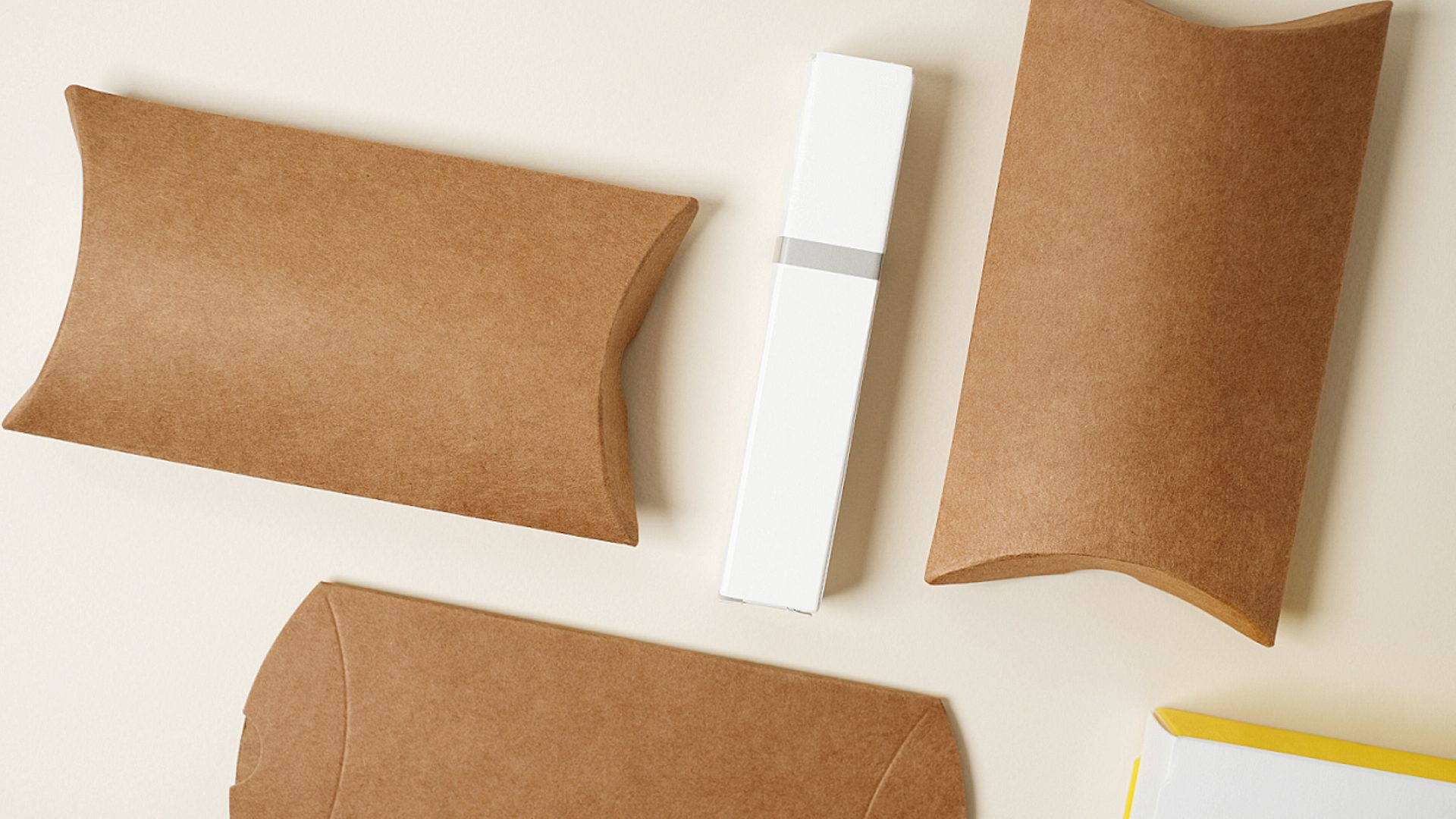
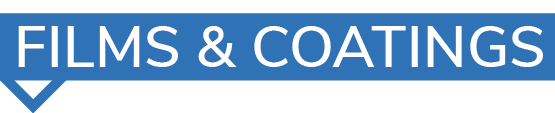
SUSTAINABILITY TAKES CENTER STAGE
Read about some key sustainability developments regarding films and coatings.
By Bobby Douglas
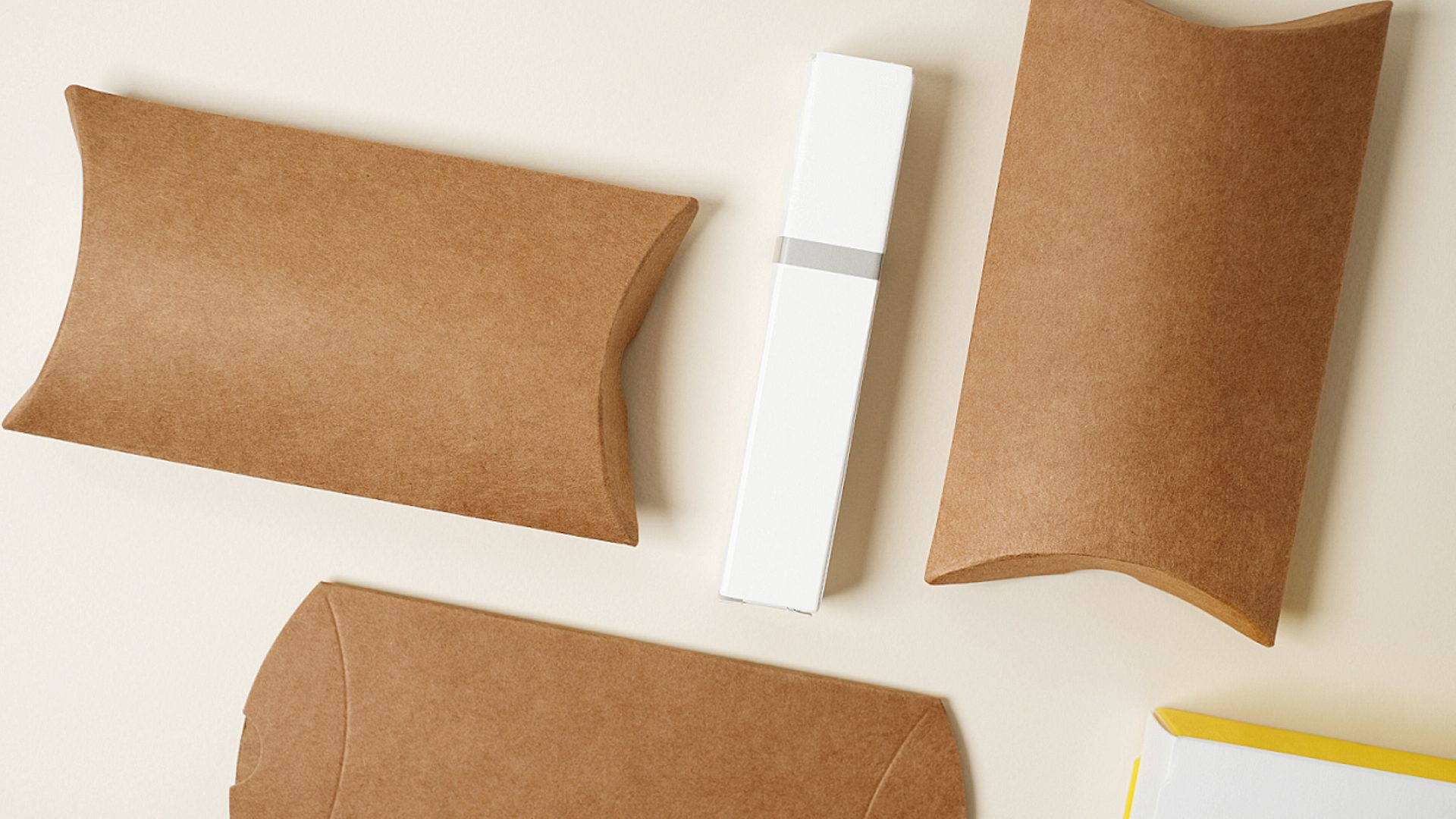
Sustainability has become a key issue when it comes to films and coatings.
Courtesy of Xampla
When it comes to films and coatings in the packaging industry, sustainability has been a key factor as of late. With national governments across the world calling for environmentally friendly packaging and consumers sharing similar attitudes, packaging manufacturers have been tasked with designing films and coatings that are not only functional, but also sustainable.
Companies have tackled this challenge in a variety of ways. First, Huhtamaki reached a significant multi-year deal with 2M Group of Companies to use Xampla’s plastic-free Morro™ coating for its takeaway boxes, allowing for the replacement of traditional and less sustainable barrier coatings.
On the materials side, Mondi and traceless partnered to develop a new coating solution made from agricultural by-products, which led to significant greenhouse gas savings compared to traditionally used plastic.
Finally, Paramelt brought two unique coating solutions to the table with Paraflex Nowax, which is on par with polyethylene barriers despite being made from biodegradable materials, and Aquaseal, which is a fully recyclable, water-based coating.
Learn more about these developments below:
Huhtamaki Reaches Deal to Use Xampla's Morro™ Coating Polymer for Takeaway Boxes
Huhtamaki and 2M Group of Companies have announced the first ever multi-year supply deal to deploy Xampla’s plastic-free Morro™ Coating polymer to replace traditional barrier coatings in a range of takeaway boxes.
The deal between Huhtamaki and 2M Group of Companies will see Morro™ Coating deployed at scale in selected foodservice on-the-go applications, enhancing Huhtamaki’s wider use of alternative recyclable and compostable packaging solutions derived from renewable sources.
Huhtamaki’s UK manufacturing facilities supply innovative packaging solutions to leading global Quick Service Restaurants, Specialty Coffees and catering brands.
READ MORE
Developed by Cambridge based deep-tech company Xampla, Morro™ Coating is an alternative to both renewable and fossil-derived plastic coatings. Made from plant protein, the material is food contact safe and delivers excellent grease, water and oxygen barrier performance as well as heat-seal ability.
Classified as a natural polymer, Morro™ Coating is completely free from both Per- and Polyfluorinated Substances (PFAS), known as ‘forever chemicals’, and plastic. The material is exempt from the Single Use Plastic Directive.
A completely natural material, it can be used on a variety of substrates and tailored for use across many food packaging applications.
Mottie Kessler OBE, Chair and CEO of the 2M Group of Companies said, “The 2M Group of Companies are committed to promoting sustainable solutions using innovation in science and manufacturing. We are proud to be working with Huhtamaki, one of the leading packaging manufacturers in the world and Xampla to deliver alternatives to plastic packaging, which help create a better future for our planet”
Andy Hesp, General Manager Huhtamaki UK & Ireland, said: “At Huhtamaki, our ambition and values to lead the way in sustainable food packaging are clear. Packaging enhances food security and makes everyday necessities more hygienic, more accessible and more affordable. The adoption of Xampla’s technology on some of our core food service solutions further contributes towards our drive to protect food, people and the planet."
Xampla's landmark partnership with the 2M Group of Companies was announced last year and this exciting milestone represents significant progress on the commercialization of Morro™ technology.
The 2M Group of Companies and Xampla were successfully awarded an Innovate UK SMART grant to scale-up the manufacture, supply and distribution of Morro™ Coating to multiple tonnes per day. 2M also recently launched its own sustainable packaging business.
The deal will give Huhtamaki exclusivity on use of the coating in food service containers made from fluted corrugate board. 2M Group of Companies is looking to agree further partnerships for other applications of Xampla technology.
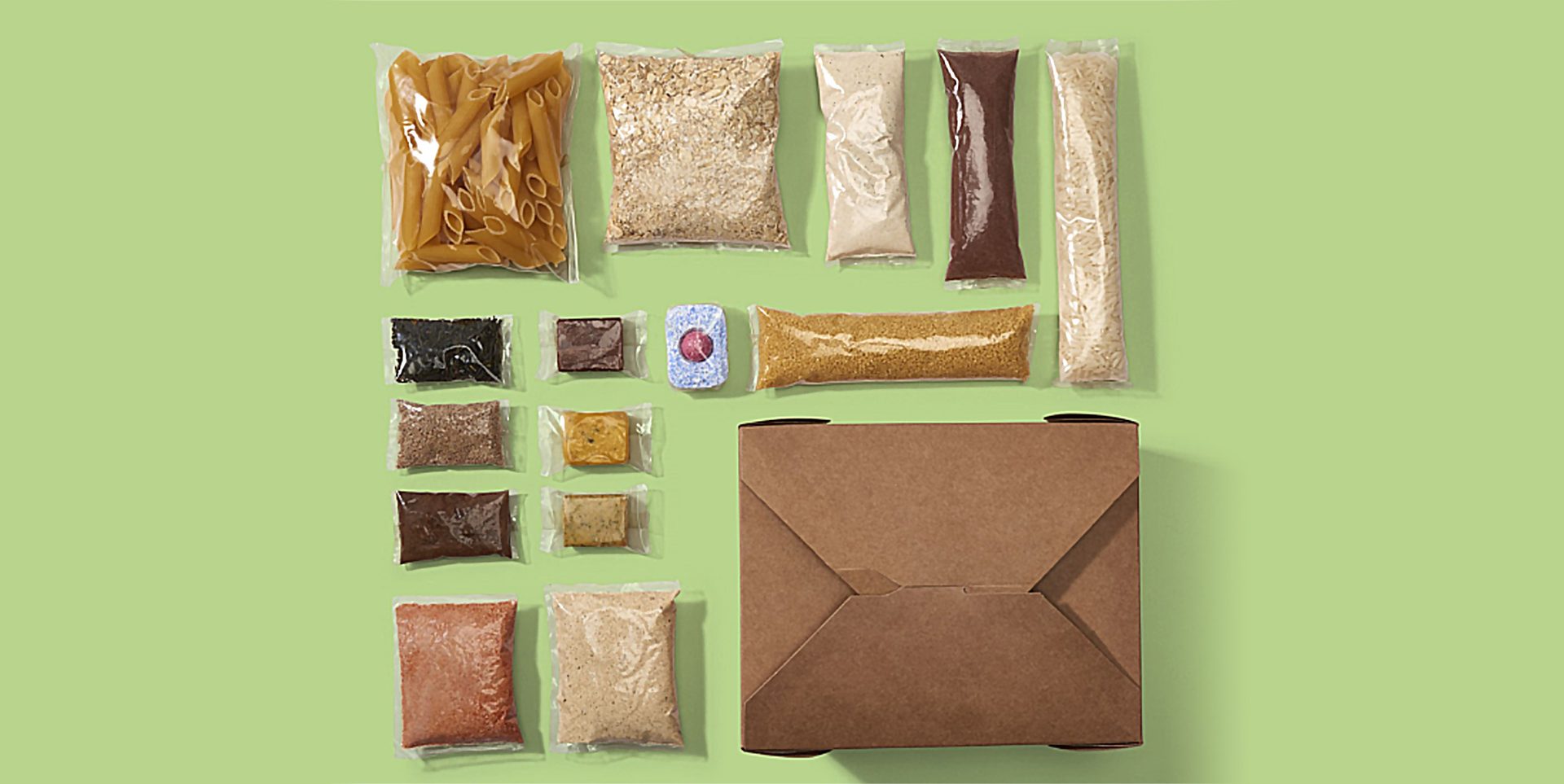
The deal allows Huhtamaki to enhance its use of environmentally friendly packaging solutions.
Courtesy of Xampla
COLLAPSE ARTICLE ABOVE
Mondi and Traceless Develop new Coating Solution Made from Agricultural By-products
Mondi, a global leader in sustainable packaging and paper, is partnering with advanced biomaterial engineers traceless to develop a new coating solution based on by-products from the agricultural industry. This innovative bio-circular coating solution is the first of its kind and will be able to replace traditionally used plastic coating.
There is an increasing demand for plastic alternatives in packaging solutions, and this new coating will respond to the demand directly: made from renewable plant-based materials, namely residues from the agricultural industry, it eliminates the need for fossil raw materials. traceless' consequential life-cycle assessment showed that the provision of traceless® material to the market leads to overall greenhouse gas savings of 76% from sourcing to disposal, if the material is used as a replacement for virgin PET. If only the production and disposal phase is considered, these savings add up to 95%. Also, the material is certified home compostable by DIN CERTCO according to NF T51-800.
READ MORE
The joint work of Mondi and traceless on this product started in 2021 and brought world-leading expertise together: Mondi’s knowledge in paper coating and packaging solutions, and traceless’ expertise for material solutions based on natural polymers. The coating granulates are produced in traceless' pilot plant and are applied to Mondi's kraft paper in Mondi's R&D centre for further testing of the coated paper in the company’s laboratories. Later production on industrial scale will take place in a designated plant in Hamburg.
Varying products require different barriers in their packaging and the coated kraft paper solution is tested thoroughly for different packaging purposes, to ensure it can be used across different end-markets: the in-depth trials have confirmed that kraft paper coated with traceless® can resist water, oxygen and fat, while offering good printing abilities for different customers. At the same time, the goal is to develop a solution that is also recyclable in existing recycling streams throughout Europe. Currently, the properties of the bio-based coating are further optimized, fine-tuning the solution to make it fit for different packaging applications for various end-markets such as eCommerce, frozen food, fatty and non-fatty food. The goal is to achieve a packaging solution which can be scaled for a range of different industries and significantly reducing the greenhouse gas emissions throughout the packaging life cycle.
Marko Schuster, COO Functional Paper and Films at Mondi, says: “We are always looking at what the next steps are in creating truly circular packaging, following our customers’ demands as well as our own innovative spirit. This is a fantastic example of how we can combine our R&D forces to be one step ahead in the sustainable packaging game, contributing to a circular economy.”
Anne Lamp, CEO and co-founder traceless adds: “Our mission is to make pollution and waste history by using materials that impact positively. The journey so far has been exciting and insightful, teaching us valuable lessons to ensure our packaging delivers excellent protection. By working with Mondi — its team, its machines and its products and processes — we are adapting our existing expertise in innovative biomaterials to reduce plastic barrier coatings in packaging. The goal is to create a truly fit-for-purpose product that works for as wide a range of applications and industries as possible.”
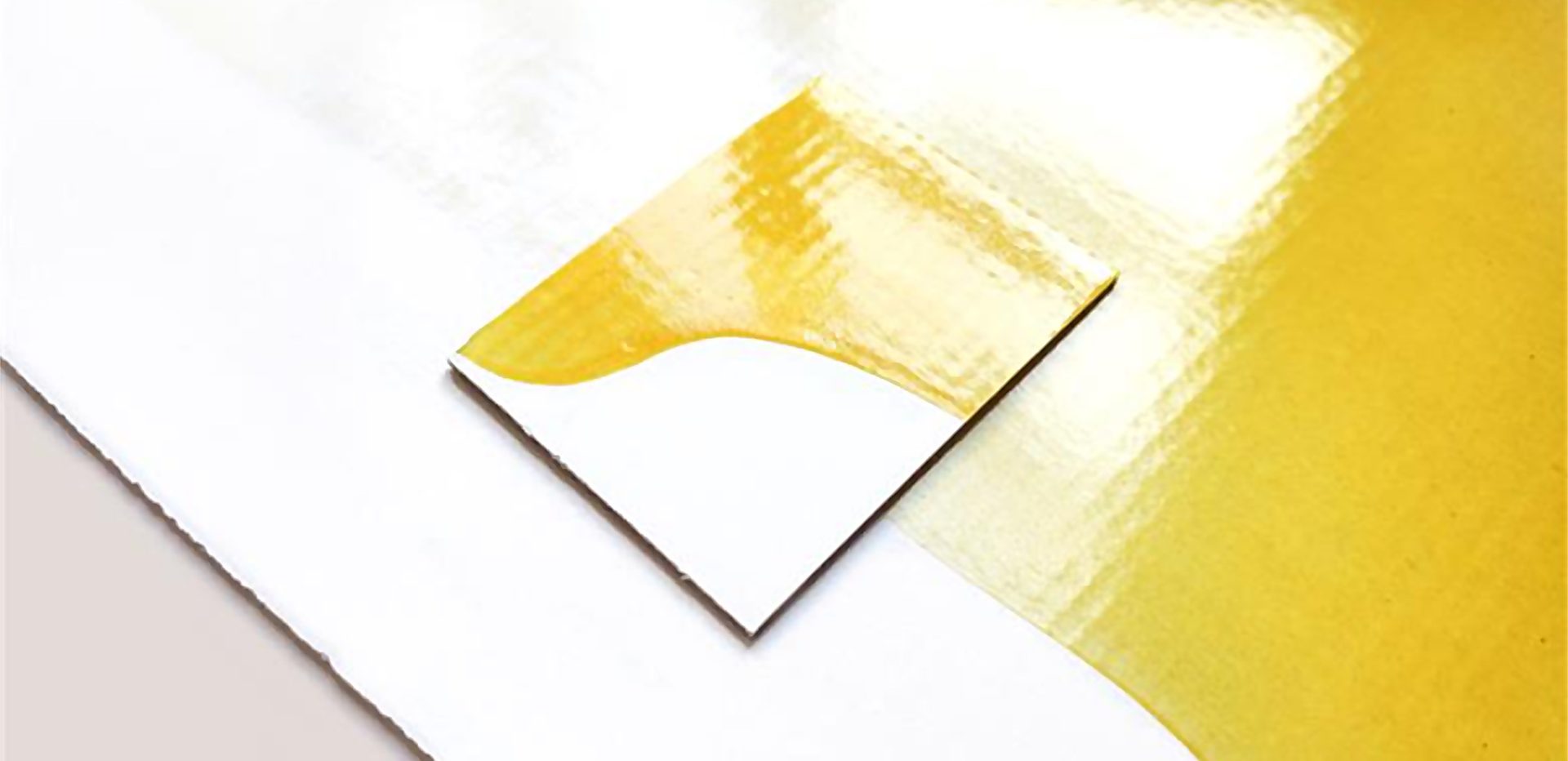
The bio-circular coating will be able to replace traditionally used plastic coating.
Courtesy of Mondi Group
COLLAPSE ARTICLE ABOVE
Paramelt Coatings Help Reduce Environmental Impact of Packaging Material
When designing packaging in today’s context of the circular economy, not only the mere functionality of the packaging, but also the environmental impact has to be considered. Sourcing and end-of-life scenarios for the packaging material have become decisive criteria.
This has led to renewed interest in paper-based packaging. In combination with suitable coatings, they can offer the required barrier and heat-seal functionality needed for many packaging applications.
Paramelt provides two key platforms enabling the creation of high-performance packaging papers while maintaining the benefits of this highly attractive substrate:
READ MORE
1. Paraflex Nowax — renewable vegetable-based coatings
Paper functionalized with the company’s Paraflex Nowax coatings yields barriers equivalent to polyethylene while remaining inherently biodegradable. Paramelt coatings are applied in the same way as wax coatings and can be used in a wide range of packaging applications. They offer a solution for all “end of life” scenarios, be that landfill, littering, recycling or composting.
Paramelt has now certified its Paraflex Nowax range under EN 13432 Home and Industrial compostability.
When combined with equally certified papers and inks, Paramelt’s targeted customers (converters) can hence speed up approval processes of their final packaging materials.
2. Aquaseal — waterbased polyolefin dispersions of conventional extrusion-grade plastics
Although 10-12 gram of plastic per square meter of paper is often enough to achieve heat-seal and barrier performance, it is difficult to consistently apply such thin layers with extrusion techniques. A thinner, water-based coating, which can be applied using conventional coating and printing techniques, will inherently yield a lower overall MVTR, but this is frequently sufficient for the target application. The heat-seal functionality remains, but more importantly, the packaging material remains fully repulpable and recyclable via existing waste streams using appropriate processes.
In addition to the recyclable polyolefin-based coatings that Paramelt has offered for several years already, the company is now introducing a range of compostable polyester dispersions, both biobased as well as synthetic.
This new range offers converters the possibility to create fully recyclable and compostable paper-based packaging structures.
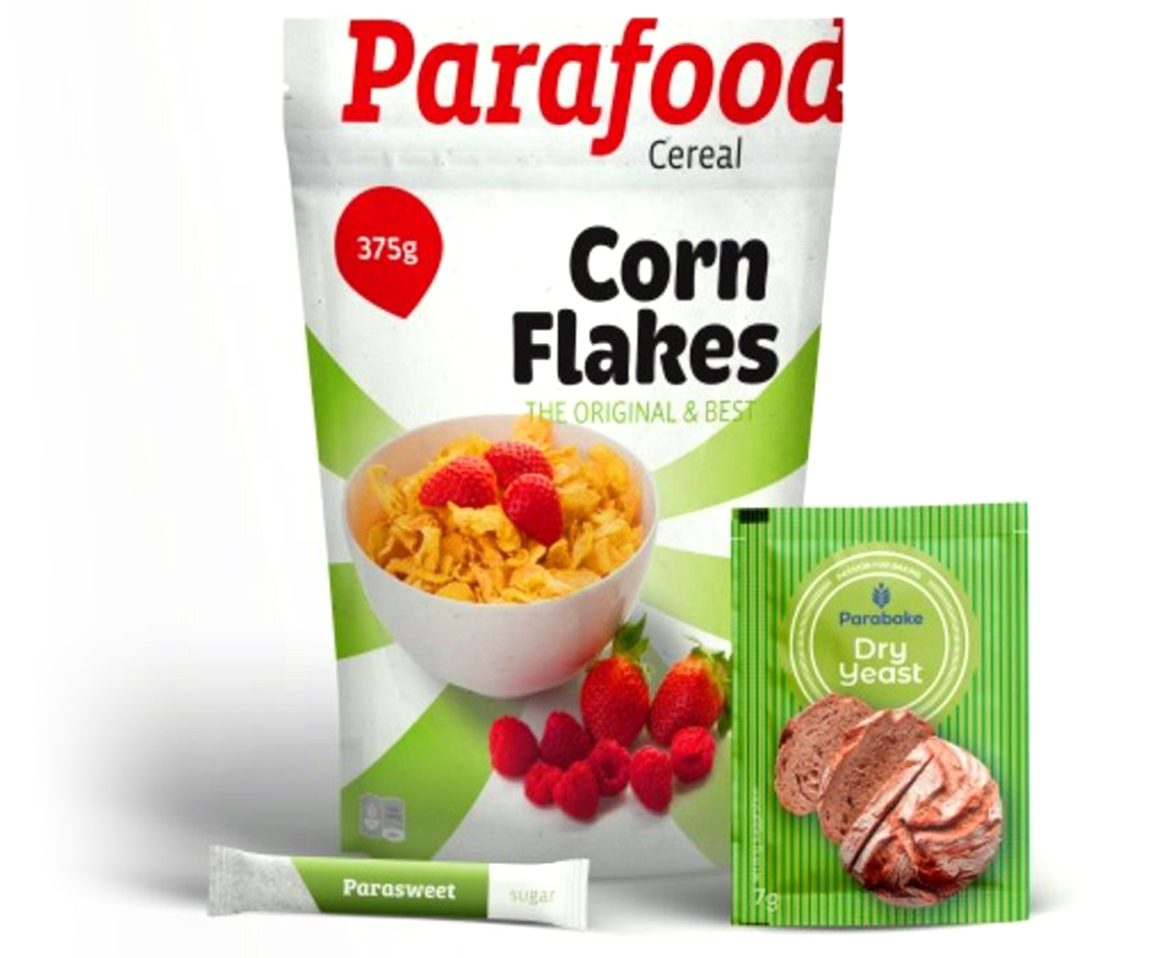