier.
TABLE 3–ǀ–Drier formulation.
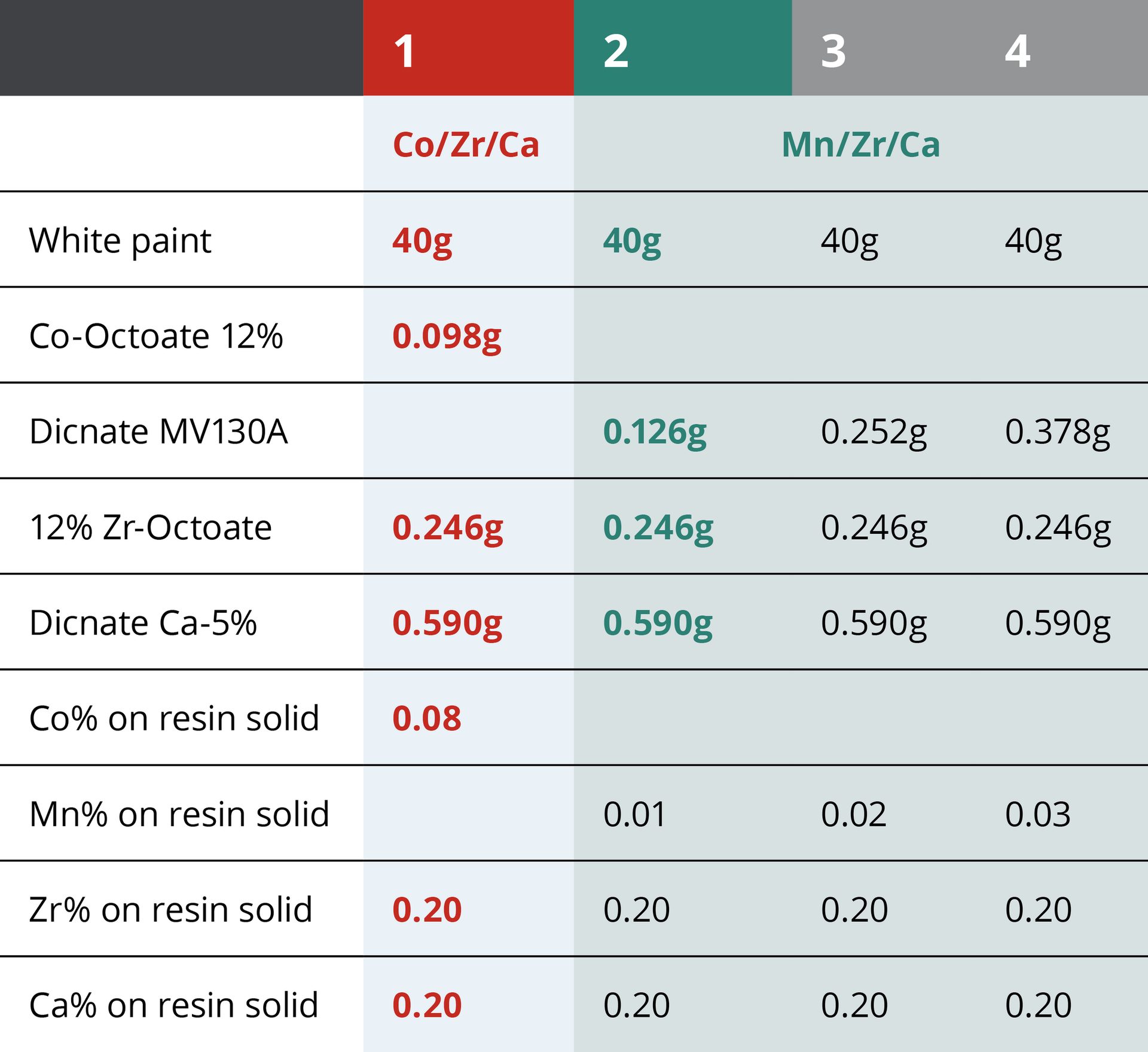
Drier dosage (g) = ((weight of paint (g)) × (resin% of paint) × (metal% on resin solid)) / (metal% of drier)
Test Conditions
- Temperature: 25 °C
- Humidity: 50% RH
- Paint film thickness: 76 μm/wet
Drying Performance
Drying Recorder/Hours
TABLE 4–ǀ–Drier formulation and drying time.
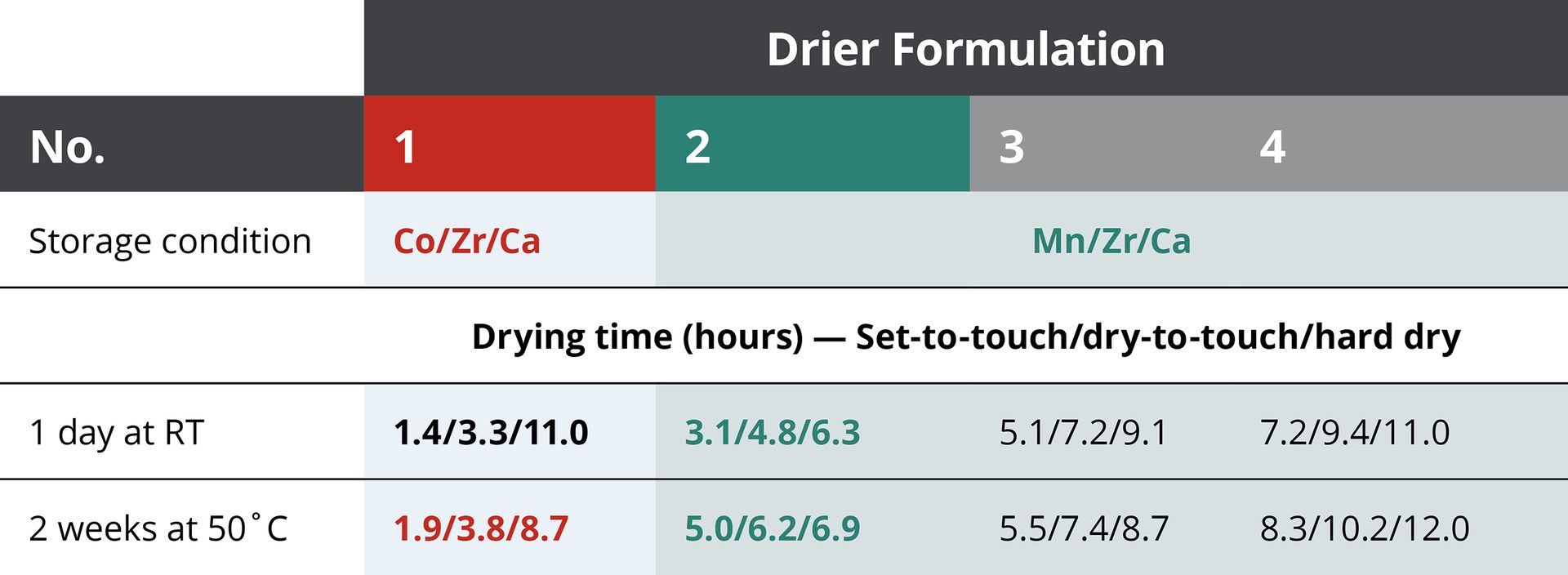
As a result, it was confirmed that the best drying performance was obtained when the amount of manganese added to the resin was 0.01%. It was proven that the hard dry time obtained by the drying recorder test was faster than using a conventional cobalt drier.
The results of the above study are described in Figure 1. This figure shows the result of testing the drying performance of the paint with the drying recorder after mixing each drier in the paint and passing one day at room temperature. As can be seen from the figure, the newly developed combination of DICNATE MV130A/Zr/Ca resulted in hard dry at 6.3 hours, which was approximately five hours faster than the standard combination.
FIGURE 1–ǀ–Coating after one day at room temperature.
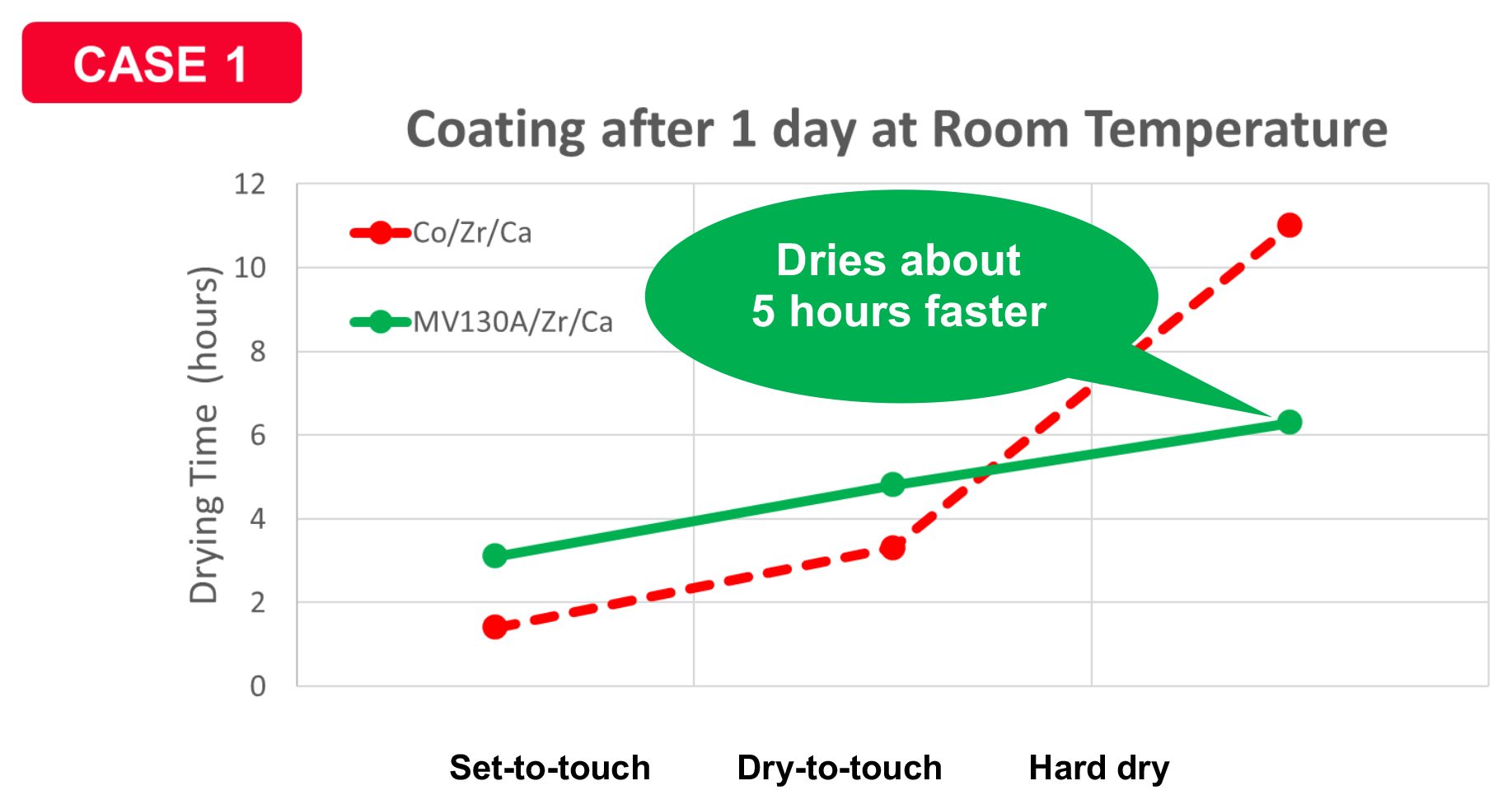
In order to confirm the change in drier performance with time, the drying test was also conducted with drying recorder on a paint that was mixed with a drier and stored at 50 °C for two weeks (Figure 2). As a result, in the standard combination of Co/Zr/Ca, the results of set-to-touch at 1.9 hours, dry-to-touch at 3.8 hours, and hard dry at 8.7 hours were obtained. In the DICNATE MV130A/Zr/Ca combination, hard dry at 6.9 hours was obtained, and it was found that the drying time was about two hours faster than in the standard combination. When evaluating drier performance, it was found that hard dry is one of the most important drying performances, and DICNATE MV130A is a developed product that can contribute to shortening drying time without changing auxiliary driers such as Zr and Ca from conventional cobalt drier.
FIGURE 2–ǀ–Coating after two weeks at 50 ˚C.
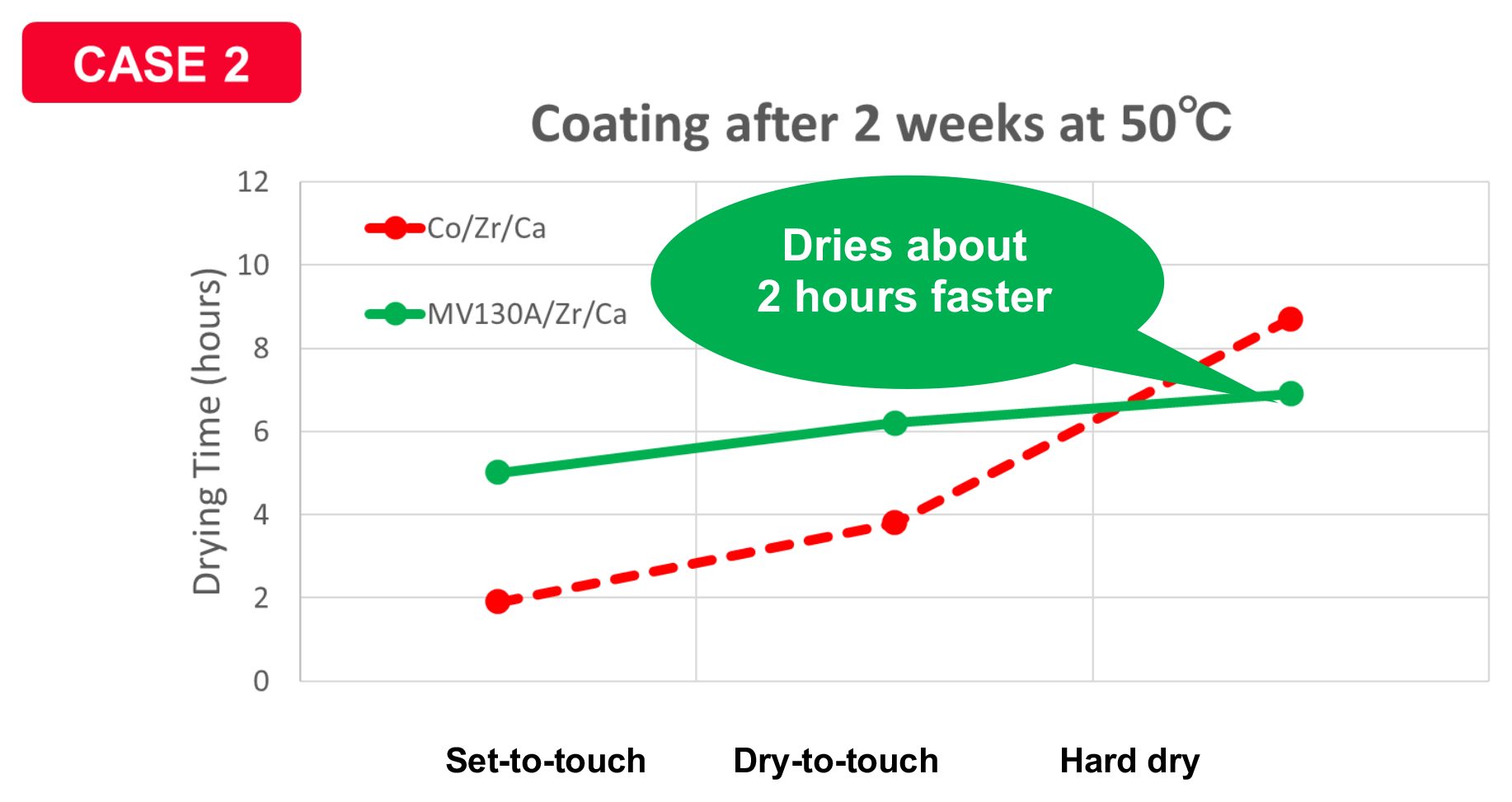
Examination of the Addition Amount
To confirm the drying performance of the developed DICNATE MV130A, the performance was compared with that of conventional cobalt driers. In this study, a conventional blend containing Co/Zr/Ca was used as a standard blend, and MV130A was examined so that the amount of manganese added to the resin in the paint would be 0.01%, 0.02%, and 0.03%. For MV130A, Zr/Ca was also used as an auxiliary drier. As a result, it was confirmed that the best drying performance was obtained when the amount of manganese added to the resin was 0.01%. In particular, it was confirmed that the complete curing time (hard dry time) obtained by the drying recorder test was faster than that using a conventional cobalt drier.
To conclude, DIC has effectively developed cobalt-free and VOC-free driers for coatings and inks. The combination of DICNATE MV130A/Zr/Ca showed better drying performance than conventional Co/Zr/Ca for hard dry time.
To find out more about Sun Chemical’s high-performance additives, click here.