PRESSES
John Sprovieri // Chief Editor
Here’s a look at the most common mistakes made with presses—and how to avoid them.
Common Mistakes With Presses
Jay-Cee Sales stocks nearly 10 million pounds of fasteners at its Farmington, MI, facility, including standard small rivets from numerous vendors. Photo courtesy Jay-Cee Sales & Rivet Inc.
Assemblers are well-advised to involve press suppliers early in the design process. Photo courtesy Promess Inc.
At first glance, press-fit assembly would seem to be much simpler than, say, welding or installing threaded fasteners. However, there’s a lot more to the process than simply jamming one part into another part. As with welding and fastening, assemblers must pick the right tool for the job; dial in the process parameters; and use the equipment correctly.
Dave Zabrosky, North American sales manager for Schmidt Technology, says a common misconception is that a servo press is necessary for force and distance monitoring.
“There’s a difference between process monitoring and process control,” he explains. “We do process monitoring on manual presses, hydraulic presses, pneumatic presses and servo presses. Monitoring measures what happens during the pressing operation. But, you look at the data after the fact.
“Servo presses are about control. They monitor the process, but they use that data as feedback to control the motion of the ram. A lot of times, that’s not what our customers need.
“For the most part, they want process monitoring for quality control. They want to be able to put tolerances on a force and distance curve to ensure that every part they produce is the same and to detect parts that are out of that range.”
Another common mistake, particularly with manual presses, is to choose the wrong type of press for the application, says Zabrosky. When selecting a press, engineers often look solely at the machine’s force capacity without considering how it actually delivers that force.
For example, a manual toggle press is a better option for crimping, staking and swaging applications, because it produces little force at the start of the stroke, but delivers maximum force at the end. A rank-and-pinion press produces constant force over the entire length of the stroke, so it’s a better option for pressing pins.
Similarly, a hydropneumatic press is a better choice for a punching operation over direct-acting pneumatic press, because a hydropneumatic press provides slower, smoother motion. A pneumatic press tends to punch through material hard and fast.
A third common mistake is trusting equations to provide guidance on how much force is needed for a particular application, especially for press-fit assembly.
See us at The Assembly Show, Booth 1831
“Calculations for blanking and other operations are pretty good, but for press-fit insertion…there are just too many variables that can influence the force requirement, such as surface finish, temperature changes and lubrication,” says Zabrosky. “The only way to know how much force is necessary is to test sample parts.”
Fortunately, most press suppliers are more than willing to help customers determine the parameters of their pressing application. All that’s needed are five or six sets of production-ready parts and, ideally, the tooling for the assembly, in case it has an influence on the operation.
“We help customers test their parts all the time,” says Zabrosky. “I have boxes of parts to test on my desk right now. And, unless we have to make custom tooling, we don’t charge to do testing.”
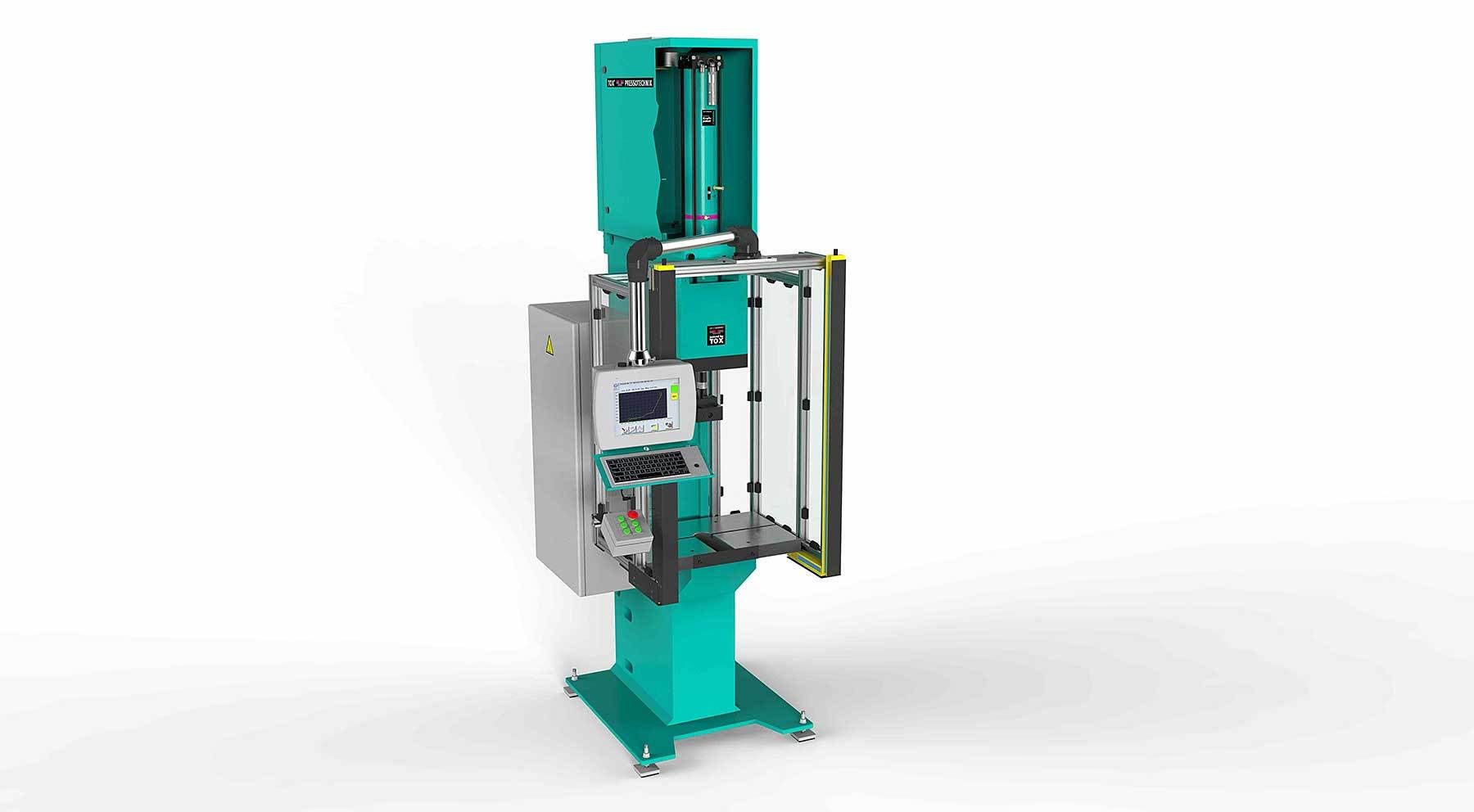
To avoid side-loading, align the ram to where maximum force is applied, rather than the physical center of a part. Photo courtesy TOX-Pressotechnik LLC
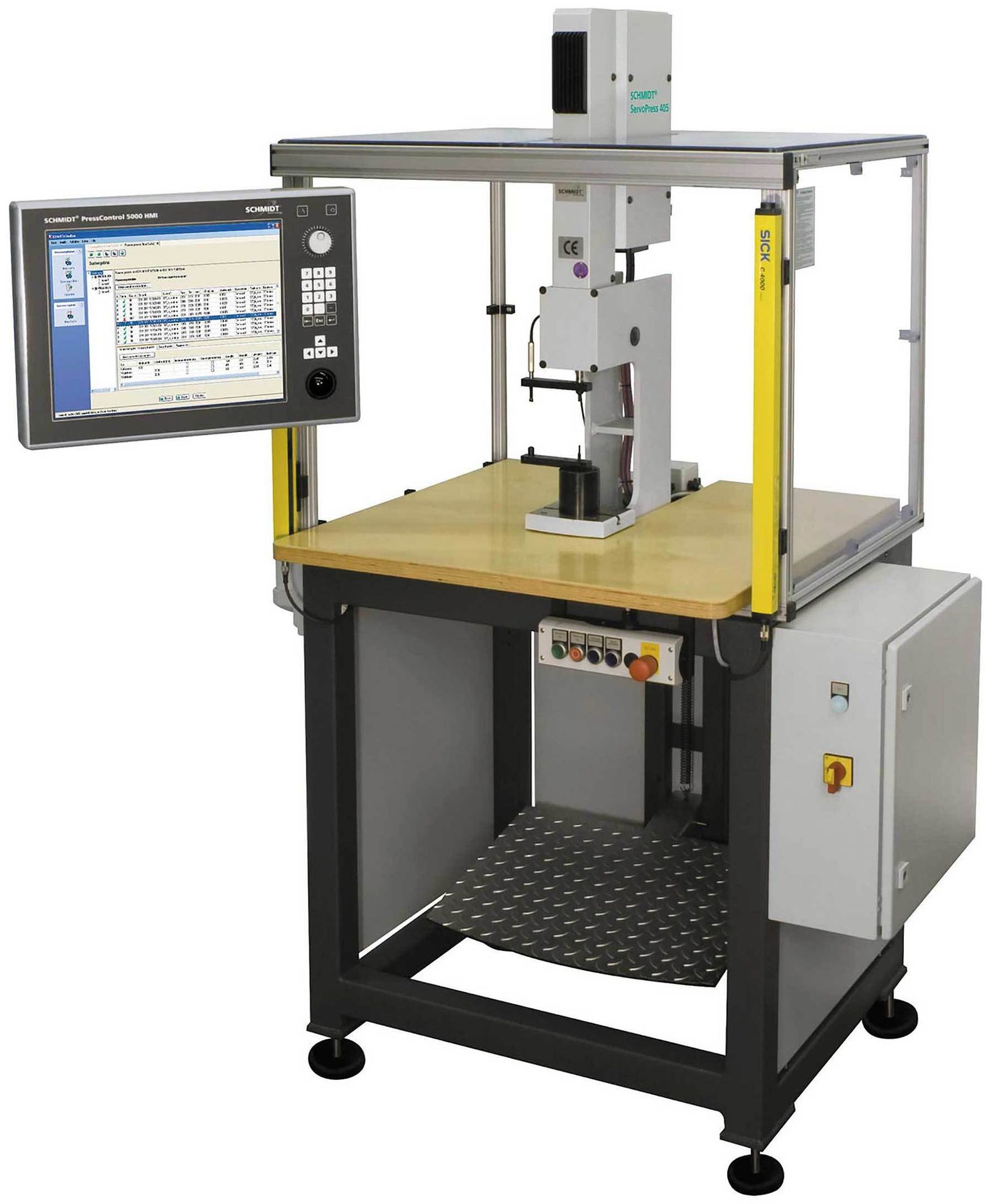
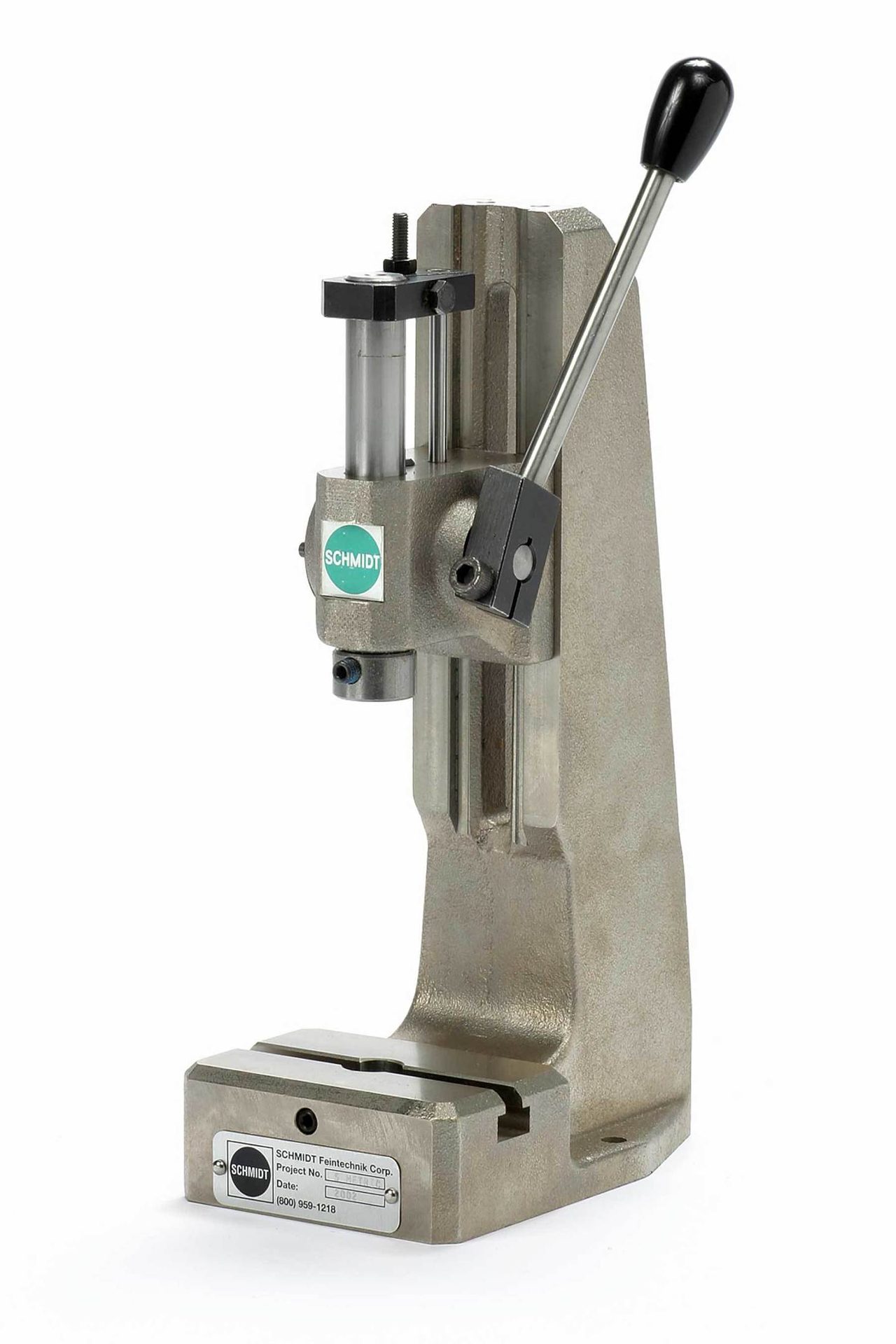
A common misconception is that a servo press is necessary for force and distance monitoring. However, there’s a difference between process monitoring and process control. Photo courtesy Schmidt Technology
When selecting a press, engineers often look solely at the machine’s force capacity without considering how it actually delivers that force. Photo courtesy Schmidt Technology
Glenn Nausley, president of Promess Inc., reiterates the importance of testing. Most mistakes with presses, he argues, begin before production even starts. Assemblers are well-advised to involve press suppliers early in the design process.
“When people buy our presses, we walk them through station design,” he says. “Our customers bring their parts and tooling, and we work through the process on our floor. We don’t see a lot of problems with our presses, because we are heavily involved in the integration. How are the parts going to go together? What are the key parameters and measurements that must be made? How can you tell a good part from a bad part? What data do you need to collect and how are you going to handle it?”
Nausley says a common mistake he sees is that assemblers don’t take maximize the capabilities of servo presses. “When manufacturers get a servo press for the first time, they often use it in the same way as a hydraulic or pneumatic press,” he explains. “They don’t take full advantage of the flexibility and capabilities of the press. With a servo system, you have force and position feedback. They’re tremendously accurate. You don’t need hard stops. You can have the ram come down at a high speed but then slow down for the pressing operation. You can get the part aligned and then speed up. They don’t realize that if they just added, say, a linear measurement probe, they could do the application in a much better way.”
See us at The Assembly Show, Booth 400
See us at The Assembly Show, Booth 351
Pressing the Right Way
Engineers should not trust equations to provide guidance on how much force is needed for a particular application, especially for press-fit assembly. The only way to know how much force is necessary is to test sample parts. Photo courtesy Promess Inc.
Of course, even the best equipment and the best-designed parts and processes will come to naught if they’re not run and maintained properly.
Troy Waldherr, vice president sales and operations at TOX-Pressotechnik LLC, says the most common mistakes he sees concern presses that are already on the line. He points out the following:
Zabrosky echoes the latter two points. “A common mistake is to assume that what you have is what you need,” he says. “Don’t try to use a 6-ton press to insert a pin just because you happen to have one on the shop floor. You also want to match the load cell to the application. The accuracy and resolution of a load cell is based on its capacity. A load cell that is oversized or undersized will not provide accurate readings.”
Users removing or overriding safety devices, creating injury risk.
Aligning the press ram to the physical center of a part instead of to where the maximum force is applied. “These are not always the same,” he explains. “Misalignment can cause side-loading, which can damage the press or the parts, and create a safety hazard.”
Overtaxing a press: turning up the power to drive a press over its rated capacity. This could damage the press and create a safety hazard.
Using an existing, oversized press to assemble small parts instead of buying a smaller press that is better matched to the application. An oversized press can damage the parts and tooling.
ASSEMBLY ONLINE
For more information on assembly presses, visit www.assemblymag.com to read these articles: