robotics
John Sprovieri // Chief Editor
Whether the application involves a standard robot or a cobot, engineers must do a risk assessment to identify potential hazards.
How to Conduct a Robot Risk Assessment
Jay-Cee Sales stocks nearly 10 million pounds of fasteners at its Farmington, MI, facility, including standard small rivets from numerous vendors. Photo courtesy Jay-Cee Sales & Rivet Inc.
The Industrial Robot Safety Standard, ANSI/RIA R15.06-2012, requires that a risk assessment be carried out on every robotic system. Photo courtesy RoboDK Inc.
At the Moscow Chess Open in July, a tabletop six-axis robot equipped with a two-finger gripper was programmed to play chess with three opponents simultaneously. During one match, an overenthusiastic seven-year-old boy reached for a piece before allowing the robot to complete its move. Suddenly, the gripper closed on the boy’s finger and broke it. After a brief struggle, several bystanders helped to free the child’s hand and take him away from the table.
“A robot broke a child’s finger—this is, of course, bad,” says Sergey Lazarev, president of the Moscow Chess Federation. Fortunately, the boy was otherwise unharmed, and he continued to compete in the tournament after his finger was put in a cast.
“We will coordinate to understand what happened and try to help [the family] in any way we can,” adds Lazarev. “And, the robot’s operators, apparently, will have to think about strengthening protection so that such a situation does not happen again.”
The incident underscores the importance of doing a thorough risk assessment on every robot application, regardless of where or how the machine is deployed. Even seemingly benign applications—a small robot, moving at slow speeds, carrying a small payload—can cause serious injury.
With robots becoming ever more ubiquitous on the assembly line—a record high 11,595 robots, valued at $646 million, were sold in North America in the first quarter of 2022, according to the Association for Advancing Automation (A3)—engineers might be tempted to take a blasé attitude toward the technology. That, warns Jerry Perez, executive director for global accounts at FANUC America Corp., is a recipe for disaster. The cost in legal risk, OSHA fines, insurance premiums, and employee retention can be immense if a workplace is not as safe as possible.
See us at The Assembly Show, Booth 441
“The most difficult part of doing a risk assessment is actually getting people to do it,” he observes. “It takes time. It can take several hours to evaluate a process and rate all the potential hazards. It can be hard. After doing an assessment, you might even conclude that you need more safety equipment than you originally planned or budgeted for. But, at the end of the day, safety is paramount.”
The increasing popularity of collaborative robots has added a layer of complexity to the challenge. A major selling point of cobots is that they can work side by side with people; there’s no need to wall off the machines with fencing or Plexiglas. At least, that’s what the catalog says. The reality is more complex. A cobot equipped with a high-speed deburring tool is not as safe as one equipped with a small vacuum gripper.
Whether the application involves a standard robot or a cobot, engineers must do a risk assessment to identify potential hazards and mitigate the risk of injury.
Step by Step
The approach to risk assessment doesn’t necessarily change if the operation is performed by a cobot rather than a standard robot. Photo courtesy FANUC America Corp.
The Industrial Robot Safety Standard, ANSI/RIA R15.06-2012, requires that a risk assessment be carried out on every robotic system. This includes determining what the robot will be used for, a risk analysis, hazard identification, risk estimation and risk evaluation.
The first step in the process is to do a risk analysis. This requires engineers to identify tasks, hazards, risk levels, and the performance level and category of safeguards needed for compliant risk mitigation.
Engineers must identify potential hazards associated with each step in a production process and assign a value to the hazard. All the robot’s motions and actions must be separated into potential risks. Any potential interaction between a person and a robot is a risk, and each risk gets a grade. A pick-and-place operation with a vacuum suction cup gripper would have a lower hazard value than an arc-welding operation.
“What’s the robot doing? How fast is it moving? The robot might be picking up a part and placing it somewhere. Can a worker’s hand get in the way? Are there pinch points? Are there places where someone could get cut? Are there electrical hazards?” says Perez. “You even need to think about noise. An abrasive disk spinning at 10,000 rpm is pretty loud.”
Engineers also must consider how often a risk might happen. What’s the likelihood of an adverse event happening? Could it happen once a shift? Once a week? Or one time in a million opportunities?
See us at The Assembly Show, Booth 1902
“Sometimes you need to consider silly or improbable scenarios,” says Perez. “I remember an application in which a truck cab entered a robot cell. The cell was equipped with safety gates to keep personnel out while the robots were doing their job. Once the cab entered the cell, it was impossible for a worker to enter the cell. Then someone suggested, what if someone was inside the cab when it entered the cell?
“We thought, ‘That’s just silly. No one’s going to do that.’ But, it could happen. So we installed a sensor to detect if the cab is occupied before it enters the cell.”
Standardized spreadsheets and templates based on international safety standards are available to keep subjectivity out of the ratings. They define and grade various risks: mechanical, electrical, thermal, vibrational and sonic. Numerical values help to prioritize actions. Such values are based on:
The degree of possible harm (bruise, cut, fracture, death).
The possibility of the hazard occurring (almost impossible, unlikely, possible, probable, certain).
The possibility of avoidance (possible, possible under certain circumstances, impossible).
The frequency of exposure (annually, monthly, weekly, daily, hourly, constantly)
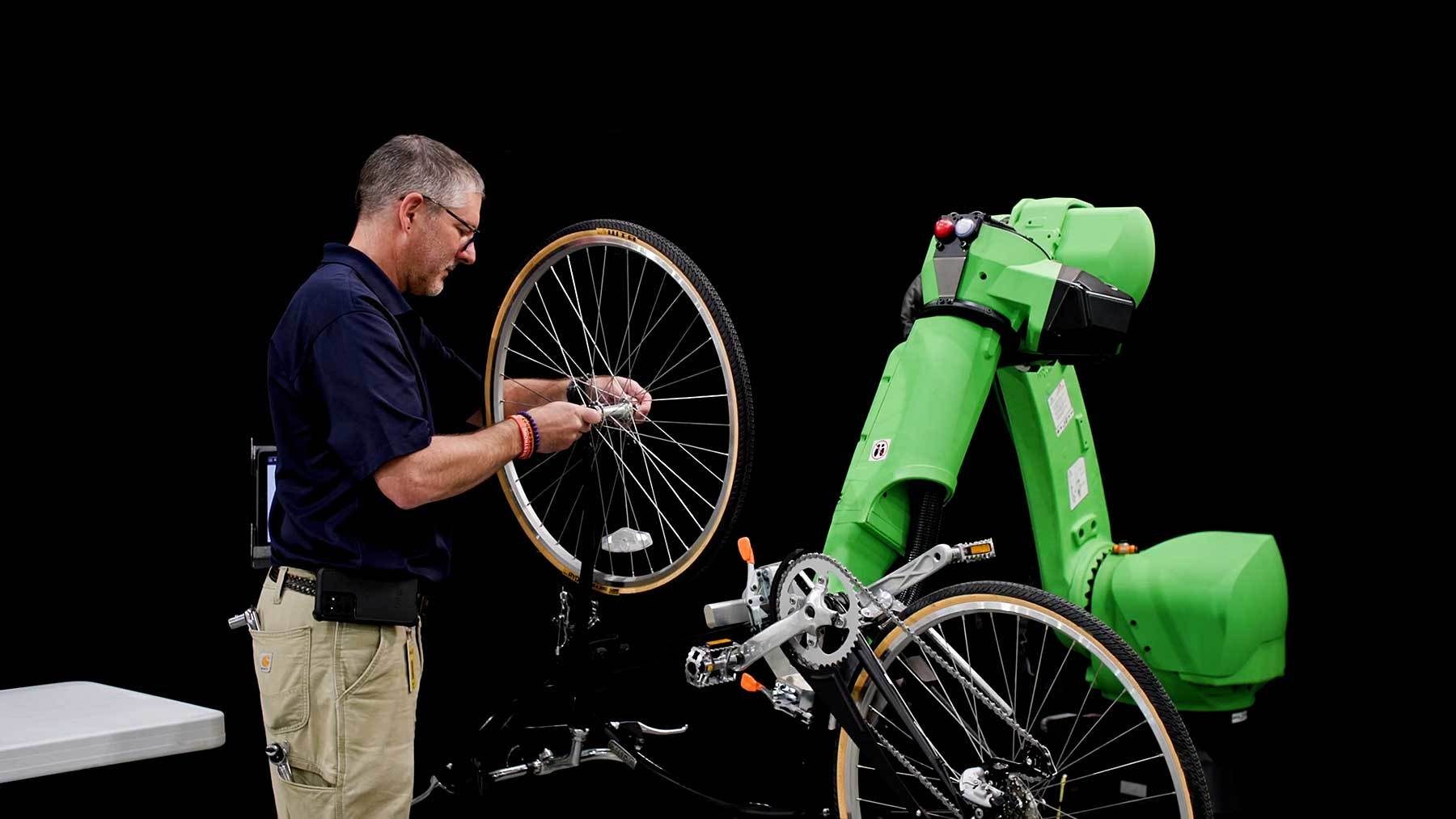
While cobots are designed to work alongside people, engineers still need to conduct a risk assessment to ensure safety. Photo courtesy FANUC America Corp.
A team effort helps to ensure that nothing is overlooked. “You want all the stakeholders involved—whoever is close to the machine,” advises Perez. “You want to include operators, maintenance personnel, your safety team, and your vendors.”
Perez notes that the approach to risk assessment doesn’t necessarily change if the operation is performed by a cobot rather than a standard robot.
“Let’s say the robot is picking and placing a 20-pound box,” he explains. “Whether it’s a cobot or a robot, you must make sure that the tool gripping the box won’t accidentally drop it on someone’s foot. You have to make sure that no one will get in the way while the robot is moving the box.”
Once all the risks are rated, they can be ranked in order from the most dangerous to least dangerous. After that, engineers must evaluate each risk and determine if it is acceptable for the application or not. If the risk is acceptable, nothing more need be done. If not, engineers will need to integrate safety measures or change something in the application to make it safer.
Once risks and hazards have been identified and ranked, engineers can devise a risk mitigation plan. As with the initial assessment, a collaborative effort is the best way to determine what risk reduction methods are best suited for a particular process.
With a plan in place, engineers can begin designing a system to achieve functional safety. This can include guarding, programmable logic controllers, light curtains, safety switches, laser scanners, safety-rated embedded software, safety-rated application software, and safety and supervisory networking.
Once safety systems are in place, the final step is to validate that the intended level of safety performance has been achieved. Engineers must restart the risk assessment process all over again to ensure that their modifications work as intended and did not actually make the cell more dangerous.
Help Is Available
Engineers must identify potential hazards associated with each step in a production process and assign a value to the hazard. A pick-and-place operation with a vacuum suction cup gripper would have a lower hazard value than an arc-welding operation. Photo courtesy GT Engineering
If conducting a risk assessment seems daunting, help is available, some of it at little or no cost.
Engineering firms, such as Automation Rangers Inc. of Fairfield, OH, or ProSafe Inc. of Stratford, ON, Canada, specialize in safety reviews and compliance evaluations.
For engineers who want to do it themselves, software is available to guide them through the process.
Robot Safety Center from Safety Center Inc. is task-based risk assessment software. It delivers a clear, easy-to-understand, consistent methodology for reducing risk to an acceptable level. The software helps engineers to identify tasks, associate them with hazards, and select performance levels, safeguards and complementary protective measures. Verification and validation modules are included. Versions are available for the following safety standards: RIA TR R15.306-2016, ANSI B11.0-2015 and ISO 12100:2010.
Designsafe 8 from Design Safety Engineering Inc. enables engineers to identify hazards, assess risk for identified hazards; and reduce risks in a structured method. Shortcuts and guidance documents provide advice on how to stay out of the weeds when doing a risk assessment. Compatible with Windows 8, the software includes a control system assessment, a dynamic checklist, and risk reduction measure updates. The software can be used on smartphones or tablets, so engineers can start a risk assessment on the shop floor, or capture a hazard and assess it on the spot.
Several companies offer Excel spreadsheets that help engineers identify and rank hazards. Such spreadsheets reduce the subjectivity of the risk assessment process. Photo courtesy RoboDK Inc.
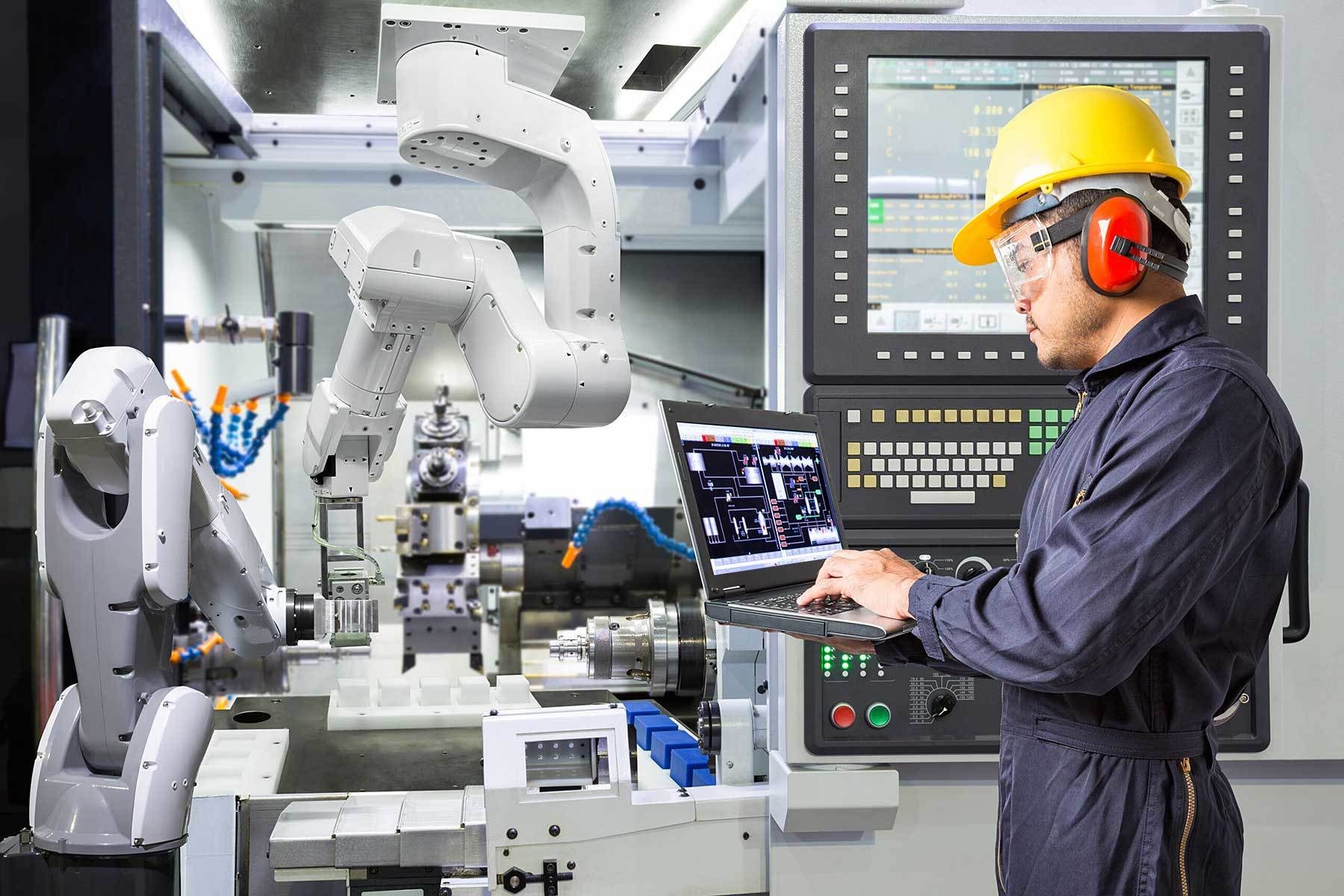
Several companies, such as Machine Safety Specialists, offer Excel spreadsheets that help engineers identify and rank hazards. Such spreadsheets reduce the subjectivity of the risk assessment process.
For its part, the A3 provides several training opportunities focused on robot safety. For example, the association’s International Robot Safety Conference will take place Sept. 27-29 in Columbus, OH. It’s the first time since 2019 that the conference will be held in-person.
Don’t want to travel? The A3 offers two virtual training programs: “Robot Safety and Risk Assessment” and “Robot Safety for Collaborative Applications.” Both are taught by live instructors. The former consists of two half-day sessions; the latter is one half-day program. The association also offers in-house training on risk assessment and robot safety.
ASSEMBLY ONLINE
For more information on robots and safety, visit www.assemblymag.com to read these articles: