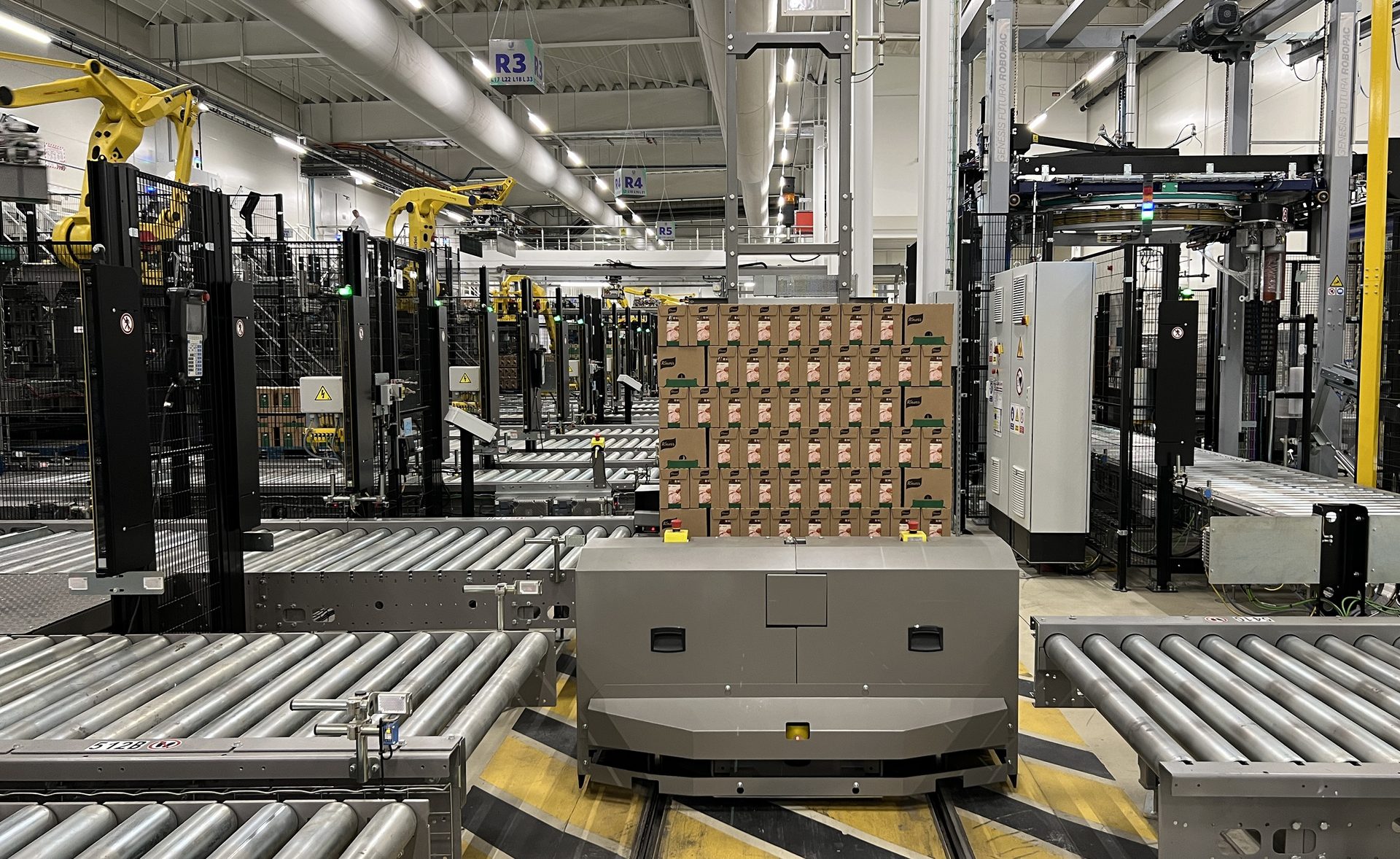
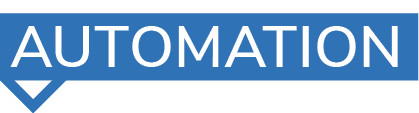
End-of-line Solutions Take Center Stage
Time and again in the course of our reporting on automation and robotics, end-of-line challenges such as palletizing and case forming come to the fore.
By Brad Addington
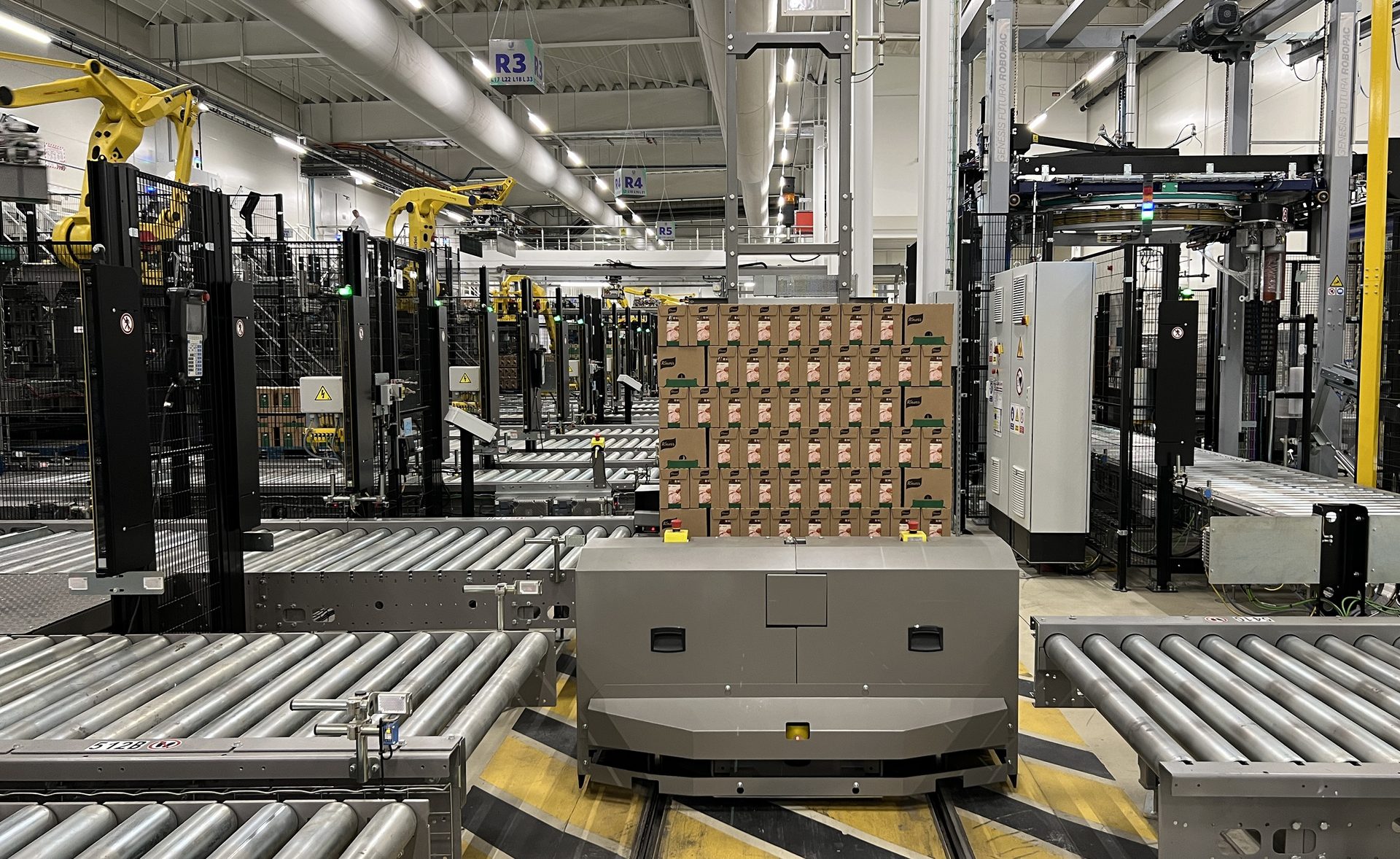
After outgrowing its end-of-line system, Unilever's nutrition factory in Ploiesti, Romania, invested in a new central palletizing solution from Sidel.
Courtesy of Sidel
Automation and robotics play an increasingly important role in the packaging industry. The applications and benefits are literally too numerous to count. That’s why we have decided in this story to shine the spotlight on some specific cases of automation and robotics serving as a game-changer for converters.
One of our favorite stories is that of Unilever’s nutrition factory in Ploiesti, Romania, outgrowing its end-of-line system to manage the breadth of brands packed at the facility. Sidel came to the rescue and installed a centralized palletizing system comprising: eight robotic cells; several hundred meters of case and pallet conveyors; four pallet-handling shuttles; and two stretch wrappers, achieving a production rate of up to 98 pallets an hour.
End-of-line automation has been a common theme in recent months. In February, Ranpak announced the development of Cut’it!™ EVO Multi-Lid, which allows up to four distinct lids to be applied in tandem with the Cut’it!™ EVO machine. This allows the management of multiple branded lid requirements through a single packaging line. We also did a podcast in February in which we talked to Ranpak’s Bryan Boatner about the critical role of end-of-line automation.
Finally, PMMI — The Association for Packaging and Processing Technologies — issued a report in late 2023 noting that labor shortages and e-commerce growth are driving warehouse automation. This insightful report looks at the extent to which CPG companies have turned to automated warehouse solutions. Automated palletizers figure prominently in this report.
Learn more about these exciting new developments in automation and robotics.
Unilever expansion sustained by Sidel’s central robotic palletizing system
Unilever is one of the world’s leading FMCG companies with sales in 190 countries and products used by 3.4 billion people every day. Its nutrition factory in Ploiesti, Romania, manufactures products for one of the company’s most well-known brands, Knorr.
The entire dry nutrition portfolio includes meal makers, dish and sauce bases, and seasonings in various packaging formats — pouches, bags, cartons, and multipacks. These different product lines also handle a large variety of secondary packaging options — American boxes, tray and hood, tray and shrinking foil, and shelf-ready packaging.
Unilever Ploiesti’s production capability has gradually evolved. Volumes have tripled from 12,000 tons per year to 35,000 tons per year; SKUs have risen from 200 to 1,000; packaging lines increased from 14 to 28; and personnel has jumped from 200 to 700.
It was no longer feasible to utilize the factory’s existing end-of-line system to manage the breadth of brands packed on site. Unilever Ploiesti has invested in a new central palletizing solution, fundamentally designed for the continuous production site transformations.
Futureproof robotic palletizing
Sidel installed a centralized palletizing system comprising: eight robotic cells; several hundred meters of case and pallet conveyors; four pallet-handling shuttles; and two stretch wrappers, achieving a production rate of up to 98 pallets an hour. This consolidated system is connected to 28 packing lines.
The robotic cells are divided into two separate clusters — one with five robots, and the other with three. Each cluster has one central pallet magazine for all pallet types and sizes, one induction shuttle for full pallet discharge and one compact shuttle for empty pallet delivery integrated underneath the robotic islands.
According to the capacity of each packing line and the palletizing pattern requested, the cells have three or four product in-feeds, ensuring a robot utilization rate of 92 percent.
READ MORE
Modular build in a compact space
Unilever’s masterplan for the Ploiesti site was to keep the palletization space in a separate area from the packing hall to easily accommodate the recurring packing line modifications. To connect the two areas, Sidel proposed a high-level conveying solution with spiral elevators to save space, facilitate circulation and increase the overall flexibility linked to site transformations.
Iuliana Popescu Colt, Operations Manager at Unilever, comments: “We’ve been impressed by Sidel’s design capability to fit the detailed palletizing specifications we required in a compact area and simultaneously oversee the complexity and high throughput coming from the packing lines.”
Laurentiu Badulescu, Technical Manager at Unilever, said: “This was a complex project. However, the solution developed by Sidel is based on standard proven modules, which have been developed and implemented in other projects. Sidel has combined them in a smart way, to deliver a custom solution, avoiding any complex start-up issues brought by a made-to-order one-shot solution.”
Comprehensive project management
Sidel was able to demonstrate its proposed arrangement using virtual reality glasses, which allowed Unilever to visualize the full installation, check the space constraints and solve potential issues related to platforms, the operators’ access and the raw material flows. Speed simulations also helped to confirm the speed levels and the robot utilization rate.
After the design phase, Sidel’s project management spanned from factory acceptance testing to site installation. All eight robot cells were completed in less than eight months. The modular concept accelerated installation as each cell was commissioned individually and at once integrated into the factory’s live packaging operations.
Badulescu adds: “Spending a little bit more time in design and simulations helped during the installation phase. The virtual model fitted exactly in the physical space, so that we achieved the desired throughput in a very short time.”
Energy savings and integrated digital process
The central palletizing system is integrated in the Unilever digital process. As soon as the operator selects the production order from the packing line, all the information related to the palletization, including pallet size, type of pattern, number of rows/layers, and the label to apply is all automatically set and transmitted to the corresponding palletizing cell and the entire end-of-line setup.
Lucian Tarida, Process Engineer at Unilever, adds: “At Unilever, in every project, we prioritize energy reduction as we’re aiming to achieve a zero-carbon footprint by 2030. By using an energy-saving module for each robotic cell of this palletizing installation from Sidel, we’re able to generate energy from the robotic arm deceleration and re-inject it into the network to be used by other robots or equipment within the line.”
Find out more about Sidel’s palletizing solutions on the Sidel website.
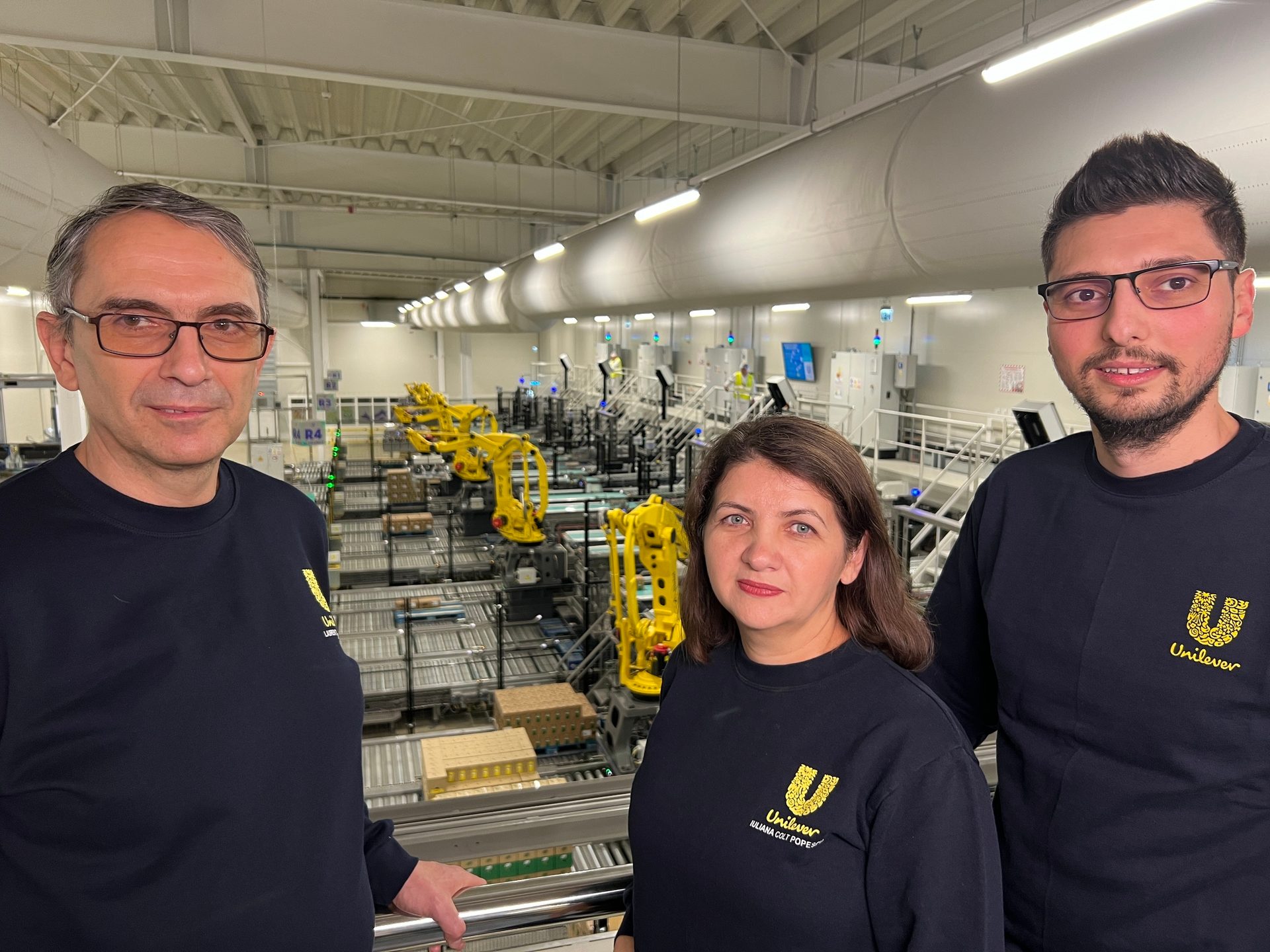
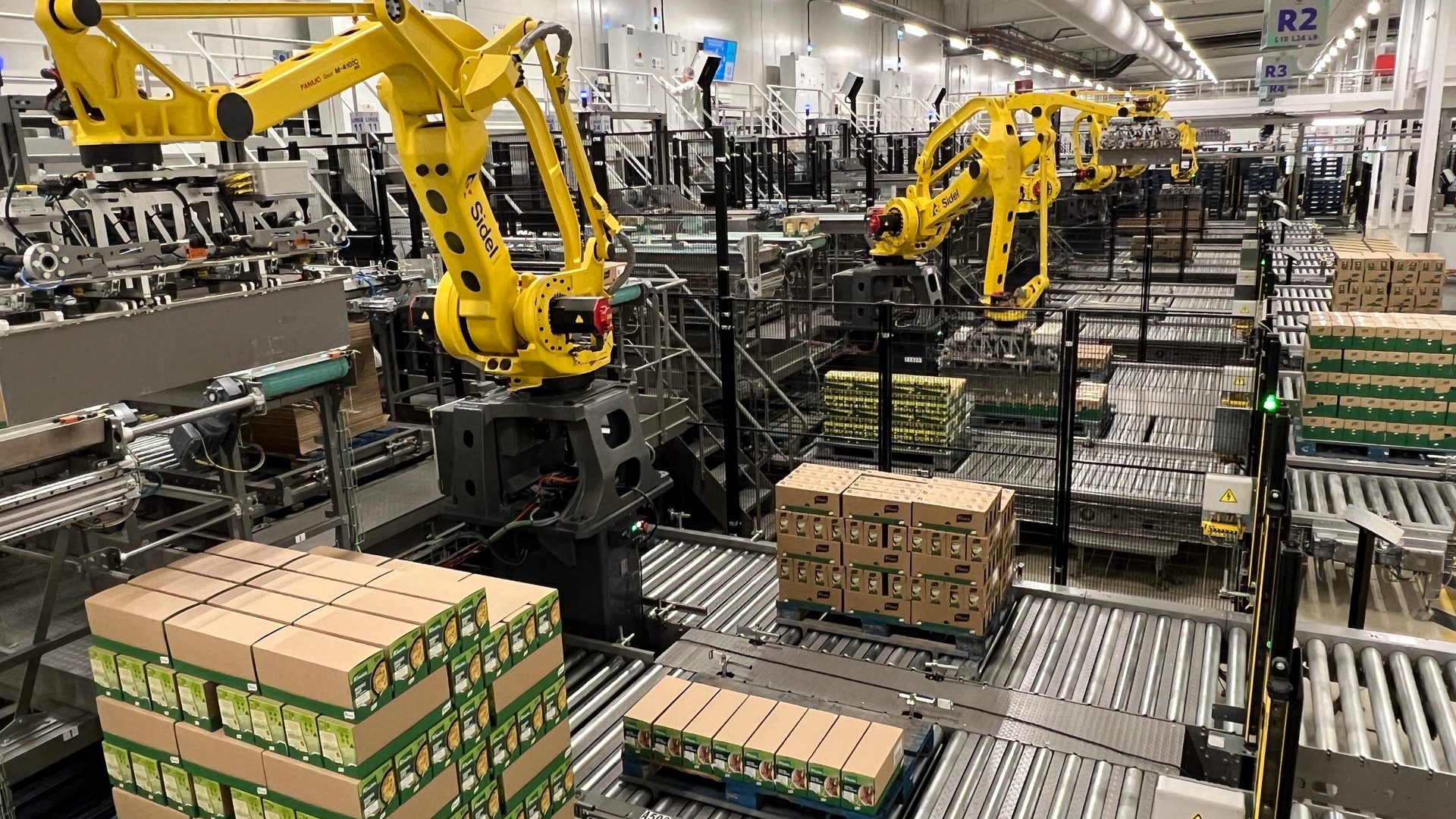
From left to right: Laurentiu Badulescu, Technical Manager, Iuliana Popescu Colt, Operations Manager, and Lucian Tarida, Process Engineer, at Unilever’s nutrition factory in Ploiesti, Romania.
Courtesy of Sidel
After Unilever’s nutrition factory in Ploiesti, Romania, outgrew its end-of-line system, Sidel installed a centralized palletizing system comprising: eight robotic cells; several hundred meters of case and pallet conveyors; four pallet-handling shuttles; and two stretch wrappers.
Courtesy of Sidel
COLLAPSE ARTICLE ABOVE
Ranpak’s Cut’it!™ EVO Multi-Lid allows four unique branded lids on a single machine
Ranpak Holdings Corp., a global leader of environmentally sustainable, paper-based packaging solutions for e-commerce and industrial supply chains, in February announced the development of Cut’it!™ EVO Multi-Lid, a solution that allows up to four distinct lids to be applied via one Cut’it!™ EVO machine, dramatically improving customer experience and managing multiple branded lid requirements through a single packaging line.
Ranpak presented its automated end-of-line (EOL) packaging solutions at LogiMAT 2024, which was held in March at the Stuttgart Trade Fair Centre.
During the show, Ranpak demonstrated its comprehensive portfolio of automated solutions, including the Cut’it!™ EVO in-line packaging machine and the Cut’it!™ EVO Multi-Lid solution. These solutions maximize packaging efficiency for customers, enabling them to achieve their goals related to compliance with the EU Packaging Directive, reaching the 40% void target required by 2030.
READ MORE
Unbox the Future of Packaging with Four Unique Branded Lids on a Single Cut’it! EVO Machine
Ranpak’s Cut’it!™ EVO solution automatically shortens cartons to match their highest point of filling and then glues a lid securely in place. Cut’it!™ EVO delivers unrivaled ROI by enabling labor savings, EOL flow optimization, an enhanced unboxing experience, shipping cost reduction, reduced material usage, and improved stock management. Overall, it assists packaging operations in reducing costs and improving performance and sustainability.
Today, growth in e-commerce is driving more complex warehouse operations, including managing multiple branding requirements. Flexible box branding has become paramount for companies to navigate direct sales alongside B2B activities or providing fulfilment for different brands from one facility. In response to these trends, Ranpak’s Cut’it!™ EVO Multi-Lid emerges as a game-changer.
With up to four unique branded lids available on a single machine, it addresses demand for flexible box branding. This innovative solution allows a single packaging line to efficiently serve multiple customers, optimizing space and future-proofing businesses.
Moreover, Cut’it!™ EVO Multi-Lid enhances the unboxing experience with easy-to-open boxes featuring a tear-off strip. The visually appealing boxes are both strong in construction and tamper evident due to glued lids, which minimizes damage during shipping, leading to fewer returns.
Ranpak’s Cut’it!™ EVO Multi-Lid allows four unique branded lids on a single machine.
Courtesy of Ranpak
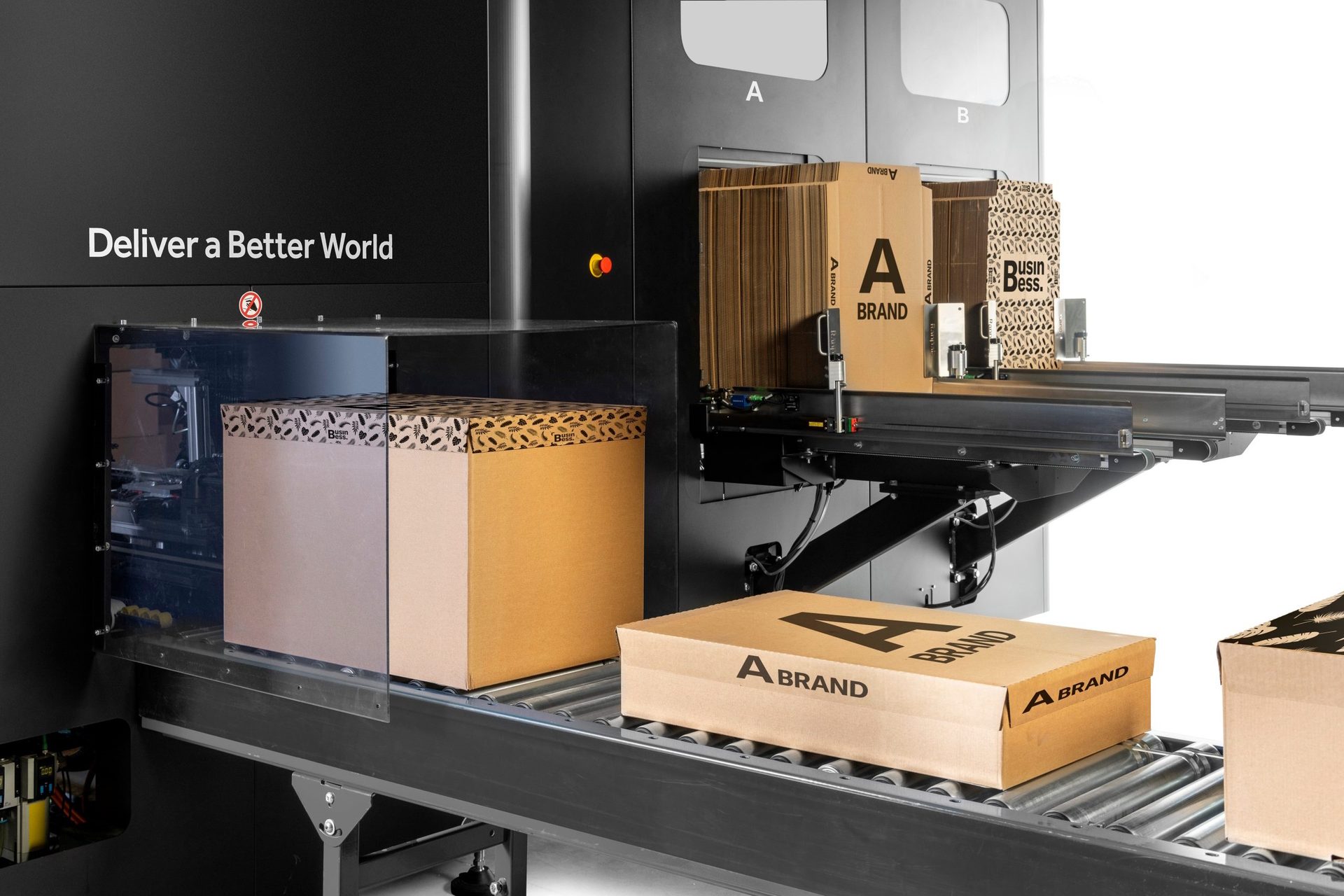
COLLAPSE ARTICLE ABOVE
PMMI Report: Labor Shortages, E-Commerce Growth Are Driving Warehouse Automation
Labor and skills shortages are pushing consumer packaged goods (CPG) companies to invest in warehouse automation solutions, according to the Packaging and Automation in the Warehouses of the Future report produced by PMMI, The Association for Packaging and Processing Technologies.
Additionally, growing e-commerce activity and rising direct-to-consumer demands mean many CPG firms are seeing their warehousing and fulfillment operations become more complex, increasing the demand for mixed and layered pallets.
READ MORE
With these new trends, CPG companies are turning to warehouse automation solutions such as palletizers and mobile robots, according to the PMMI report. More than one in four (25%) warehouses will have some form of automation installed by 2027, leaping from just 14% in 2017 and 18% at the end of 2021. The PMMI survey shows that less than 20% of CPG firms operate mostly automated warehouses today, and very few report they are fully automated.
As highlighted in another PMMI report — 2022's The Future of Automation in Packaging and Processing — the most immediate challenge in 2022 was the lack of available labor. For some companies, it was a case of automating the line or stopping production. CPG firms are starting to realize that a piecemeal approach to automation can be effective. Companies are increasingly demanding flexibility from their operations and the ability to alter output from production lines to meet fluctuating levels of demand.
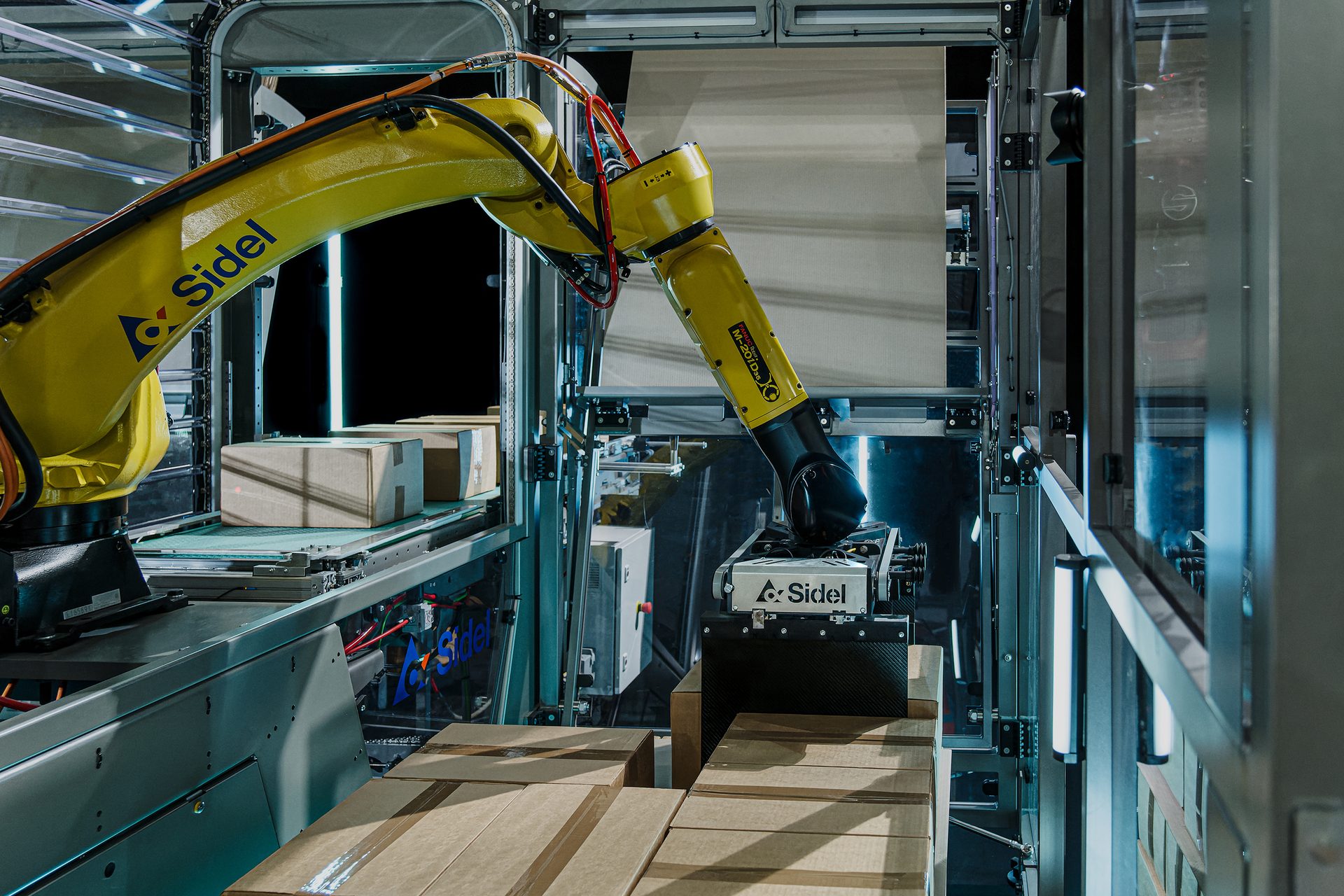
PMMI reports that CPG companies are turning to warehouse automation solutions. Sidel’s compact palletizing unit combining robotics and cobotics — the RoboAccess_Pal S — embeds three new patented features to provide an even higher level of agility, operability and compactness.
Courtesy of Sidel
COLLAPSE ARTICLE ABOVE
Nm
No
READ MORE
Th
