H2 Deck By Bold Name
h2 xxxxxx
H1 xxxxxx
h2 xxxxx
Measurement
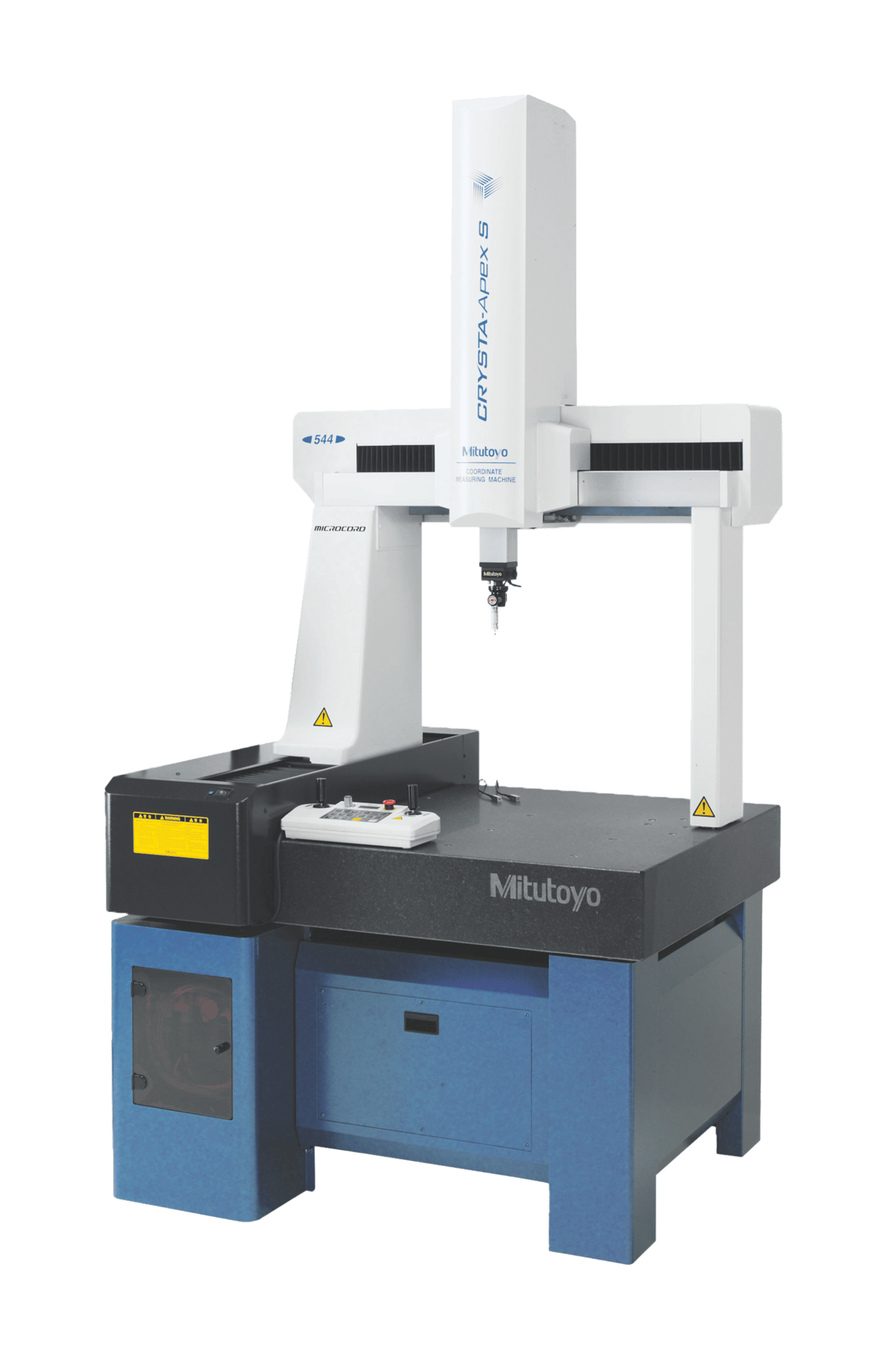
The integration of 3D CAD models and advanced software algorithms are setting new standards for accuracy and efficiency in manufacturing. By Genevieve Diesing
Precision Trends in
Metrology
Measurement
H2 Deck Info By Paragraph Style Bold
Headline
Metrology is becoming more integrated, efficient, and predictive. Manufacturers are increasingly embedding measurement processes within production, using advanced data analytics, and using more sophisticated software to automate maintenance. Here are four ways these changes are taking shape:
1.Continuous Monitoring Over Final Inspection
Quality departments are shifting toward measuring directly within production, experts say. Production floor measuring near-line and in-line is becoming the norm, along with metrology equipment monitoring for equipment maintenance and equipment workload versus idle time, says Gene Hancz, CMM product manager, Mitutoyo America Corp.
This approach not only streamlines the manufacturing process but also ensures that equipment is better utilized and maintained.
Dan Skulan, general manager, industrial metrology, Renishaw, highlights the move away from traditional end-of-line inspections. He explains, “There has been a significant shift in the reliance on final inspection, or as we call it ‘tailgate inspection.’” Skulan notes the inefficiency of detecting issues only at the final stage, advocating for “incorporating accurate, actionable data upstream in a manufacturing process.”
2. Comprehensive Solutions on the Rise
Demand for interoperability across various measurement tools and platforms is growing. “More customers ask for a single software interface, crossing multiple hardware platforms, through which multiple sensors can be used to measure and analyze more products,” says David Wick, manager of product management, ZEISS Industrial Quality Solutions.
A growing number of clients want to work with a vendor who can “define, integrate and support a full solution, not just a CMM,” he adds.
OEM services are expanding to support these trends, including “turnkey metrology solutions, contract programming/inspection, service agreements, training and re-training resources, [and] metrology education classes (online and on-site, in classroom),” Hancz adds.
3. AI Drives Predictive Maintenance
Predictive maintenance powered by AI analytics anticipates potential problems before they escalate into equipment failures or, at worst, cause severe quality issues due to compromised measurement data, Hancz says. This can prevent product failures and resulting analytics can help to automate routine maintenance, minimizing production interruptions.
Skulan says AI is akin to “rapid research,” with its outputs heavily reliant on the quality of input data. In manufacturing, where decisions must be based on factual, traceable information, accuracy and reliability of measurement data are very important, and so a quality traceable CMM can help teams improve performance and maintain quality control.
Because predictive maintenance provides customers with forecasts of when their CMMs will require calibration or service—based on operational factors such as run time hours, time since the last calibration, or the distance the probe head has moved — they can calibrate the CMM according to manufacturer specifications.
4.Algorithmic Advancements Impact Accuracy
Software and algorithm advancements are impacting metrology. By automating part programming, integrating comprehensive product information, and reducing program run times, manufacturers are seeing more accuracy and efficiency in quality control.
Manufacturers are increasingly integrating Product Manufacturing Information (PMI) into the measurement process. “Advanced software that can create measurement programs directly from models... ensures that the correct features are being inspected,” Skulan notes. This approach minimizes human error and optimizes the inspection process at various stages of production, identifying and isolating controllable processes through pattern detection.
The use of 3D CAD models streamlines the inspection plan process and helps teams to apply necessary PMI accurately and consistently, which can make CMM measurements more accurate and complete, experts say. Hancz says that leveraging 3D CAD models for fully automated part programming “ensures the most efficient in the least amount of time required for a complete measurement plan.”
These developments are also providing efficiency gains. “Advancements in software algorithms improve customer efficiency by reducing measurement program run time,” Wick says. The optimization of software, sensors, computers, and the CMM frame boosts the accuracy of measurements, he says.
IoT’s real-time analytics and in-process control are making operations more precise and products more reliable. By Genevieve Diesing
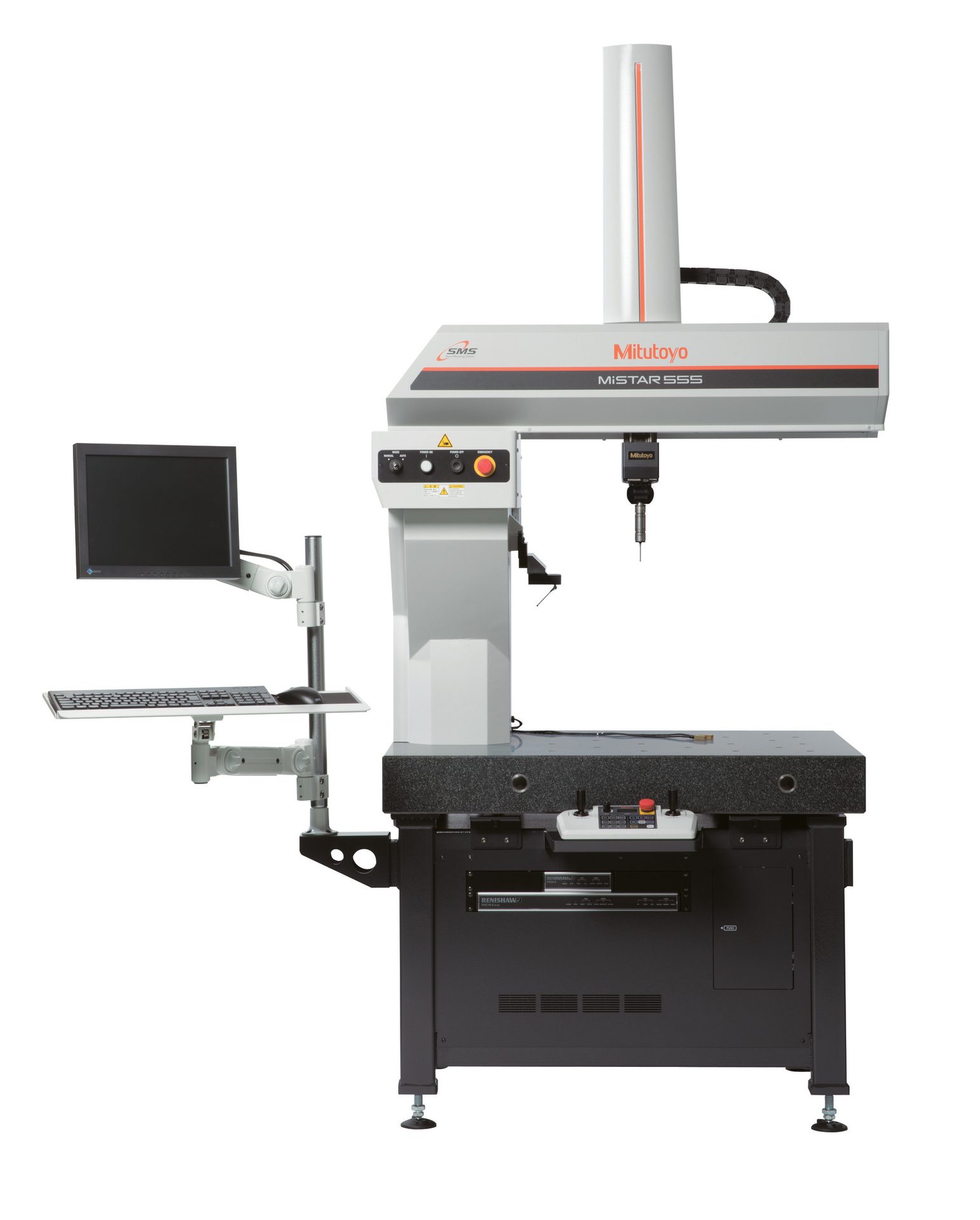
How IoT Integration Enhances Quality and Speed
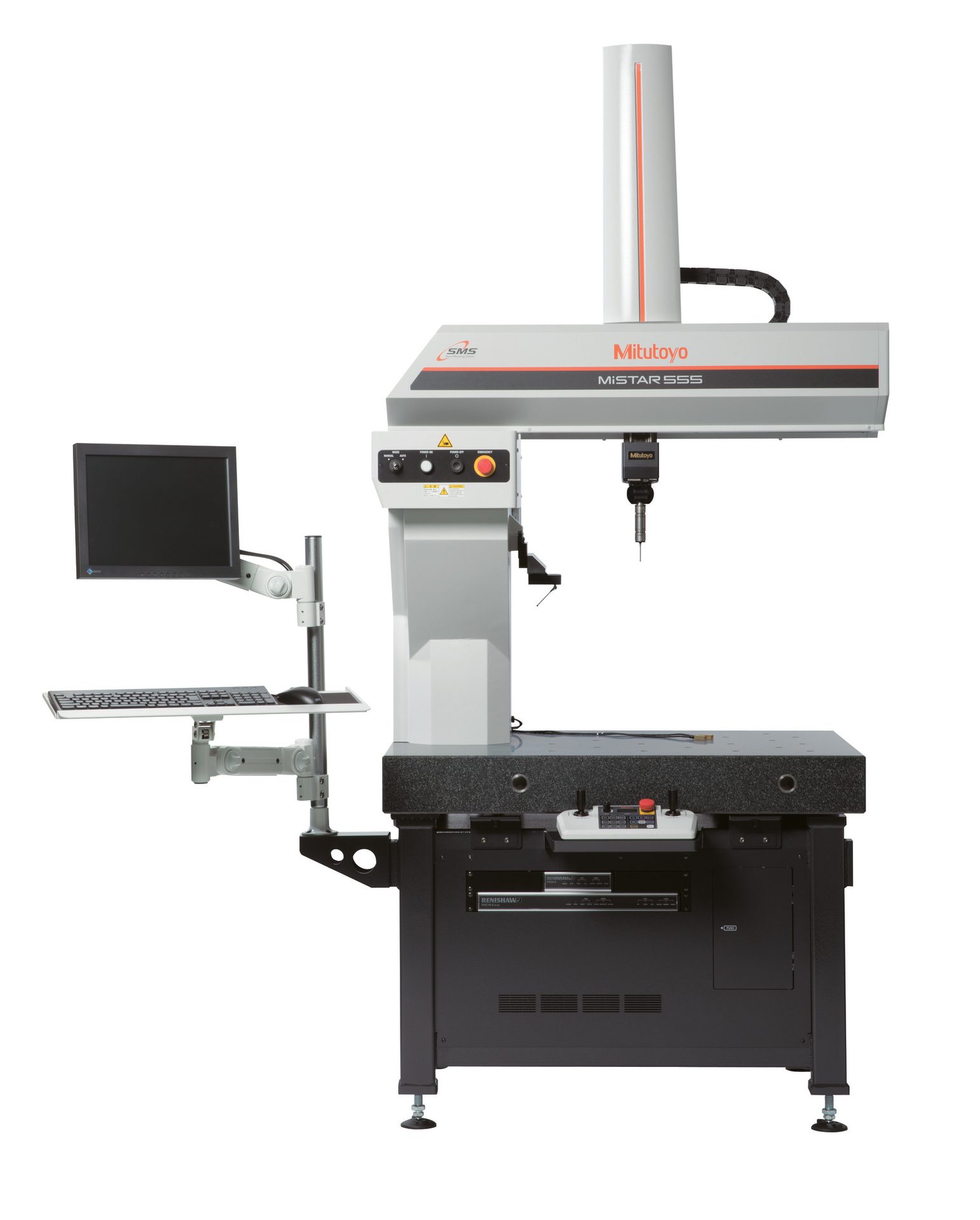
How IoT Integration Enhances Quality and Speed
In plain language, Internet of Things (IoT) integration is the process of connecting sensors and objects with one another—and with applications and databases, says David Wick, manager of product management, ZEISS Industrial Quality Solutions.
CMMs are already benefiting from IoT through the integration of multiple plug-and-play tactile and noncontact sensors with metrology software and measurement databases, says Wick. This integration helps sensors and objects communicate directly with applications and databases.
When coordinate measuring machines (CMMs) enter the picture, manufacturers can improve product quality and manufacturing speed. This combination helps sensors to collect and report real-time data, significantly reducing machine downtime and the production of out-of-spec products.
Closing Skills Gaps and Reducing Downtime
As the manufacturing sector faces staff shortages, this integration allows for automated adjustments to machine tools if they trend towards producing out-of-tolerance parts, thereby reducing scrap and rework.
“With shortages of skilled labor and resources—and as the Internet of Things (IoT) brings increased connectivity — manufacturers are seeking a more streamlined and speedier measurement process, one that eliminates the need to move parts away from the production line for verification,” says Gene Hancz, CMM product manager, Mitutoyo America Corp.
Information Automation
Dan Skulan, general manager, industrial metrology, Renishaw, says that “information automation”—where IoT boosts communication between devices—ensures that measurement data lands directly within the production machinery, increasing overall speed and accuracy.
“IoT has increased the ability of all devices in a manufacturing environment to communicate with each other more effectively... eliminating the delays and possible loss of context that happens with human transfer of information,” says Skulan.
Real-Time… and Ahead of Time
With the advent of IoT and AI, along with analytical information, there’s a marked improvement in flexibility and overall product quality, experts say. The ability to monitor CMM usage and maintenance needs in real-time also makes CMMs more reliable.
Real-time data collection also offers broader organizational benefits, experts say.
“The key advantage is that a customer can see if specific steps in their production process are yielding a part within the desired specification, right now,” Wick says. This immediate feedback loop enables manufacturers to make necessary adjustments on the fly, minimizing scrap costs and development time. Wick also points out the strategic advantage in larger organizations, where real-time data collection facilitates the comparison of measurement results across machines or even across global plants, thereby “accelerating quality improvement across the organization.”
Real-time data and analysis keep production standards high, as they allow for immediate corrections. Experts say that artificial intelligence (AI) takes this a step further, predicting potential issues and giving teams a chance to address them before they escalate.
“Real-time analytics with the aid of AI can identify trends that can predict an out of tolerance state before they happen, prompting immediate attention,” Hancz says. This significantly reduces the risk of producing out-of-specification parts.
In-Process Control and On-Machine Measurement
Real-time information conversion into actionable steps, otherwise known as in-process control, also boosts quality.
“Real-time information can quickly be converted to action that can be taken with minimal parts being run while you wait,” Skulan explains. Teams can use near-machine CMMs or gaging systems to facilitate in-process control, often integrating CMM-type measurements directly on CNC machines. This strategy enables teams to measure parts before machining, so they are produced correctly.
All Images Source: Mitutoyo
Genevieve Diesing is a contributing editor to Quality.
LINKS TO PAST COLUMNS:
Listen to a past podcast with the author: