H2 Deck By Bold Name
h2 xxxxxx
H1 xxxxxx
h2 xxxxx
Test & INspection
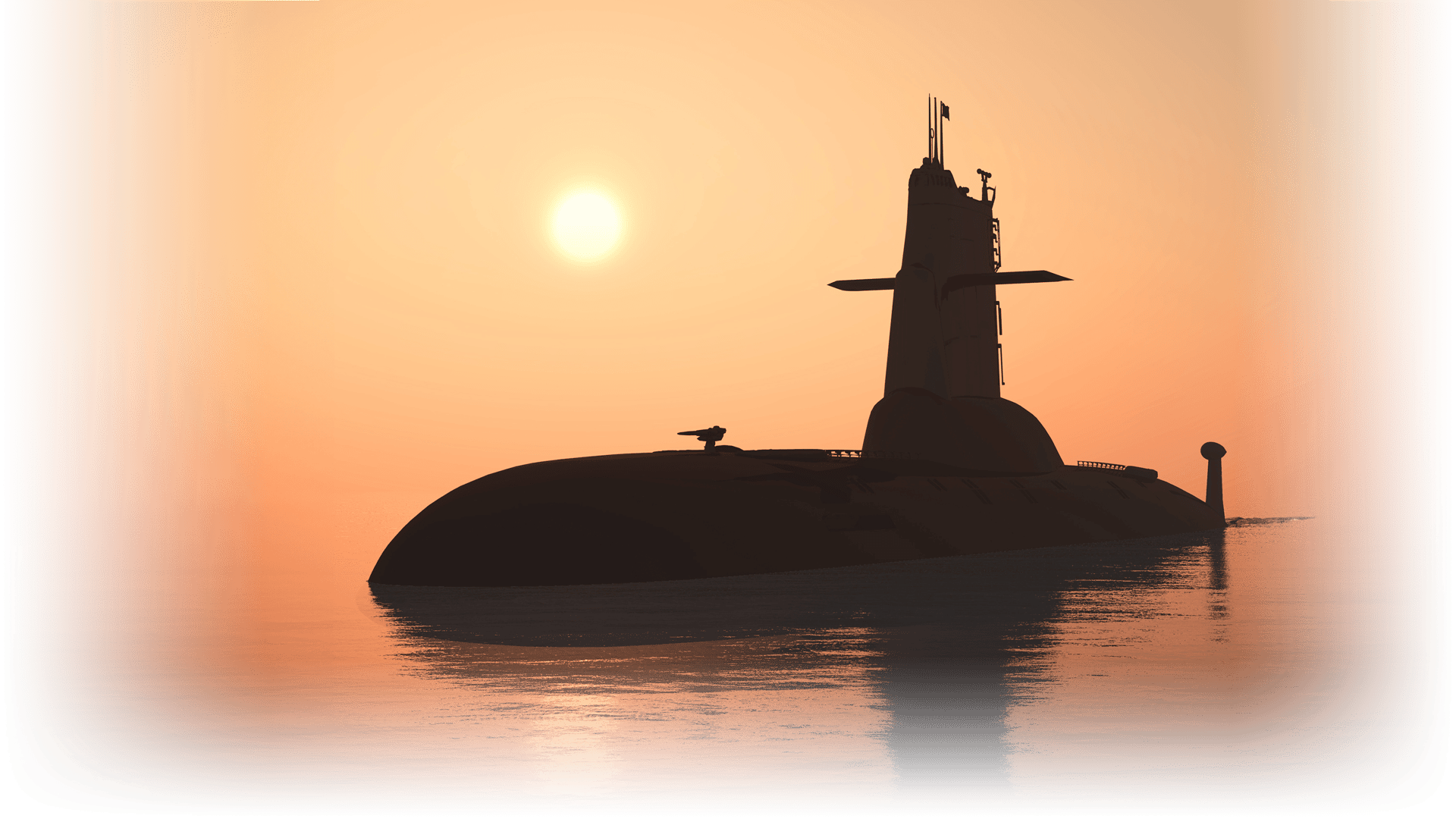
My training as a nondestructive testing inspector started with mentors that were NDT inspectors during the USS Thresher’s shipyard work. By Joseph Sorrentino
The Importance of
Quality Assurance and Safety
Test & INspection
H2 Deck Info By Paragraph Style Bold
Headline
My career in quality assurance and configuration management started in 1963.
On April 10, 1963, the USS Thresher SSN 593 (after completing shipyard work), submerged for its sea trials. Tragically, 112 Naval Personnel and 17 Civilians plunged to their death.
The USS Thresher was known as the Thresher-Class, a deep diving fast attack nuclear submarine that was a significant improvement over the Skipjack-Class Navy nuclear submarines. Skipjack class were a class of nuclear submarines (SSNs) that entered service in 1959-61. This new class introduced the teardrop hull and the S5W reactor to U.S. nuclear submarines. The Skipjacks were the fastest U.S. nuclear submarines until the Los Angeles-class submarines were the first of which entered service in 1974.
The shipyard work done on the USS Thresher was performed with one major job on the Auxiliary Saltwater system (ASW System). The Thresher had 3,000 silver-brazed joint exposed to full submergence pressure. During this shipyard maintenance period, 145 of these joints were inspected with a new technique called ultrasonic inspection. Fourteen percent of the joints tested had sub-standard joint integrity. This inspection disclosed many joints not meeting the acceptance criteria of 70% bonding between the pipe to fitting. The piping system had rejection reports for each failed joint by way of ultrasonic inspections.
The ASW piping was in the machinery space which held electronic panels controlling various submarine systems. The reject inspection reports were submitted, but a high-ranking officer released the USS Thresher for sea trials ignoring these reports. Sea trials required that all tests and inspections assured that the submarine was seaworthy before it could return on patrol duties. This initial test dive should have been performed in Non-Crush Depth Waters, it was not. This was a big mistake. When the submarine conducted its test dive systems it failed and the USS Thresher was lost.
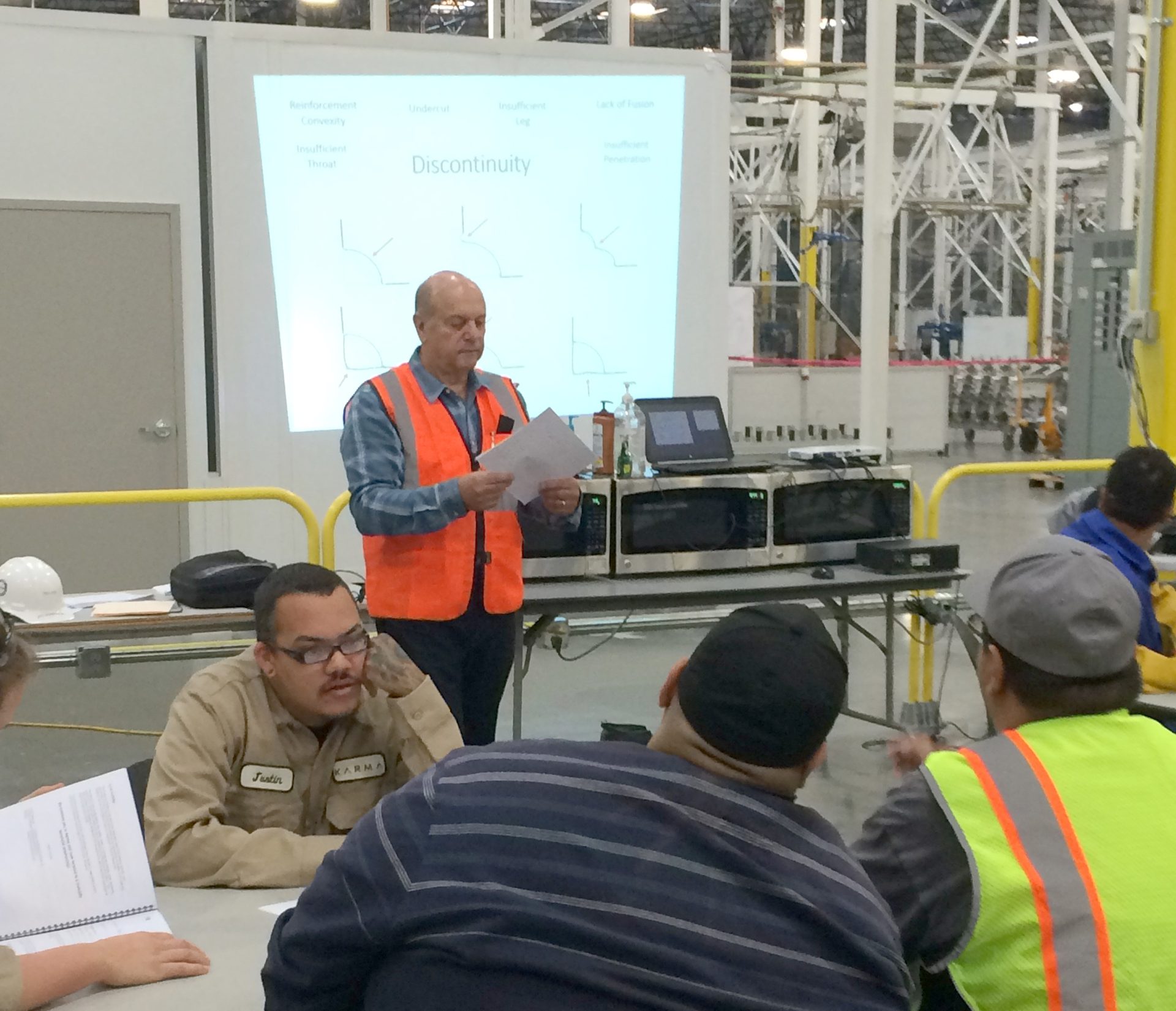
Caption
Why am I telling you this story? The final testing and validation of the design is where the drawings, standards, specifications, inspection requirements and acceptance requirements are established. The control over all of these is called configuration management. The liability of who is responsible for all of this is the person approving the design and requirements on each drawing. Remember, each component part and the system was tested until failure. The safety factor was applied and this established what can and cannot be changed. All the defined requirements MUST COMPLY to all the engineering drawings, standards, specifications, inspection requirements, and acceptance requirements. All were established by the verification and validation of testing. If you do not comply with the established requirements, you may be liable. It could identify your own actions as breaking the law and possibly subject to manslaughter charges. Configuration management is the key to safety; yes, we are the watch dogs of safety.
My training as a nondestructive testing inspector started with mentors that were NDT inspectors during the USS Thresher’s shipyard work. One of these mentors shared with me the guilt he had due to him not being able to stop the higher ups from sending the Thresher out to sea that day. I have seen first-hand the heartbreak and torture my friend lived with for the rest of his life. I got the message, and was from then on, a stickler for assuring all the standards, requirements, and acceptance standards were correct. This carried over to my 30-year civilian career working for the government, aerospace, automotive and medical device companies.
Configuration management is the engineering development and testing of destruction of all parts, components, and systems until they fail. This is performed under the most extreme working conditions, such as temperature, humidity, tensile strength, toughness, hardness, pressure, etc. This process is called a verification and validation of its intended use.
Note: The owner of the product as defined on the engineering approval drawings / responsible company or agency are liable if something fails within the scope of the engineering design and development. Liability is the key to understanding quality assurance and quality inspections. We as quality professionals are the watch dogs with the training and understanding of the design and development of a product. Below is the Congressional Record of the USS Thresher tragedy and see all the wrongs that contributed to the loss of the USS Thresher. “The loss of Configuration” Management.
Caption
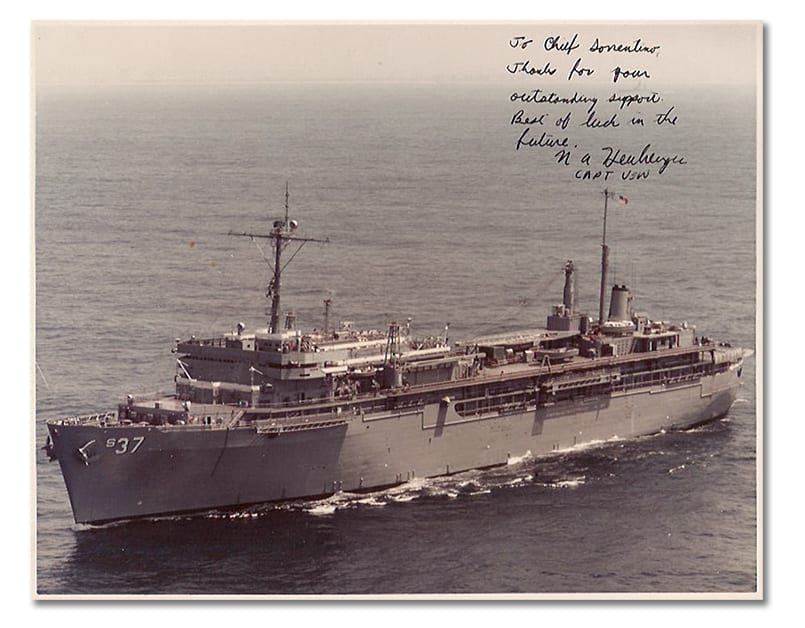
Reference: https://www.thresherbase.org/assets/subsfafe-radm-paul-e.-sullivan.pdf
Navy testimony before the Joint Committee on Atomic Energy occurred on June 26, 27, July 23, 1963 and July 1, 1964 and is a part of the Congressional Record.
“While the exact cause of the THRESHER loss is not recorded, from the facts gathered during the investigations, it is known that there were deficient specifications, deficient shipbuilding practices, deficient maintenance practices, and deficient operational procedures. Here’s what we think happened what is thought to have happened:
- THRESHER had about 3000 silver-brazed piping joints exposed to full submergence pressure. During her last shipyard maintenance period 145 of these joints were inspected on a not-to-delay vessel basis using a new technique called Ultrasonic Testing. Fourteen percent of the joints tested showed sub-standard joint integrity. Extrapolating these test results to the entire population of 3000 silver-brazed joints indicates that possibly more than 400 joints on THRESHER could have been sub-standard. One or more of these joints is believed to have failed, resulting in flooding in the engine room.
- The crew was unable to access vital equipment to stop the flooding.
- Saltwater spray on electrical components caused short circuits, reactor shutdown, and loss of propulsion power.
- The main ballast tank blow system failed to operate properly at test depth. It is believed that various restrictions in the air system coupled with excessive moisture in the system led to ice formation in the blow system piping. The resulting blockage caused an inadequate blow rate. Consequently, the submarine was unable to overcome the increasing weight of water rushing into the engine room.”
The USS Thresher was the first of the Thresher-class submarines. When the USS Thresher was lost, the Thresher class submarines were retrofitted to correct the known problems and was reclassified as the Permit-class submarines. Permit-class are nuclear-powered fast attack submarines in service with the United States Navy from early 1960’s until 1996. Thresher-class submarines were rebuilt to SUBSAFE standards. SUBSAFE includes specific training of SUBSAFE quality. Quality assurance inspectors are in the engineering crew, and track extremely detailed information about every component of a submarine that is subject to sea pressure. Joints in any equipment carrying seawater must be welded not brazed, and every hull penetration larger than a specified size can be quickly shut by a remote hydraulic mechanism.The program has been very successful, since to-date, there have been no SUBSAFE submarines lost.
Here is an example of configuration management and liability:
When you purchase a new car and it breaks down there is a warranty from the manufacturer within a certain number of miles. The manufacturer is responsible to fix it. On the other hand, if you choose to go to your local gas station for repairs—instead of the dealership—you will be the responsible party to pay for the repairs of your brake system. If the brakes fail, you will assume all the responsibility and cost of damage and possibly life loss. It’s as simple as that.
The Subsafe Program and the ISO 9001 Standard
The Nuclear Navy Subsafe Program was one of the foundations for ISO 9001 Quality Management. The International Quality Management ISO 9001 you see today was founded on The Subsafe Program, Mil-Q-9858 and BS5750 in 1987. The ISO 9001 is the foundation for specific aerospace, automotive and medical device requirements. All specific aerospace, automotive, and medical device requirements are added to the ISO 9001 using Italic and/or Bold print to address the specific requirement.
References:
- https://www.navsea.navy.mil/Media/News/Article-View/Article/3354927/uss-thresher-a-loss-a-legacy/ USS Thresher: A loss. A legacy.
- https://www.thresherbase.org/assets/subsfafe-radm-paul-e.-sullivan.pdf
Navy testimony before the Joint Committee on Atomic Energy occurred on June 26, 27, July 23, 1963 and July 1, 1964 and is a part of the Congressional Record.